Calcination and sintering are both thermal processes used in metallurgy and material science, but they serve distinct purposes and operate under different conditions. Calcination involves heating a material, typically metal ore, in the presence of air or oxygen to remove impurities such as carbon, water, or other volatile substances. Sintering, on the other hand, involves heating powdered metal or ceramic materials below their melting points to fuse particles together, creating a solid object with improved mechanical properties. While both processes occur at temperatures below the material's melting point, their objectives and outcomes differ significantly. Calcination is primarily a purification process, whereas sintering is a consolidation process aimed at enhancing material strength and integrity.
Key Points Explained:
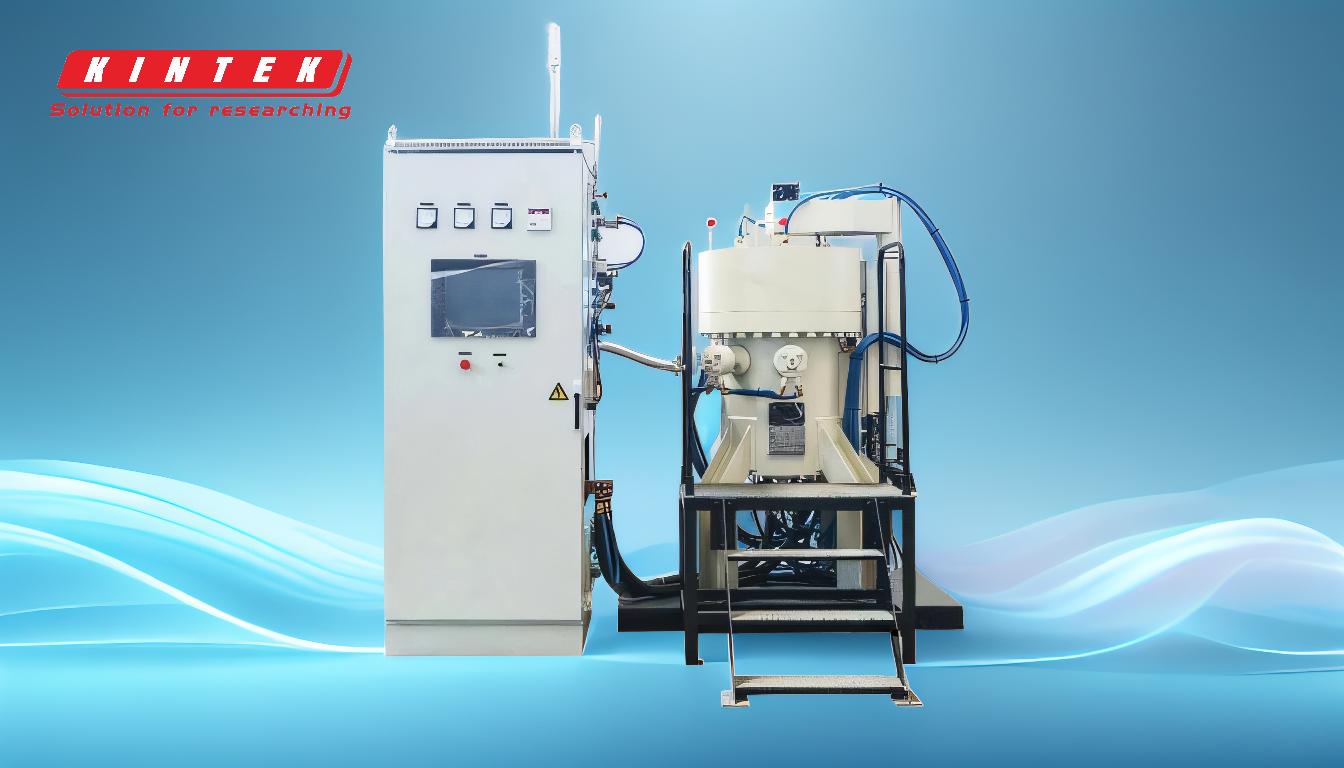
-
Definition and Purpose:
- Calcination: A thermal process where a material (usually metal ore) is heated in the presence of air or oxygen to remove impurities such as carbon, water, or other volatile compounds. The goal is purification.
- Sintering: A thermal process where powdered metal or ceramic materials are heated below their melting points to fuse particles together, forming a solid object. The goal is consolidation and enhancing material properties.
-
Temperature Range:
- Both processes occur at temperatures below the melting point of the material being processed.
- Calcination typically involves lower temperatures compared to sintering, as its primary goal is to drive off impurities rather than fuse particles.
-
Chemical vs. Physical Changes:
- Calcination: Primarily involves chemical changes, such as the decomposition of carbonates or the oxidation of impurities.
- Sintering: Primarily involves physical changes, where particles bond together through diffusion and grain growth without melting.
-
Applications:
- Calcination: Commonly used in the production of cement, lime, and alumina, where impurities need to be removed to achieve the desired chemical composition.
- Sintering: Widely used in powder metallurgy and ceramics to produce components with high strength, density, and dimensional accuracy.
-
Equipment:
- Calcination Furnace: Designed to provide controlled heating in an oxidizing atmosphere, often with features to manage off-gases and impurities.
- Sintering Furnace: Designed to provide uniform heating and controlled cooling, often with features to maintain a specific atmosphere (e.g., inert gas) to prevent oxidation or contamination.
-
Outcome:
- Calcination: Results in a purified material with reduced impurity content, often in a more friable or porous state.
- Sintering: Results in a dense, solid object with improved mechanical properties such as strength, hardness, and wear resistance.
-
Material State:
- Calcination: Typically starts with a bulk material or ore, which may be crushed or ground before heating.
- Sintering: Starts with powdered material, which is compacted into a desired shape before heating.
-
Atmosphere Control:
- Calcination: Often requires an oxidizing atmosphere to facilitate the removal of impurities.
- Sintering: May require a controlled atmosphere (e.g., inert gas or vacuum) to prevent oxidation or contamination during the bonding process.
-
Post-Processing:
- Calcination: The resulting material may require additional processing, such as grinding or further refining, depending on the application.
- Sintering: The sintered product is often near-net-shape and may require minimal post-processing, such as machining or surface finishing.
-
Industry Relevance:
- Calcination: Critical in industries such as cement production, metal refining, and chemical manufacturing.
- Sintering: Essential in industries such as automotive, aerospace, and electronics for producing high-performance components.
Understanding these key differences helps in selecting the appropriate process and equipment for specific material processing needs, ensuring optimal results in terms of purity, strength, and functionality.
Summary Table:
Aspect | Calcination | Sintering |
---|---|---|
Purpose | Purification of materials by removing impurities. | Consolidation of powdered materials to enhance strength and integrity. |
Temperature Range | Lower temperatures, below the material's melting point. | Higher temperatures, still below the material's melting point. |
Changes | Primarily chemical changes (e.g., decomposition, oxidation). | Primarily physical changes (e.g., particle bonding through diffusion). |
Applications | Cement, lime, and alumina production. | Powder metallurgy, ceramics, automotive, aerospace, and electronics. |
Equipment | Calcination furnace with oxidizing atmosphere. | Sintering furnace with controlled atmosphere (e.g., inert gas or vacuum). |
Outcome | Purified material with reduced impurities, often porous. | Dense, solid object with improved mechanical properties. |
Material State | Starts with bulk material or ore. | Starts with powdered material, compacted before heating. |
Atmosphere Control | Oxidizing atmosphere to remove impurities. | Controlled atmosphere to prevent oxidation or contamination. |
Post-Processing | May require grinding or further refining. | Often near-net-shape, minimal post-processing needed. |
Industry Relevance | Cement production, metal refining, chemical manufacturing. | Automotive, aerospace, electronics for high-performance components. |
Need help choosing the right process or equipment for your material processing? Contact our experts today for personalized guidance!