Physical Vapor Deposition (PVD) is a vacuum-based technology used to deposit thin films of materials onto a substrate. It involves converting target materials into gaseous atoms, molecules, or ions, which then condense onto the substrate to form a thin, uniform coating. PVD is widely used across industries such as semiconductor manufacturing, aerospace, automotive, biomedical, and decorative applications. It offers advantages like enhanced durability, corrosion resistance, and environmental friendliness compared to traditional coating methods like chrome plating. PVD coatings are applied in various forms, ranging from nanometers to micrometers, and are used in products like solar panels, cutting tools, medical devices, and decorative hardware.
Key Points Explained:
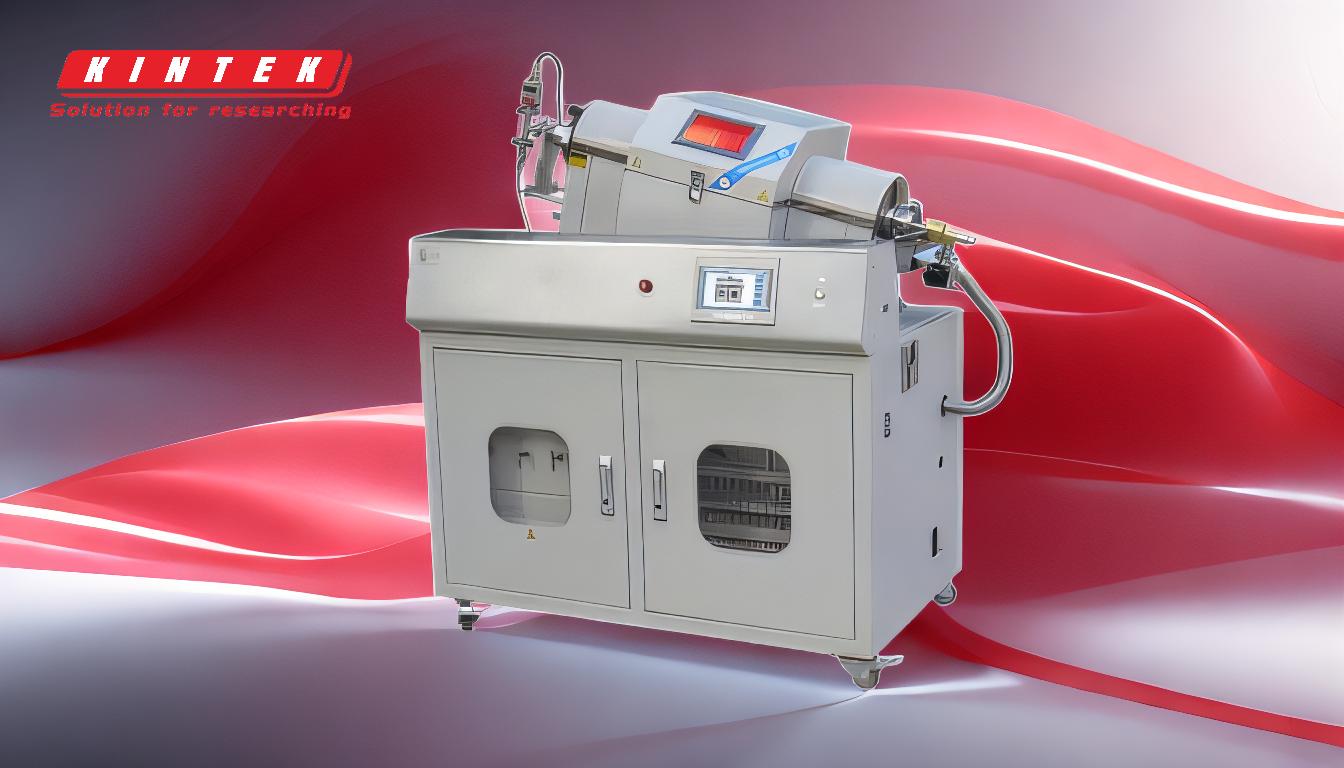
-
Definition of PVD:
- PVD is a vacuum-based process where target materials are vaporized into atoms, molecules, or ions and then deposited onto a substrate to form a thin film.
- It is a clean and precise method for creating coatings with specific mechanical, optical, chemical, or electronic properties.
-
How PVD Works:
- The process begins in a vacuum chamber to minimize contamination and ensure a clean deposition environment.
- The target material is vaporized using techniques such as sputtering, evaporation, or ion plating.
- The vaporized material then travels through the vacuum and condenses onto the substrate, forming a thin, uniform layer.
-
Applications of PVD:
- Semiconductor and Electronics: Used in the production of microchips, thin-film solar panels, and semiconductor devices.
- Cutting Tools and Industrial Equipment: Enhances the durability and performance of tools like drill bits and titanium nitride-coated cutting tools.
- Automotive and Aerospace: Extends the lifespan of car parts (e.g., wheels, pistons) and improves the performance of aerospace components.
- Medical Devices: Provides corrosion resistance and biocompatibility for surgical tools and implants.
- Decorative and Functional Finishes: Used in jewelry, door and window hardware, and self-cleaning tinted windows.
- Optics and Photovoltaics: Applied in anti-reflection coatings, optical lenses, and solar panels.
-
Advantages of PVD Coatings:
- Durability: PVD coatings can extend the lifespan of products by up to ten times, with some coatings lasting over 25 years.
- Corrosion Resistance: Provides excellent protection against wear and environmental degradation.
- Environmental Benefits: PVD is a greener alternative to chrome plating, as it avoids the use of toxic chemicals.
- Versatility: Can be used with a wide range of materials, including metals, ceramics, and polymers.
-
Types of PVD Techniques:
- Sputtering: A method where high-energy ions bombard the target material, ejecting atoms that deposit onto the substrate.
- Evaporation: The target material is heated until it vaporizes, and the vapor condenses onto the substrate.
- Ion Plating: Combines evaporation and sputtering, with the substrate being bombarded by ions to improve adhesion and film quality.
-
Material and Thickness Range:
- PVD coatings can range from a few nanometers to micrometers in thickness.
- They are used for multilayer coatings, graded compositions, and hybrid deposition techniques.
-
Industries Benefiting from PVD:
- Hardware and Decorative Products: Popular in the manufacturing of lamps, jewelry, and handicrafts.
- Biomedical and Research: Used in medical devices, corrosion research, and surface-enhanced Raman scattering (SERS) studies.
- High-Performance Applications: Essential in aerospace, automotive, and optical industries for advanced material properties.
-
Future Trends and Innovations:
- PVD technology continues to evolve, with advancements in hybrid deposition techniques and the development of new materials for specialized applications.
- Its role in sustainable manufacturing is growing, as industries seek eco-friendly alternatives to traditional coating methods.
By understanding the principles, applications, and benefits of PVD, manufacturers and consumers can make informed decisions about its use in various industries, ensuring enhanced performance and sustainability.
Summary Table:
Aspect | Details |
---|---|
Definition | Vacuum-based process for depositing thin films of materials onto substrates. |
Applications | Semiconductor, aerospace, automotive, medical devices, decorative finishes. |
Advantages | Durability, corrosion resistance, environmental friendliness, versatility. |
Techniques | Sputtering, evaporation, ion plating. |
Thickness Range | Nanometers to micrometers. |
Industries | Semiconductor, aerospace, automotive, biomedical, optics. |
Future Trends | Hybrid deposition techniques, sustainable manufacturing advancements. |
Ready to explore how PVD can transform your products? Contact us today for expert guidance!