Muffle furnaces and blast furnaces are both heating devices, but they differ significantly in design, application, and operation. A muffle furnace is a laboratory-scale device used for small-scale, batch processes, offering precise temperature control and indirect heating, where materials are isolated from the fuel. It is commonly used for heat treatment, analysis, and testing of materials like low carbon steel, stainless steel, and copper. In contrast, a blast furnace is an industrial-scale furnace used for continuous processes, primarily in metal smelting, where materials are in direct contact with fuel and air. It is designed for large-scale production of metals like iron, operating at extremely high temperatures and requiring complex systems for fuel supply, exhaust, and material feeding.
Key Points Explained:
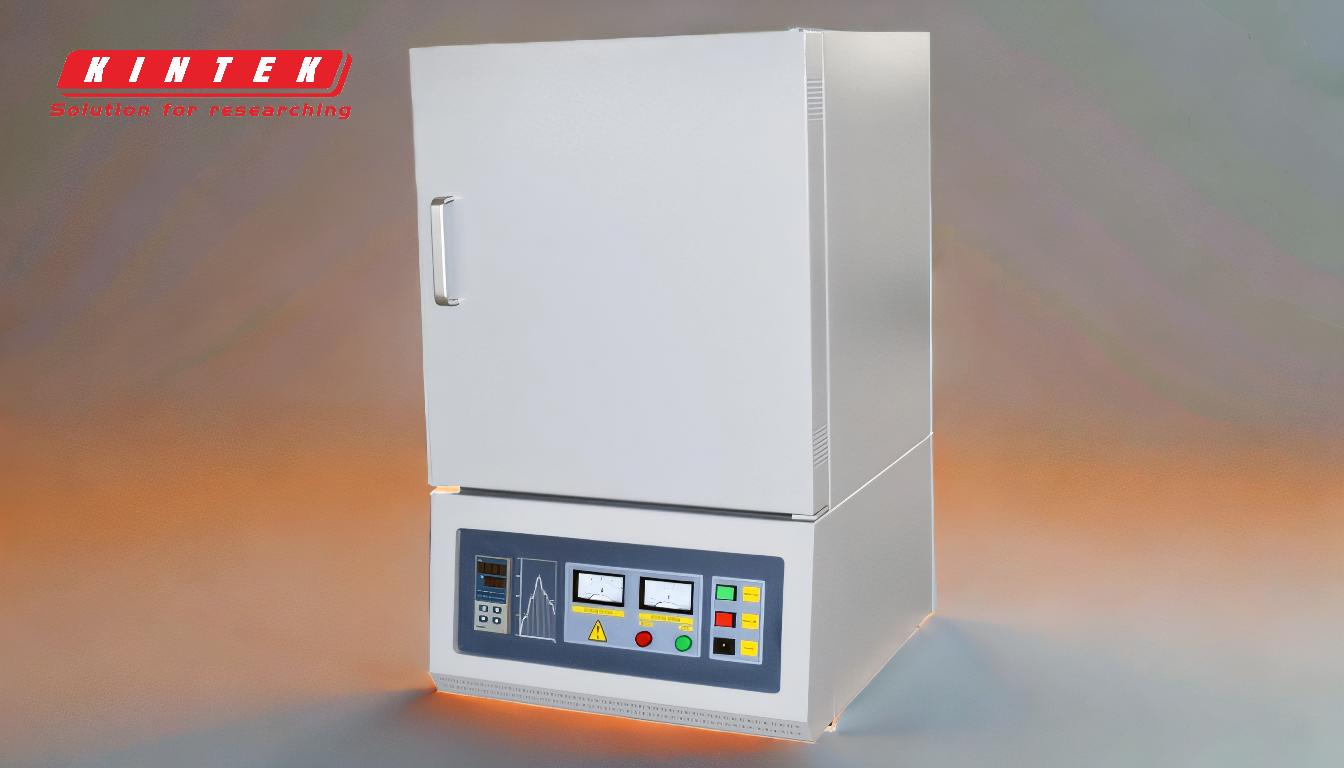
-
Design and Structure:
-
Muffle Furnace:
- Compact and cylindrical in shape, with sliding doors at both ends.
- Features a metal container that can withstand high temperatures.
- Designed for indirect heating, where materials are isolated from the fuel source.
-
Blast Furnace:
- Large, industrial-scale structure with a vertical shaft.
- Includes components like industrial furnace masonry, exhaust systems, preheaters, and combustion devices.
- Designed for direct heating, where materials are in direct contact with fuel and air.
-
Muffle Furnace:
-
Applications:
-
Muffle Furnace:
- Primarily used in laboratories for small-scale, batch processes.
- Suitable for heat treatment, elemental analysis, and testing of materials like steel and copper.
- Operates in a cycle mode, allowing for precise control and repeatability.
-
Blast Furnace:
- Used in industrial settings for continuous metal smelting processes.
- Mainly employed for the production of iron from iron ore.
- Operates at extremely high temperatures, enabling the reduction of metal ores to their metallic form.
-
Muffle Furnace:
-
Heating Mechanism:
-
Muffle Furnace:
- Uses radiant heat generated by an exothermic reaction.
- Materials are heated indirectly, ensuring no contamination from fuel or combustion byproducts.
-
Blast Furnace:
- Relies on direct combustion of fuel (e.g., coke) with air to generate heat.
- Materials are heated directly, allowing for efficient reduction of metal ores.
-
Muffle Furnace:
-
Scale and Operation:
-
Muffle Furnace:
- Small-scale and designed for batch processing.
- Operates manually or automatically, with features like programmable temperature control and data acquisition.
-
Blast Furnace:
- Large-scale and designed for continuous operation.
- Requires complex systems for fuel supply, exhaust, and material feeding, often automated for efficiency.
-
Muffle Furnace:
-
Temperature Control and Consistency:
-
Muffle Furnace:
- Offers precise temperature control and good temperature consistency.
- Ideal for processes requiring accurate and repeatable heating conditions.
-
Blast Furnace:
- Operates at extremely high temperatures, with less focus on precise control.
- Designed for high-throughput processes where consistency is maintained through large-scale operations.
-
Muffle Furnace:
-
Material Handling:
-
Muffle Furnace:
- Typically handles small quantities of materials, often in crucibles or trays.
- Suitable for laboratory-scale experiments and testing.
-
Blast Furnace:
- Handles large volumes of raw materials like iron ore, coke, and limestone.
- Designed for continuous feeding and removal of materials, enabling high production rates.
-
Muffle Furnace:
By understanding these key differences, purchasers of equipment can make informed decisions based on their specific needs, whether for laboratory research or industrial production.
Summary Table:
Feature | Muffle Furnace | Blast Furnace |
---|---|---|
Design | Compact, cylindrical, indirect heating | Large, vertical shaft, direct heating |
Applications | Labs: heat treatment, analysis, testing | Industrial: metal smelting, iron production |
Heating Mechanism | Radiant heat, indirect heating | Direct combustion, fuel + air heating |
Scale | Small-scale, batch processing | Large-scale, continuous operation |
Temperature Control | Precise control, good consistency | High temperatures, less precise control |
Material Handling | Small quantities, crucibles/trays | Large volumes, continuous feeding/removal |
Need help choosing the right furnace for your needs? Contact our experts today!