Annealing and heat treating are both processes used to alter the physical and mechanical properties of metals, but they serve different purposes and involve distinct methods. Annealing is a specific type of heat treatment where the metal is heated to a specific temperature and then slowly cooled to soften it, improve ductility, and reduce internal stresses. Heat treating, on the other hand, is a broader term that encompasses various processes, including annealing, hardening, tempering, and quenching, each designed to achieve specific material properties such as increased hardness, strength, or toughness. While annealing focuses on softening and stress relief, heat treating can be tailored to achieve a wide range of mechanical properties depending on the desired outcome.
Key Points Explained:
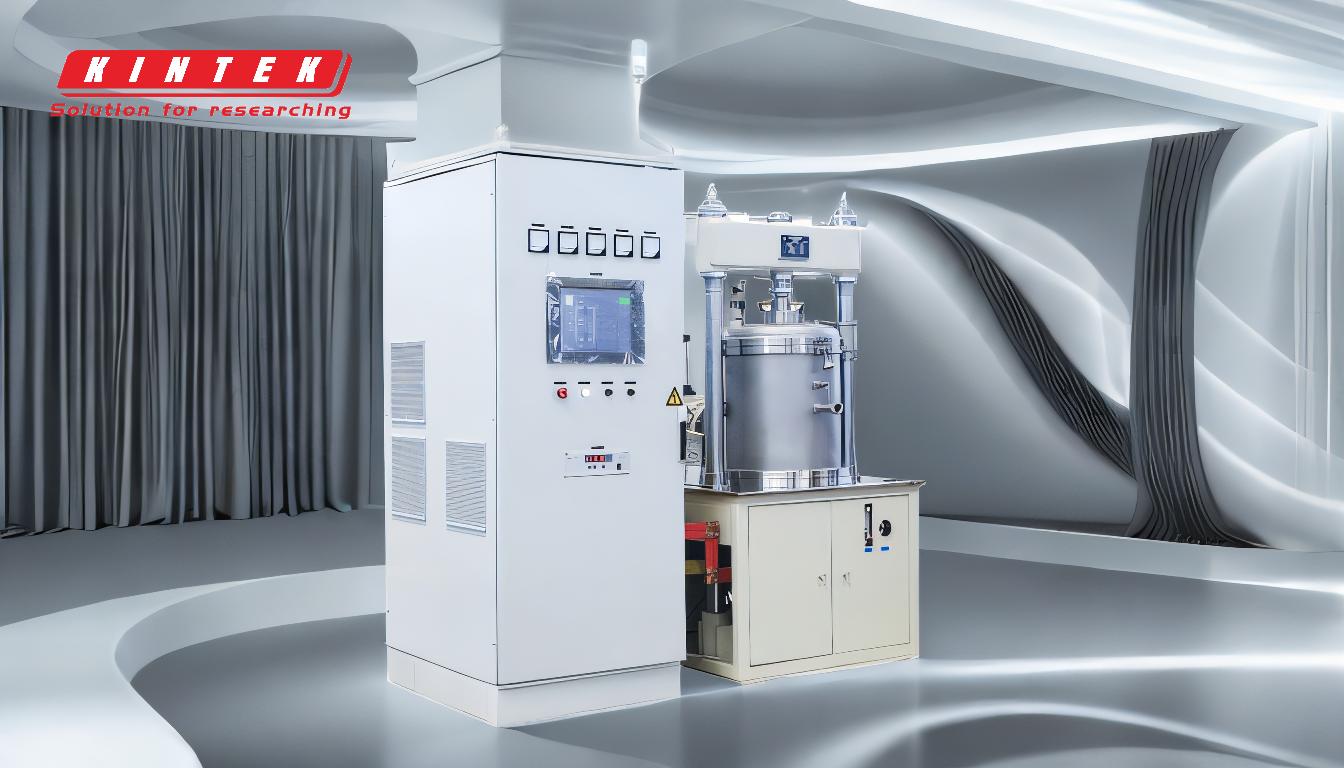
-
Definition and Purpose:
- Annealing: A heat treatment process where metal is heated to a specific temperature (often above or slightly below its transformation range) and then slowly cooled. The primary goals are to soften the metal, improve ductility, and relieve internal stresses. It is often used to prepare the material for further machining or to refine its microstructure.
- Heat Treating: A broader term that includes various processes such as annealing, hardening, tempering, and quenching. Heat treating is used to alter the physical and mechanical properties of metals, including hardness, strength, toughness, and ductility, depending on the specific process used.
-
Temperature and Cooling Rate:
- Annealing: Typically involves heating the metal to a high temperature (e.g., 1,600°F or higher for steel and copper, 600°F or higher for aluminum) and then allowing it to cool slowly. The slow cooling rate is crucial for achieving the desired softness and stress relief.
- Heat Treating: The temperature and cooling rate vary significantly depending on the specific process. For example, hardening involves rapid cooling (quenching) to increase hardness, while tempering involves reheating to a lower temperature to reduce brittleness.
-
Types of Annealing:
- Full Annealing: Involves heating the metal to a temperature above its upper critical temperature and then slowly cooling it in the furnace. This process results in a soft, coarse-grained structure.
- Process Annealing: Used to soften the metal for further cold working. It involves heating to a temperature below the lower critical temperature and then cooling.
- Spheroidizing: A type of annealing that produces a spheroidal or globular form of carbide in steel, improving machinability and ductility.
-
Applications:
- Annealing: Commonly used in industries where softness, ductility, and stress relief are required, such as in the manufacturing of machine parts, tools, and components that undergo further machining or cold working.
- Heat Treating: Used in a wide range of applications, from automotive and aerospace components to tools and machinery, where specific mechanical properties such as hardness, strength, and toughness are needed.
-
Material Suitability:
- Annealing: Suitable for both ferrous (iron-based) and non-ferrous (aluminum, copper, etc.) alloys. It is particularly effective for materials that need to be softened or have their microstructure refined.
- Heat Treating: Applicable to a wide range of materials, including steels, aluminum, copper, and titanium. The specific heat treatment process is chosen based on the material and the desired properties.
-
Outcome:
- Annealing: Results in a softer, more ductile material with reduced internal stresses. It is often a preparatory step for further processing.
- Heat Treating: Can result in a variety of outcomes depending on the process used, including increased hardness, strength, toughness, or a combination of these properties.
In summary, while annealing is a specific type of heat treatment focused on softening and stress relief, heat treating is a broader category that includes various processes aimed at achieving a wide range of mechanical properties. Understanding the differences between these processes is crucial for selecting the appropriate treatment for a given material and application.
Summary Table:
Aspect | Annealing | Heat Treating |
---|---|---|
Purpose | Softens metal, improves ductility, and relieves internal stresses. | Alters hardness, strength, toughness, and ductility depending on the process. |
Temperature | High temperature (e.g., 1,600°F for steel) followed by slow cooling. | Varies by process (e.g., rapid cooling for hardening, reheating for tempering). |
Cooling Rate | Slow cooling to achieve softness and stress relief. | Fast or controlled cooling depending on the desired properties. |
Types | Full annealing, process annealing, spheroidizing. | Includes annealing, hardening, tempering, quenching, and more. |
Applications | Used in machining, cold working, and stress relief. | Used in automotive, aerospace, tools, and machinery for specific properties. |
**Material Suitability | Ferrous and non-ferrous alloys (e.g., steel, aluminum, copper). | Wide range of materials, including steel, aluminum, copper, and titanium. |
Outcome | Softer, more ductile material with reduced internal stresses. | Varies: increased hardness, strength, toughness, or a combination of properties. |
Need help choosing the right metal treatment process? Contact our experts today for personalized guidance!