The compression ratio of a pellet mill is a critical factor in determining the quality and density of the pellets produced. It refers to the ratio of the length of the pellet to the diameter of the die hole. A higher compression ratio generally results in denser and more durable pellets, which are essential for efficient storage, transportation, and combustion. Understanding the compression ratio helps in selecting the right pellet mill for specific applications, ensuring optimal performance and product quality.
Key Points Explained:
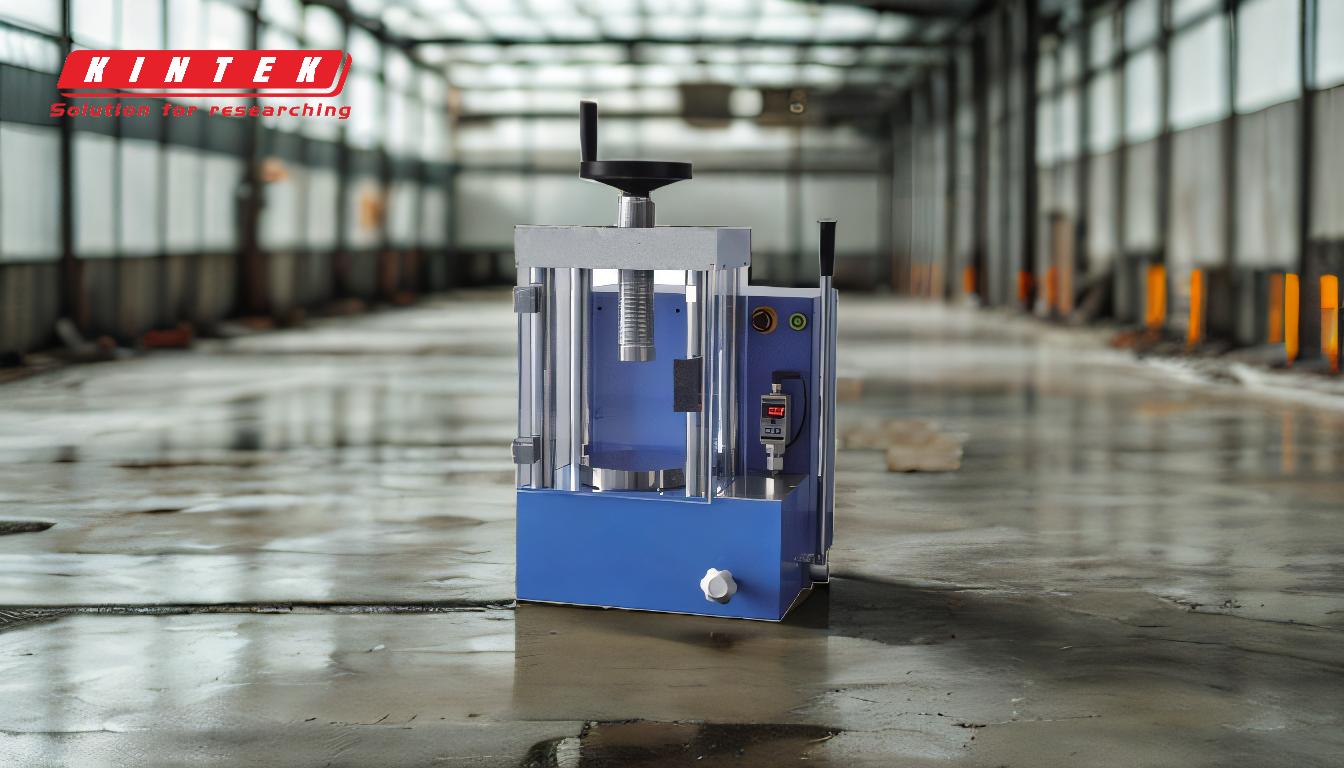
-
Definition of Compression Ratio:
- The compression ratio in a pellet mill is defined as the ratio of the length of the pellet to the diameter of the die hole. It is a measure of how much the material is compressed during the pelletizing process.
- This ratio is crucial because it directly affects the density and durability of the pellets. Higher compression ratios typically produce denser pellets, which are more resistant to breakage and have better combustion properties.
-
Importance of Compression Ratio:
- Pellet Density: A higher compression ratio results in denser pellets, which are more efficient for storage and transportation. Dense pellets also burn more efficiently, providing more energy per unit volume.
- Durability: Pellets with a higher compression ratio are less likely to break during handling and transportation, reducing waste and ensuring that the pellets reach the end-user in good condition.
- Combustion Efficiency: Denser pellets burn more evenly and completely, leading to better combustion efficiency and lower emissions.
-
Factors Influencing Compression Ratio:
- Die Design: The design of the die, including the size and shape of the die holes, plays a significant role in determining the compression ratio. Different die designs are used depending on the type of material being pelletized and the desired pellet characteristics.
- Material Properties: The properties of the material being pelletized, such as moisture content, particle size, and binding properties, also influence the compression ratio. Materials with higher moisture content or larger particle sizes may require different compression ratios to achieve optimal pellet quality.
- Pellet Mill Settings: The settings of the pellet mill, including the speed of the rollers and the pressure applied, can be adjusted to achieve the desired compression ratio. Proper calibration of these settings is essential for consistent pellet quality.
-
Typical Compression Ratios:
- The typical compression ratio for pellet mills varies depending on the application. For example, in the production of animal feed pellets, a compression ratio of 1:5 to 1:8 is common. For wood pellets used in biomass energy production, the compression ratio is typically higher, ranging from 1:8 to 1:12.
- These ratios are chosen based on the specific requirements of the pellets, including density, durability, and combustion efficiency.
-
Adjusting Compression Ratio:
- Die Selection: Selecting the appropriate die with the right hole diameter and length is the primary method of adjusting the compression ratio. Dies with longer holes and smaller diameters will produce pellets with higher compression ratios.
- Material Preparation: Adjusting the moisture content and particle size of the material can also help achieve the desired compression ratio. Properly prepared materials are easier to compress and result in higher-quality pellets.
- Mill Calibration: Fine-tuning the settings of the pellet mill, such as roller pressure and speed, can help achieve the optimal compression ratio for the specific material and application.
In conclusion, the compression ratio of a pellet mill is a vital parameter that influences the quality and performance of the pellets produced. By understanding and optimizing the compression ratio, manufacturers can produce pellets that meet the specific needs of their applications, ensuring efficiency, durability, and optimal combustion.
Summary Table:
Aspect | Details |
---|---|
Definition | Ratio of pellet length to die hole diameter, determining compression level. |
Importance | Higher ratios yield denser, more durable pellets with better combustion. |
Typical Ratios | 1:5 to 1:8 for animal feed; 1:8 to 1:12 for wood pellets. |
Key Factors | Die design, material properties, and mill settings influence the ratio. |
Adjustment Methods | Die selection, material preparation, and mill calibration. |
Optimize your pellet production with the right compression ratio—contact our experts today for tailored solutions!