Solid-state sintering is a process used to transform powdered materials into dense, solid bodies by applying heat and pressure at temperatures below the material's melting point. This method relies on atomic diffusion between particles, which leads to the formation of bonds and densification. The process is widely used in industries such as powder metallurgy and ceramics to create strong, durable, and structurally sound materials. Solid-state sintering is particularly useful for materials with high melting points, as it avoids liquefaction while achieving the desired properties.
Key Points Explained:
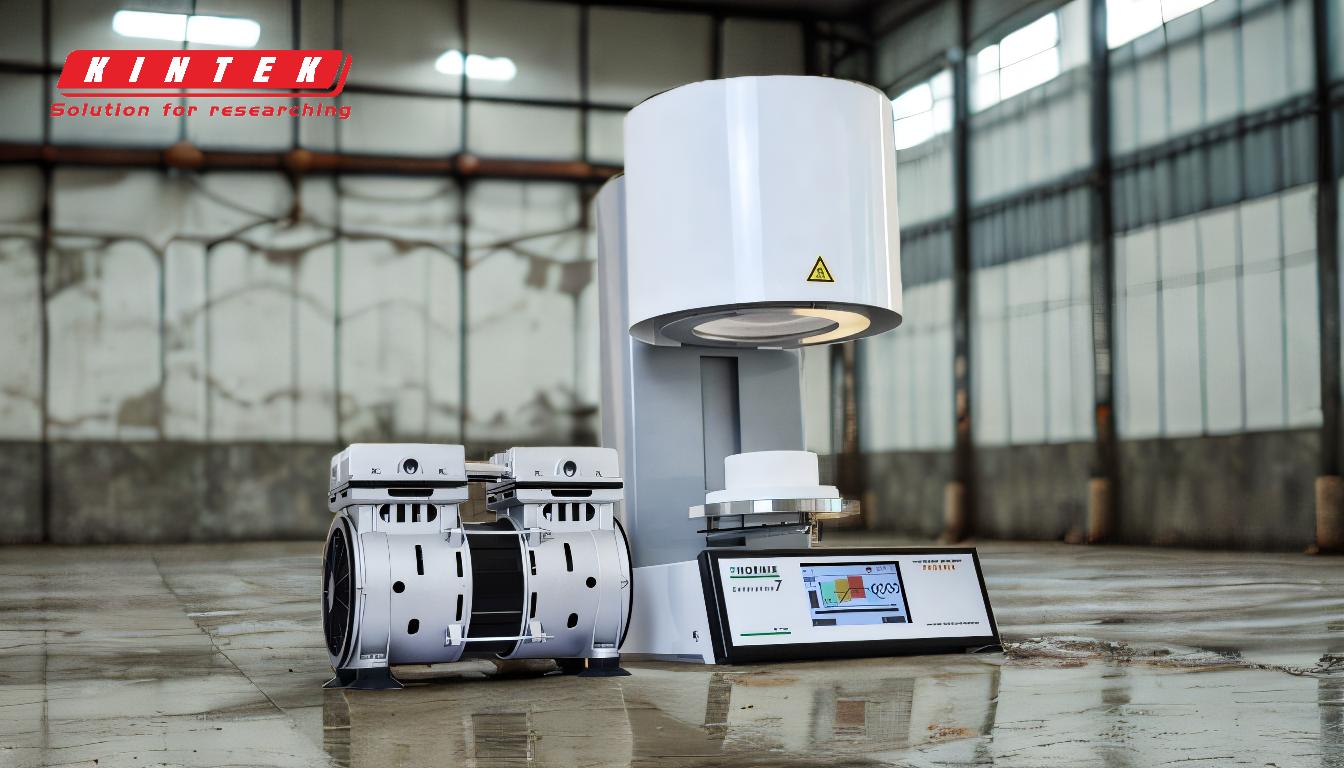
-
Definition of Solid-State Sintering:
- Solid-state sintering is a process where powdered materials are heated to temperatures below their melting points, allowing atomic diffusion to occur between adjacent particles.
- This diffusion leads to the formation of "necks" (bonded regions) between particles, which ultimately results in densification and the creation of a solid mass.
-
Key Components of the Process:
- Powdered Materials: The process begins with loose powder or pre-shaped powder compacts.
- Controlled Atmosphere: Sintering typically occurs in a controlled environment to prevent contamination and ensure consistent results.
- Temperature and Time: The material is heated to a specific temperature (below its melting point) and held there for a predetermined period (sintering time) to achieve the desired densification.
-
Mechanism of Solid-State Sintering:
- Atomic Diffusion: At elevated temperatures, atoms in the powder particles gain enough energy to move across particle boundaries, leading to bonding.
- Neck Formation: As diffusion progresses, bonds form between particles, creating necks that reduce porosity and increase density.
- Densification: Over time, voids between particles are eliminated, and the material becomes a cohesive, solid mass.
-
Applications of Solid-State Sintering:
- Powder Metallurgy: Used to create metal components with high strength and durability, such as gears, bearings, and cutting tools.
- Ceramics: Applied in the production of pottery, tiles, and advanced ceramics for industrial and electronic applications.
- High-Melting-Point Materials: Ideal for materials like tungsten and molybdenum, which have extremely high melting points and are difficult to process using traditional melting techniques.
-
Advantages of Solid-State Sintering:
- Avoids Melting: Since the process occurs below the melting point, it prevents material liquefaction, making it suitable for high-melting-point materials.
- Improved Properties: The resulting material is stronger, harder, and more durable due to the elimination of voids and the formation of strong atomic bonds.
- Cost-Effective: Sintering is often more economical than melting and casting, especially for complex shapes and high-performance materials.
-
Challenges and Considerations:
- Temperature Control: Precise control of temperature and sintering time is critical to achieving the desired properties.
- Material Selection: Not all materials are suitable for solid-state sintering; the process works best with powders that can undergo atomic diffusion at the sintering temperature.
- Porosity Management: While sintering reduces porosity, achieving full densification can be challenging, especially for materials with irregular particle sizes.
-
Comparison to Other Sintering Methods:
- Liquid-Phase Sintering: In this method, a small amount of liquid phase is introduced to aid densification. Solid-state sintering, in contrast, relies solely on atomic diffusion without any liquid phase.
- Hot Pressing: Combines sintering with external pressure to accelerate densification. Solid-state sintering typically uses only heat, though pressure may be applied in some cases.
-
Industrial Relevance:
- Solid-state sintering is a cornerstone of modern manufacturing, enabling the production of high-performance materials that are difficult or impossible to create using traditional methods.
- Its ability to produce complex shapes with minimal material waste makes it a preferred choice for industries requiring precision and efficiency.
By understanding these key points, equipment and consumable purchasers can make informed decisions about the suitability of solid-state sintering for their specific needs, ensuring optimal material performance and cost-effectiveness.
Summary Table:
Aspect | Details |
---|---|
Definition | Heating powdered materials below melting point for atomic diffusion. |
Key Components | Powdered materials, controlled atmosphere, precise temperature & time. |
Mechanism | Atomic diffusion, neck formation, and densification. |
Applications | Powder metallurgy, ceramics, high-melting-point materials. |
Advantages | Avoids melting, improves material properties, cost-effective. |
Challenges | Temperature control, material selection, porosity management. |
Comparison | Differs from liquid-phase sintering and hot pressing. |
Industrial Relevance | Enables production of complex, high-performance materials efficiently. |
Discover how solid-state sintering can enhance your material performance—contact our experts today!