Physical Vapor Deposition (PVD) is a technique used to create thin films on substrates through physical processes, typically in a vacuum environment. It involves transforming a solid target material into a vapor, which then condenses onto a substrate to form a thin film. PVD is widely used in industries such as microelectronics, machining, and optics due to its ability to produce highly precise, uniform, and durable coatings. The process is environmentally friendly and results in coatings that are hard, corrosion-resistant, and capable of withstanding high temperatures. Common PVD methods include sputtering and evaporation, which are essential for applications like semiconductor devices, cutting tools, and food packaging.
Key Points Explained:
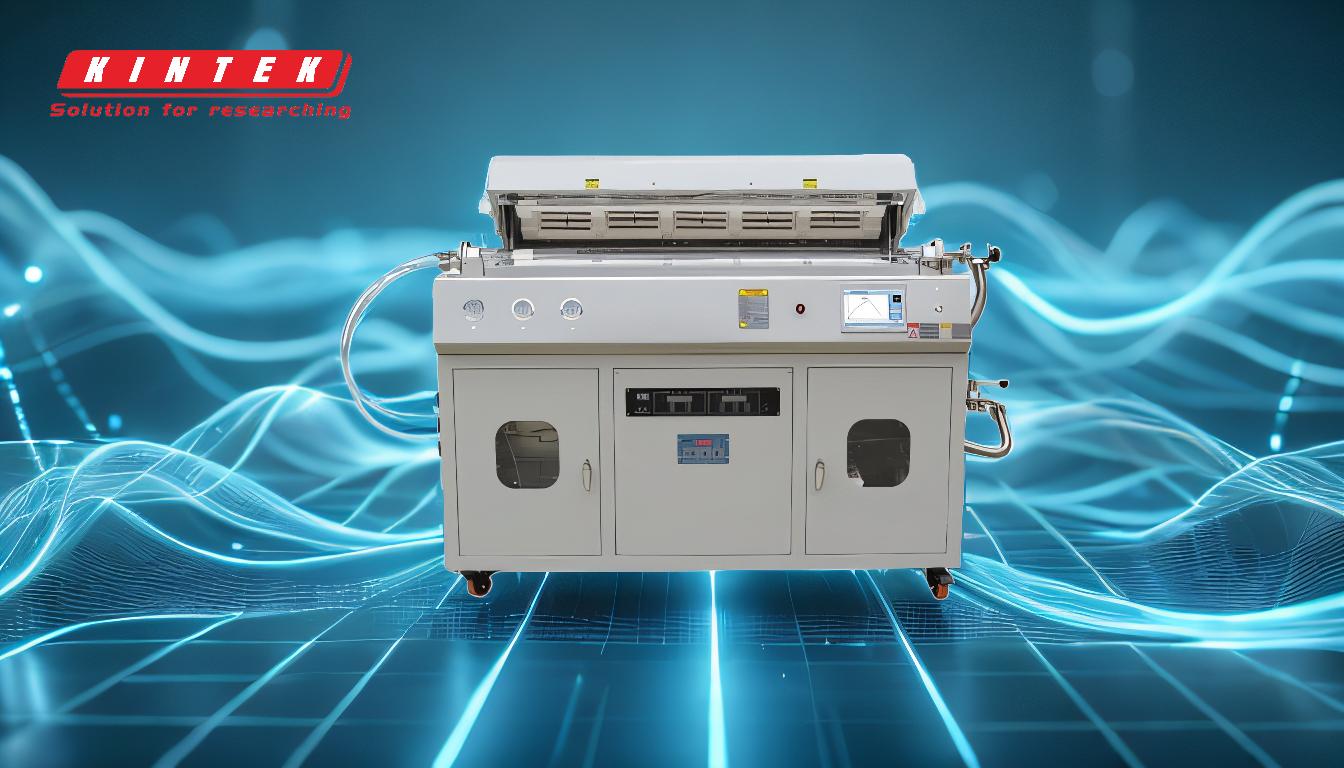
-
What is PVD?
- PVD (Physical Vapor Deposition) is a vacuum-based process used to deposit thin films onto substrates. It involves converting a solid target material into a vapor phase, which then condenses onto the substrate to form a thin, uniform coating. This technique is widely used for its ability to produce coatings with exceptional hardness, corrosion resistance, and high-temperature tolerance.
-
How Does PVD Work?
- The PVD process typically occurs in a vacuum chamber to ensure minimal contamination and precise control over the deposition. The target material is vaporized using methods like sputtering or evaporation. In sputtering, a gas like argon is ionized, and the resulting ions bombard the target, dislodging atoms that deposit onto the substrate. In evaporation, the target material is heated until it vaporizes and then condenses onto the substrate.
-
Applications of PVD:
- PVD is used in a wide range of industries due to its versatility and precision. Key applications include:
- Microelectronics: Thin-film solar cells, semiconductor devices, and microelectromechanical systems (MEMS).
- Machining: Titanium nitride-coated cutting tools for improved durability and performance.
- Food Packaging: Aluminized PET films for extended shelf life and barrier properties.
- Optics and Glass: Coatings for architectural glass, displays, and entertainment electronics like CDs and DVDs.
- PVD is used in a wide range of industries due to its versatility and precision. Key applications include:
-
Advantages of PVD:
- PVD offers several benefits, making it a preferred method for thin-film deposition:
- Durability: Produces extremely hard and wear-resistant coatings.
- Corrosion Resistance: Ideal for applications requiring long-term protection against environmental factors.
- High-Temperature Tolerance: Suitable for use in high-temperature environments.
- Environmental Friendliness: Unlike some chemical processes, PVD is considered environmentally friendly due to minimal waste and hazardous by-products.
- PVD offers several benefits, making it a preferred method for thin-film deposition:
-
Comparison with Other Techniques:
- PVD is often compared with Chemical Vapor Deposition (CVD), another thin-film deposition method. While CVD involves chemical reactions to deposit films, PVD relies on physical processes. PVD is typically performed at lower temperatures and is better suited for materials that cannot withstand the high temperatures required for CVD. Additionally, PVD coatings are often denser and more uniform than those produced by CVD.
-
Common PVD Methods:
- The two most widely used PVD techniques are:
- Sputtering: A process where ions bombard a target material, causing atoms to dislodge and deposit onto a substrate. This method is highly precise and is used in applications like semiconductor manufacturing.
- Evaporation: Involves heating the target material until it vaporizes, with the vapor then condensing onto the substrate. This method is often used for optical coatings and decorative finishes.
- The two most widely used PVD techniques are:
-
Role of Microwave Plasma Chemical Vapor Deposition:
- While PVD primarily involves physical processes, techniques like microwave plasma chemical vapor deposition (MPCVD) combine aspects of both PVD and CVD. MPCVD uses plasma generated by microwaves to enhance chemical reactions, allowing for the deposition of high-quality thin films at lower temperatures. This method is particularly useful for depositing diamond-like carbon (DLC) films and other advanced materials.
-
Future Trends in PVD:
- The demand for PVD coatings is expected to grow, driven by advancements in nanotechnology, renewable energy, and electronics. Innovations in PVD equipment and processes, such as hybrid techniques combining PVD and CVD, are likely to expand its applications further.
By understanding the principles, methods, and applications of PVD, manufacturers and researchers can leverage this technology to create high-performance thin films for a variety of industries.
Summary Table:
Aspect | Details |
---|---|
What is PVD? | Vacuum-based process for depositing thin films via physical vaporization. |
How It Works | Uses sputtering or evaporation to deposit vaporized material onto substrates. |
Applications | Microelectronics, machining, food packaging, optics, and glass coatings. |
Advantages | Durable, corrosion-resistant, high-temperature tolerant, eco-friendly. |
Common Methods | Sputtering and evaporation. |
Comparison with CVD | Performed at lower temperatures; denser, more uniform coatings. |
Future Trends | Growth driven by nanotechnology, renewable energy, and electronics. |
Discover how PVD can revolutionize your thin-film applications—contact our experts today!