The atmosphere used in annealing plays a critical role in determining the final properties and surface quality of the metal. Annealing involves heating metal to a specific temperature to allow its crystalline structure to become fluid, enabling defects to repair themselves, followed by controlled cooling. The choice of atmosphere—such as air, vacuum, endothermic gas, nitrogen-based blends, or reducing gases like hydrogen and argon—depends on the desired outcomes, including surface finish, oxidation prevention, and decarburization control. For instance, air annealing is suitable when surface finish is not critical, while vacuum or reducing atmospheres are preferred for bright finishes and oxidation prevention.
Key Points Explained:
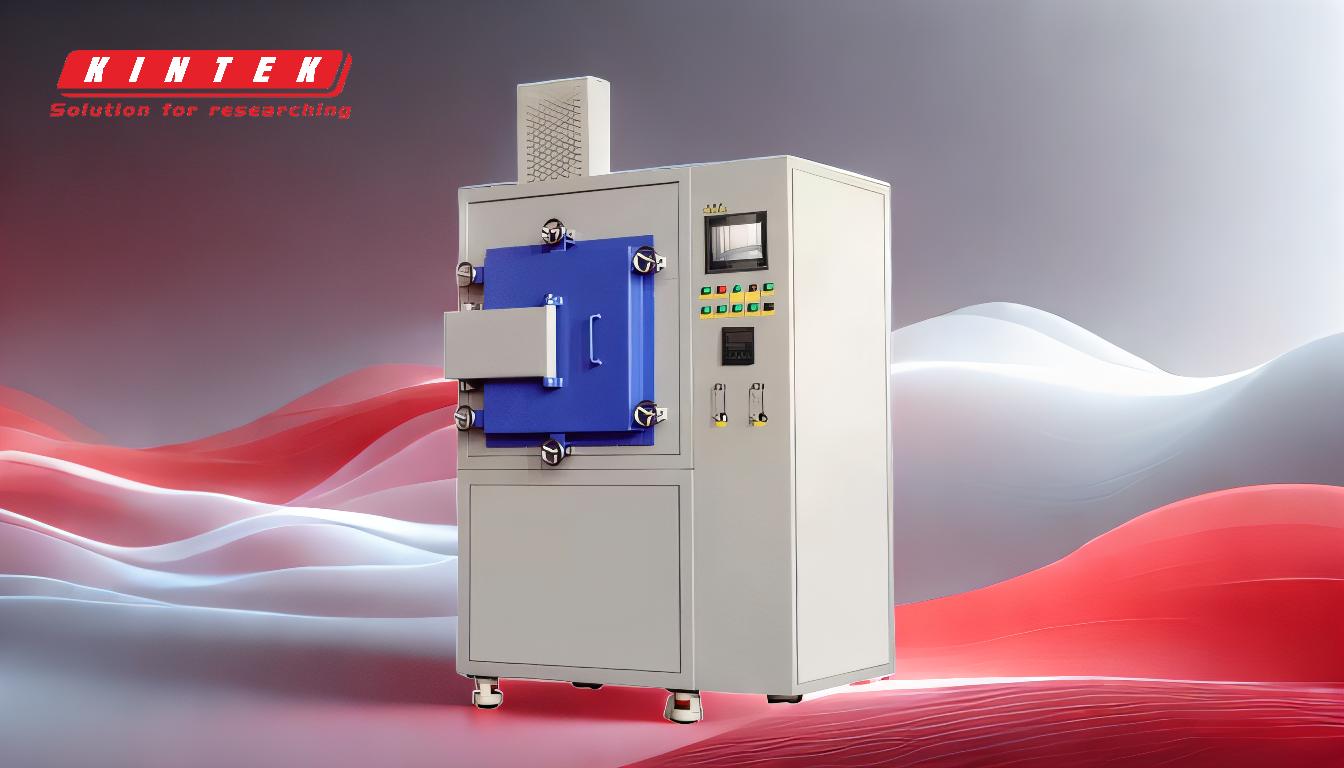
-
Purpose of Annealing Atmosphere:
- The atmosphere during annealing is crucial for controlling oxidation, surface finish, and decarburization.
- Different atmospheres are chosen based on the metal's properties and the desired outcome of the annealing process.
-
Common Annealing Atmospheres:
- Air: Used when surface finish is not a priority. Oxidation and scale formation may occur, but this is acceptable for certain applications.
- Endothermic Gas: A mixture of carbon monoxide, hydrogen, and nitrogen. Prevents oxidation and scale formation, making it ideal for applications requiring a clean surface.
- Vacuum: Provides a bright surface finish by eliminating oxidation. Suitable for high-precision applications.
- Reducing Atmosphere: Includes gases like hydrogen and argon. Prevents oxidation and ensures a bright finish.
- Nitrogen-Based Atmospheres: Blended with hydrocarbons (e.g., propane, methane) or hydrogen to achieve specific properties and prevent oxidation.
-
Oxidation and Scale Prevention:
- High temperatures during annealing can cause oxidation, leading to scale formation on the metal's surface.
- Atmospheres like endothermic gas, vacuum, or reducing gases are used to avoid oxidation and maintain a clean surface.
-
Decarburization Control:
- Decarburization, the loss of carbon from the metal surface, can weaken the material.
- Neutral or endothermic atmospheres are used to control decarburization during annealing.
-
Surface Finish Requirements:
- Bright surface finishes are achieved using vacuum or reducing atmospheres.
- Air annealing is acceptable when surface finish is not critical.
-
Specialized Atmospheres:
- Hydrogen and Argon: Used for specific applications requiring a reducing environment to prevent oxidation and ensure a bright finish.
- Nitrogen-Methanol: A blended atmosphere that provides controlled properties and prevents oxidation.
-
Application-Specific Considerations:
- The choice of atmosphere depends on the metal type, desired properties, and application requirements.
- For example, nitrogen-hydrocarbon blends are used for specific property enhancements, while hydrogen-argon mixtures are ideal for high-precision applications.
By carefully selecting the annealing atmosphere, manufacturers can achieve the desired mechanical properties, surface quality, and oxidation resistance in the final product.
Summary Table:
Atmosphere Type | Key Features | Applications |
---|---|---|
Air | Oxidation and scale formation | Non-critical surface finish |
Endothermic Gas | Prevents oxidation, clean surface | General applications |
Vacuum | Bright finish, no oxidation | High-precision applications |
Reducing Gases (H2, Ar) | Oxidation prevention, bright finish | Specialized applications |
Nitrogen-Based Blends | Controlled properties, oxidation prevention | Property enhancement |
Discover the right annealing atmosphere for your needs—contact our experts today!