The CVD (Chemical Vapor Deposition) coating process is a sophisticated method used to deposit hard material layers onto a substrate through a chemical gas-phase reaction. This process involves introducing volatile precursor gases into a reaction chamber, typically under vacuum, and heating the chamber to high temperatures (around 1000 °C) to activate the reaction. The precursor gases decompose or react with the substrate surface, forming a thin, durable coating with excellent adhesion. The process is highly versatile, capable of coating complex geometries, including threads, blind holes, and interior surfaces. However, it requires elevated temperatures and careful control of environmental conditions, which may limit the types of base materials that can be coated. The CVD process is widely used in industries requiring high-performance coatings, such as aerospace, automotive, and tool manufacturing.
Key Points Explained:
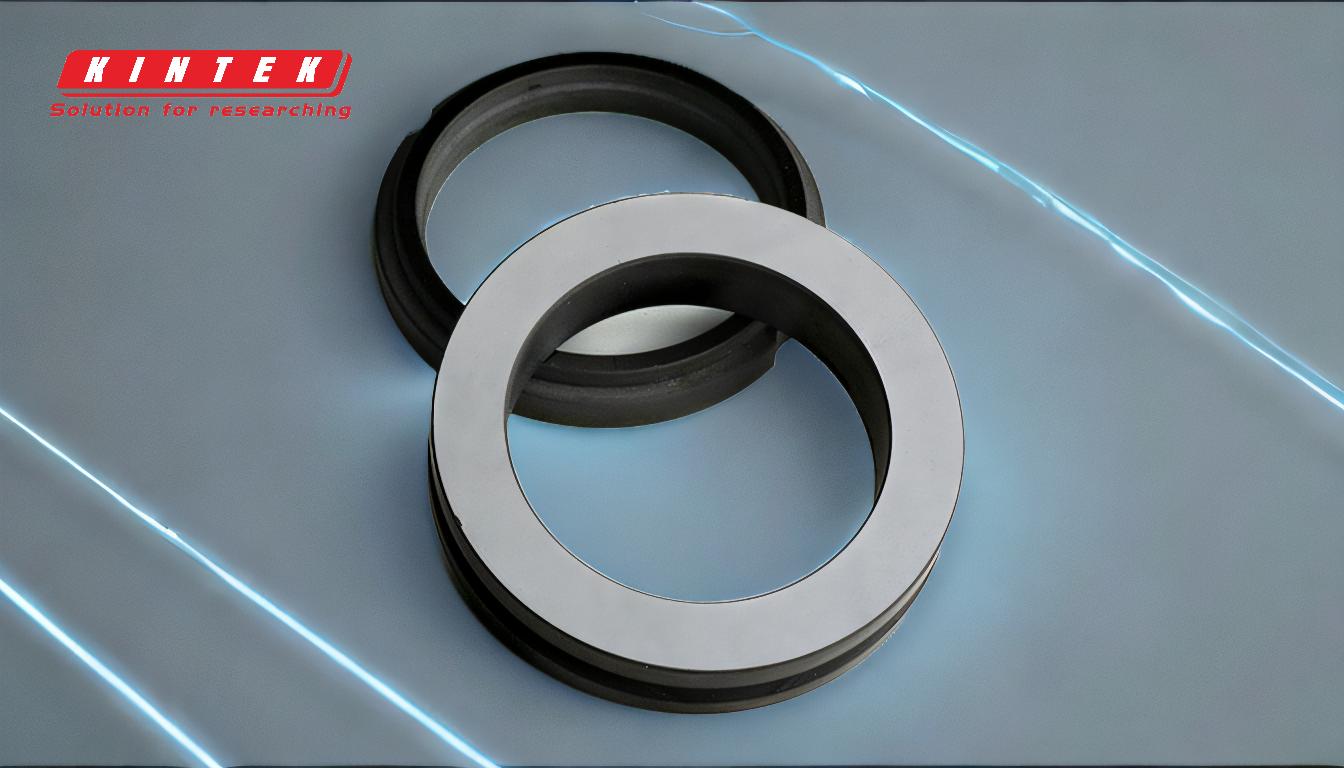
-
Definition and Purpose of CVD Coating
- CVD coating is a chemical gas-phase process used to deposit hard, durable material layers onto a substrate.
- The process is designed to create coatings with high adhesive strength, making it suitable for applications requiring wear resistance, corrosion protection, and thermal stability.
-
Key Components of the CVD Process
- Precursor Gases: Volatile chemicals that react or decompose to form the desired coating.
- Reaction Chamber: A vacuum-sealed environment where the chemical reactions occur.
- Substrate: The material to be coated, which must be clean and free of contaminants.
- Heat Source: Provides the energy needed to activate the chemical reactions, typically at temperatures around 1000 °C.
-
Steps in the CVD Coating Process
The CVD process can be broken down into four main steps:-
Step 1: Introduction of Reactants
- Gaseous precursors and inert gases are introduced into the reaction chamber containing the substrate.
-
Step 2: Activation of Reactants
- The chamber is heated, and pressure is reduced to activate the chemical reactions. Precursors may be activated through thermal energy, plasma, or catalysts.
-
Step 3: Surface Reaction and Deposition
- The activated precursors react with the substrate surface, forming a thin film of the desired material.
-
Step 4: Removal of Byproducts
- Gaseous byproducts are evacuated from the chamber to prevent contamination and environmental pollution.
-
Step 1: Introduction of Reactants
-
Advantages of CVD Coating
- Uniform Coverage: CVD can coat complex geometries, including internal surfaces, threads, and blind holes.
- Superior Adhesion: The coating is chemically bonded to the substrate, ensuring excellent durability.
- Versatility: Suitable for a wide range of materials and applications, including cutting tools, semiconductors, and aerospace components.
-
Limitations of CVD Coating
- High Temperatures: The process requires elevated temperatures, which may limit the types of base materials that can be coated.
- Reactivity Constraints: Some materials may react unfavorably with the precursor gases or the coating process.
- Environmental Concerns: Proper handling and disposal of gaseous byproducts are necessary to avoid pollution.
-
Applications of CVD Coating
- Tool Manufacturing: CVD coatings are widely used to enhance the performance and lifespan of cutting tools, drills, and inserts.
- Aerospace and Automotive: Coatings provide wear resistance, thermal protection, and corrosion resistance for critical components.
- Semiconductors: CVD is used to deposit thin films for electronic and optoelectronic devices.
-
Comparison with PVD (Physical Vapor Deposition)
- Temperature: CVD operates at higher temperatures than PVD, which can limit its applicability to certain materials.
- Coverage: Unlike PVD, CVD can coat all areas of a part, including complex geometries.
- Adhesion: CVD coatings typically exhibit stronger adhesion due to the chemical bonding process.
-
Environmental and Safety Considerations
- The CVD process requires careful handling of precursor gases and byproducts to ensure safety and minimize environmental impact.
- Proper ventilation, waste gas treatment, and adherence to safety protocols are essential.
By understanding the CVD coating process, purchasers of equipment and consumables can make informed decisions about its suitability for their specific applications, considering factors such as material compatibility, performance requirements, and environmental impact.
Summary Table:
Aspect | Details |
---|---|
Process | Chemical gas-phase reaction to deposit hard material layers. |
Key Components | Precursor gases, reaction chamber, substrate, heat source. |
Steps | 1. Introduction of reactants 2. Activation 3. Surface reaction 4. Byproduct removal. |
Advantages | Uniform coverage, superior adhesion, versatility. |
Limitations | High temperatures, reactivity constraints, environmental concerns. |
Applications | Tool manufacturing, aerospace, automotive, semiconductors. |
Comparison with PVD | Higher temperatures, better coverage, stronger adhesion. |
Safety Considerations | Proper handling of gases, ventilation, and waste gas treatment required. |
Discover how CVD coating can enhance your product performance—contact our experts today!