Deposition process gases are essential in various thin film deposition techniques, such as sputtering and chemical vapor deposition (CVD). These gases facilitate the transfer of material from a source to a substrate, where it forms a solid layer. Inert gases like argon are commonly used for their stability and efficient momentum transfer, while reactive gases such as nitrogen, oxygen, and acetylene are employed to create compounds like oxides, nitrides, and carbides. The choice of gas depends on the target material and the desired film properties, with considerations for atomic weight and chemical reactivity. Process gases are carefully controlled and delivered to ensure precise and high-quality deposition.
Key Points Explained:
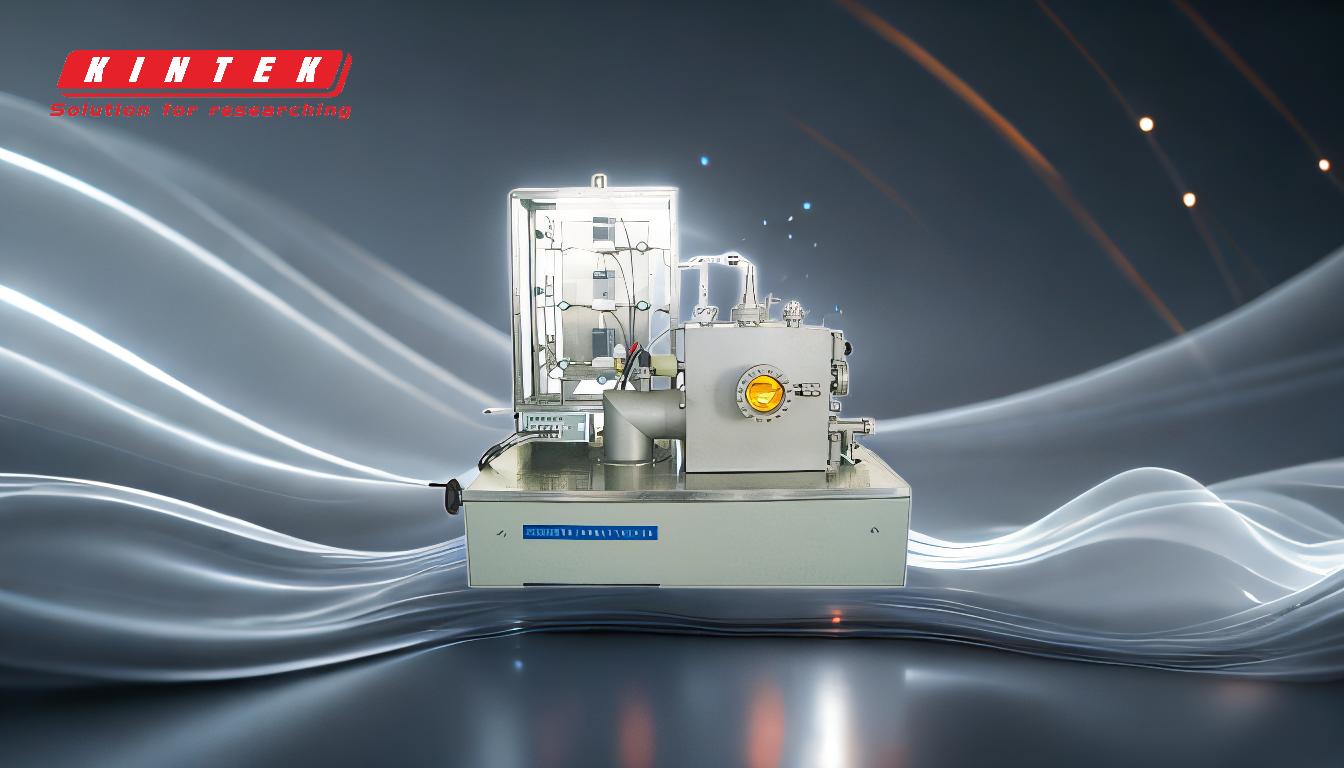
-
Definition of Deposition Process Gases:
- Deposition process gases are used in techniques like sputtering and CVD to transfer material from a source to a substrate, forming a solid layer.
- These gases can be inert (e.g., argon) or reactive (e.g., nitrogen, oxygen), depending on the application.
-
Inert Gases in Deposition:
- Argon: The most commonly used inert gas due to its stability and efficient momentum transfer properties.
- Neon, Krypton, Xenon: Used based on the atomic weight of the target material. Neon is preferred for light elements, while krypton and xenon are used for heavy elements.
- Role: Inert gases like argon are used to sputter target materials by transferring momentum, ensuring the material is ejected and deposited onto the substrate.
-
Reactive Gases in Deposition:
- Nitrogen (N₂): Used to form nitrides, such as titanium nitride (TiN), which are hard and wear-resistant.
- Oxygen (O₂): Used to create oxides, such as aluminum oxide (Al₂O₃), which are often used for their insulating properties.
- Acetylene (C₂H₂) and Methane (CH₄): Used to deposit carbide films, such as silicon carbide (SiC), which are known for their hardness and thermal stability.
- Hydrogen (H₂): Often used in CVD processes to reduce oxides or as a carrier gas.
- Role: Reactive gases chemically interact with the target material or the ejected particles to form compounds on the substrate.
-
Gas Selection Criteria:
- Atomic Weight Matching: The atomic weight of the sputtering gas should be close to that of the target material for efficient momentum transfer. For example, neon is used for light elements, while krypton or xenon are used for heavy elements.
- Chemical Reactivity: Reactive gases are chosen based on the desired chemical composition of the deposited film. For instance, oxygen is used to form oxides, while nitrogen is used to form nitrides.
- Process Requirements: The choice of gas also depends on the specific deposition technique (e.g., sputtering vs. CVD) and the desired film properties (e.g., conductivity, hardness, optical properties).
-
Process Gas Delivery and Control:
- Gas Cylinders: Gases are typically supplied from high-pressure cylinders and regulated before entering the deposition chamber.
- Valves and Meters: Precise control of gas flow is achieved using valves and flow meters, ensuring consistent and reproducible deposition conditions.
- Vacuum Environment: Deposition processes often occur in a vacuum chamber to minimize contamination and control the gas environment.
-
Applications of Deposition Process Gases:
- Sputtering: Inert gases like argon are used to sputter metals and alloys, while reactive gases are used to deposit compounds like oxides, nitrides, and carbides.
- Chemical Vapor Deposition (CVD): Reactive gases such as oxygen, hydrogen, and methane are used to deposit thin films of various materials, including silicon dioxide (SiO₂) and silicon carbide (SiC).
- Low-Pressure CVD (LPCVD): Gases like oxygen, sulfur, and hydrogen are heated and evaporated to deposit thin films on substrates, often used in semiconductor manufacturing.
-
Importance of Gas Purity:
- High-purity gases are critical to avoid contamination and ensure the quality of the deposited film. Impurities can lead to defects, reduced performance, or failure of the final product.
- Gas purity is especially important in semiconductor and optical coating applications, where even trace impurities can significantly impact device performance.
In summary, deposition process gases play a crucial role in thin film deposition techniques, with inert gases like argon providing efficient material transfer and reactive gases enabling the formation of complex compounds. The selection and control of these gases are critical to achieving high-quality, functional films for a wide range of applications.
Summary Table:
Category | Details |
---|---|
Inert Gases | Argon, Neon, Krypton, Xenon - Used for efficient momentum transfer in sputtering. |
Reactive Gases | Nitrogen (N₂), Oxygen (O₂), Acetylene (C₂H₂), Methane (CH₄) - Form oxides, nitrides, carbides. |
Gas Selection Criteria | Atomic weight matching, chemical reactivity, and process requirements. |
Applications | Sputtering, CVD, LPCVD - Used in semiconductor and optical coating industries. |
Importance of Purity | High-purity gases ensure contamination-free, high-performance thin films. |
Optimize your thin film deposition process with the right gases—contact our experts today!