The Chemical Vapor Deposition (CVD) process of silicon involves the deposition of a thin silicon film onto a substrate through chemical reactions in the gas phase. This process is widely used in semiconductor manufacturing and materials science due to its ability to produce high-quality, uniform films. The CVD process typically includes steps such as reactant introduction, activation, surface reaction, and byproduct removal. It is a versatile method that can be adapted for various applications, including the growth of low-dimensional materials like graphene. The process requires precise control of temperature, pressure, and gas flow to achieve optimal results.
Key Points Explained:
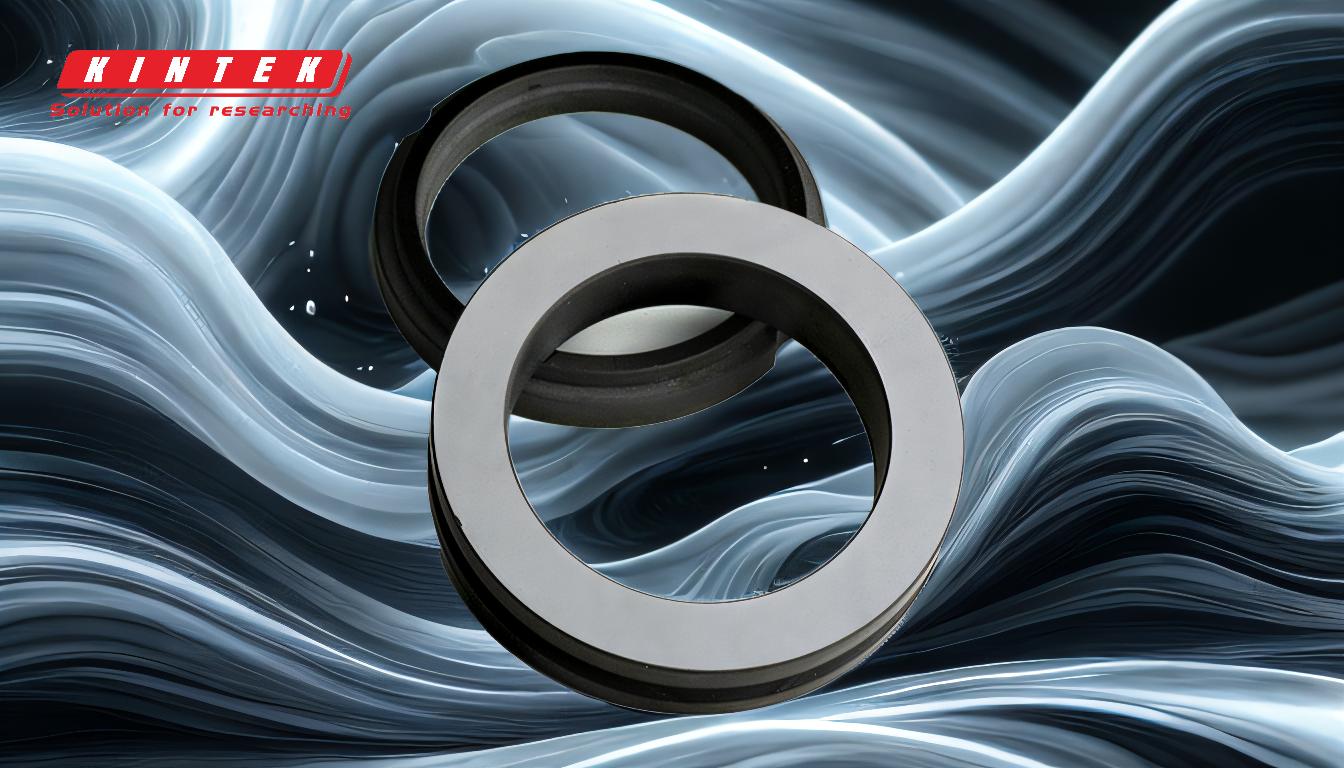
-
Introduction of Reactants:
- Gaseous precursors, often silicon-containing compounds like silane (SiH₄), are introduced into a reaction chamber containing the substrate.
- The substrate is usually heated to a high temperature (around 1000-1100°C) to prepare the surface for deposition.
- Inert gases may be used to carry the reactants and control the reaction environment.
-
Activation of Reactants:
- The reactants are activated through thermal energy, plasma, or catalysts. This step is crucial for breaking down the precursors into reactive species.
- Thermal activation is the most common method, where the high temperature causes the precursors to decompose or react.
-
Surface Reaction and Deposition:
- The activated precursors react at the substrate surface to form a thin silicon film.
- This step involves chemisorption, where the reactive species adhere to the substrate surface, followed by surface diffusion and reaction to form the desired material.
- The quality of the film depends on factors like substrate temperature, precursor concentration, and reaction time.
-
Removal of Byproducts:
- Volatile byproducts, such as hydrogen gas (H₂) or other reaction products, are removed from the reaction chamber.
- Proper removal of byproducts is essential to prevent contamination and ensure the purity of the deposited film.
- The byproducts are often processed to avoid environmental pollution.
-
Control of Process Parameters:
- Temperature: Precise control of the substrate temperature is critical for achieving the desired film properties. High temperatures are typically required for silicon deposition.
- Pressure: The reaction chamber pressure is carefully controlled to optimize the reaction kinetics and film uniformity.
- Gas Flow: The flow rates of the reactant gases and inert carrier gases are adjusted to ensure a consistent supply of precursors and maintain the reaction environment.
-
Applications of CVD for Silicon:
- Semiconductor Manufacturing: CVD is widely used to deposit silicon films in the production of integrated circuits and other semiconductor devices.
- Low-Dimensional Materials: CVD is also used to grow low-dimensional materials like graphene, which have applications in high-performance electronics and sensors.
- Thin-Film Coatings: CVD can produce thin-film coatings with excellent uniformity and adhesion, making it suitable for various industrial applications.
-
Advantages of CVD:
- High-Quality Films: CVD can produce films with low defect counts and good uniformity.
- Versatility: The process can be adapted to deposit a wide range of materials, including silicon, graphene, and other thin films.
- Scalability: CVD is suitable for large-scale production, making it a preferred method in the semiconductor industry.
-
Challenges and Considerations:
- Complexity: The CVD process requires precise control of multiple parameters, making it more complex than other deposition methods.
- Cost: The equipment and materials used in CVD can be expensive, particularly for high-temperature processes.
- Environmental Impact: The handling and disposal of byproducts must be carefully managed to minimize environmental impact.
In summary, the CVD process of silicon is a highly controlled and versatile method for depositing thin films. It involves several key steps, including reactant introduction, activation, surface reaction, and byproduct removal. The process requires precise control of temperature, pressure, and gas flow to achieve high-quality films. CVD is widely used in semiconductor manufacturing and has applications in the growth of low-dimensional materials like graphene. Despite its complexity and cost, CVD remains a leading method for producing high-quality silicon films with excellent uniformity and adhesion.
Summary Table:
Key Steps | Description |
---|---|
Introduction of Reactants | Gaseous precursors like silane (SiH₄) are introduced into a heated reaction chamber. |
Activation of Reactants | Reactants are activated via thermal energy, plasma, or catalysts to form reactive species. |
Surface Reaction | Activated precursors react at the substrate surface to form a thin silicon film. |
Byproduct Removal | Volatile byproducts are removed to ensure film purity and prevent contamination. |
Control of Parameters | Precise control of temperature, pressure, and gas flow is critical for optimal results. |
Applications | Used in semiconductor manufacturing, graphene growth, and thin-film coatings. |
Advantages | High-quality films, versatility, and scalability for large-scale production. |
Challenges | Complexity, high cost, and environmental considerations. |
Discover how the CVD process can enhance your semiconductor production—contact our experts today for tailored solutions!