Sintering in a blast furnace is a critical process in steel production, where iron ore powder, fluxes, and recycled materials are transformed into sinter, a dense and consistent material optimized for use in the blast furnace. The process involves heating the mixture below its melting point to fuse particles, creating a strong, porous structure. This sinter improves blast furnace efficiency by enhancing permeability, reducing the coking ratio, and ensuring smooth furnace operation. The sintering process not only strengthens the material but also reduces porosity, making it ideal for ironmaking. It is a cost-effective method for producing high-quality materials with desirable mechanical properties.
Key Points Explained:
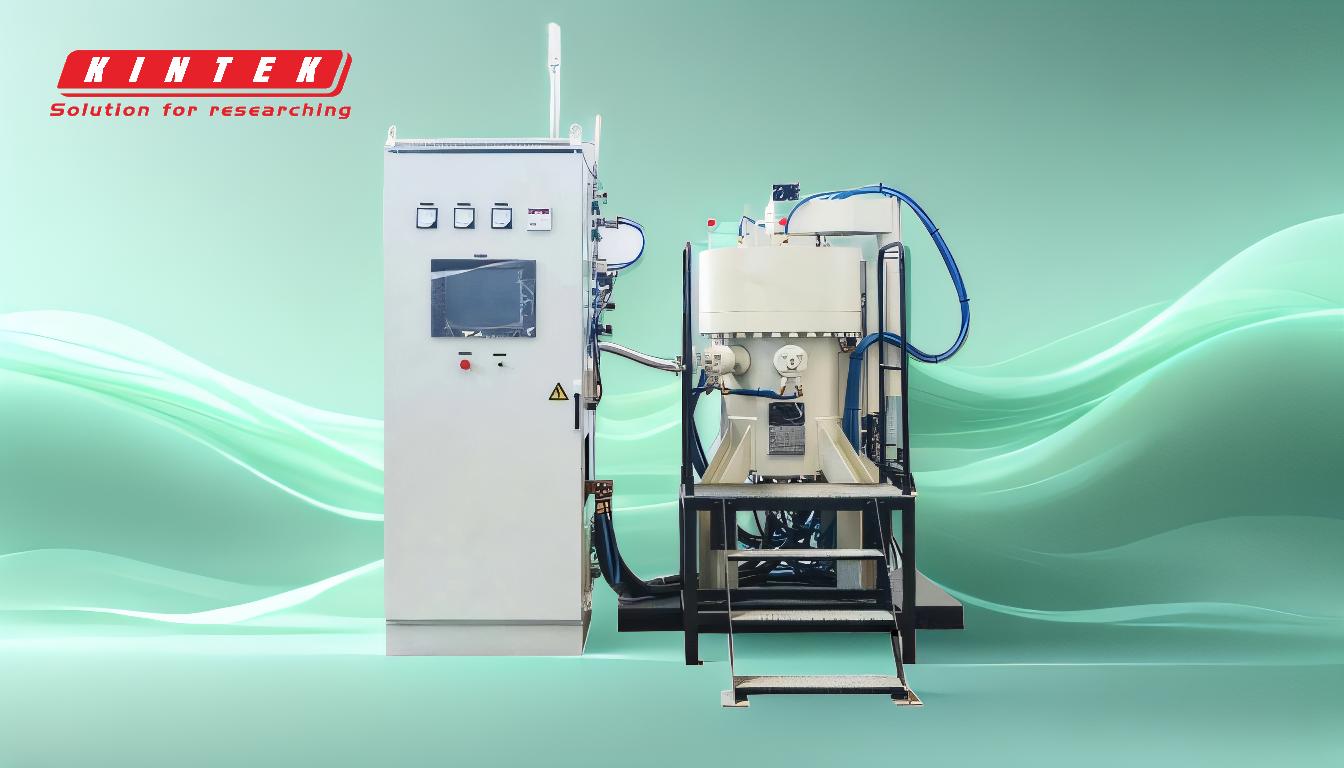
-
Definition and Purpose of Sintering in Blast Furnaces:
- Sintering is the process of transforming powdery materials, such as iron ore, into a dense, consistent product called sinter.
- The primary purpose is to create a material that optimizes blast furnace performance by improving permeability, reducing the coking ratio, and enhancing furnace efficiency.
-
Materials Used in the Sintering Process:
- Iron ore powder: The primary raw material.
- Fluxes: Materials like limestone or dolomite that help remove impurities.
- Recycled substances: Waste materials from steel plants, such as dust and slag, are reused to reduce waste and costs.
- Non-tobacco coal: Used as a fuel source to provide heat for the sintering process.
-
Stages of the Sintering Process:
- Mixing and Blending: Iron ore powder, fluxes, and recycled materials are mixed in specific ratios to ensure uniformity.
- Formation of Green Sinter: The mixture is shaped into a desired form, often using a bonding agent like wax or polymer to hold the particles together.
- Heating and Firing: The green sinter is heated in a furnace at temperatures below the melting point of the materials. The bonding agent evaporates or burns away, and the particles begin to fuse at their surfaces.
- Cooling and Crushing: After sintering, the material is cooled, crushed, and screened to remove dust and achieve the desired granularity.
-
Key Benefits of Sintering in Blast Furnaces:
- Improved Blast Furnace Efficiency: Sinter enhances the permeability of the blast furnace, allowing for smoother operation and better gas flow.
- Reduced Coking Ratio: Sinter reduces the amount of coke required in the blast furnace, lowering production costs.
- Enhanced Material Properties: Sintering imparts strength, reduces porosity, and improves the mechanical properties of the material, such as hardness and toughness.
- Cost-Effectiveness: The use of recycled materials and lower energy requirements make sintering an economical process.
-
Applications of Sintering in Metallurgy:
- Sintering is widely used in the production of metal components such as gears, bearings, bushings, and automotive parts.
- It enables the creation of intricate shapes and geometries that are difficult to achieve with traditional manufacturing methods.
- Sintering combines the properties of multiple materials, such as toughness and abrasion resistance, to produce high-performance components.
-
Importance of Sintering in Steel Production:
- Sintering is a crucial step in the steel production process, as it ensures the production of high-quality sintered ore with sufficient strength and granularity.
- It contributes to the overall efficiency and sustainability of steel production by reducing waste and improving resource utilization.
By understanding the sintering process in blast furnaces, manufacturers can optimize their operations, reduce costs, and produce high-quality materials that meet the demands of modern steel production.
Summary Table:
Aspect | Details |
---|---|
Definition | Process of transforming powdery materials into dense, consistent sinter. |
Purpose | Improves blast furnace efficiency, reduces coking ratio, and enhances operation. |
Materials Used | Iron ore powder, fluxes (limestone/dolomite), recycled substances, coal. |
Stages | Mixing & blending, green sinter formation, heating & firing, cooling & crushing. |
Key Benefits | Enhanced permeability, reduced coking ratio, improved material properties. |
Applications | Gears, bearings, automotive parts, and intricate metal components. |
Importance | Crucial for high-quality sintered ore, cost-effectiveness, and sustainability. |
Discover how sintering can revolutionize your steel production—contact our experts today!