Microwave pyrolysis and conventional pyrolysis differ significantly in their heating mechanisms, efficiency, and outcomes. Microwave pyrolysis uses microwave radiation to directly heat biomass through dielectric properties or absorbers, enabling volumetric heating with a much higher heating rate. This method reduces initiation time, operates at lower temperatures (200-300 °C), and produces bio-oil with higher concentrations of valuable chemicals. Conventional pyrolysis, on the other hand, relies on external heat sources, leading to slower heating rates, higher energy consumption, and less precise temperature control. Microwave pyrolysis also offers better heat distribution and faster response to process changes, making it more efficient and suitable for producing high-value chemicals.
Key Points Explained:
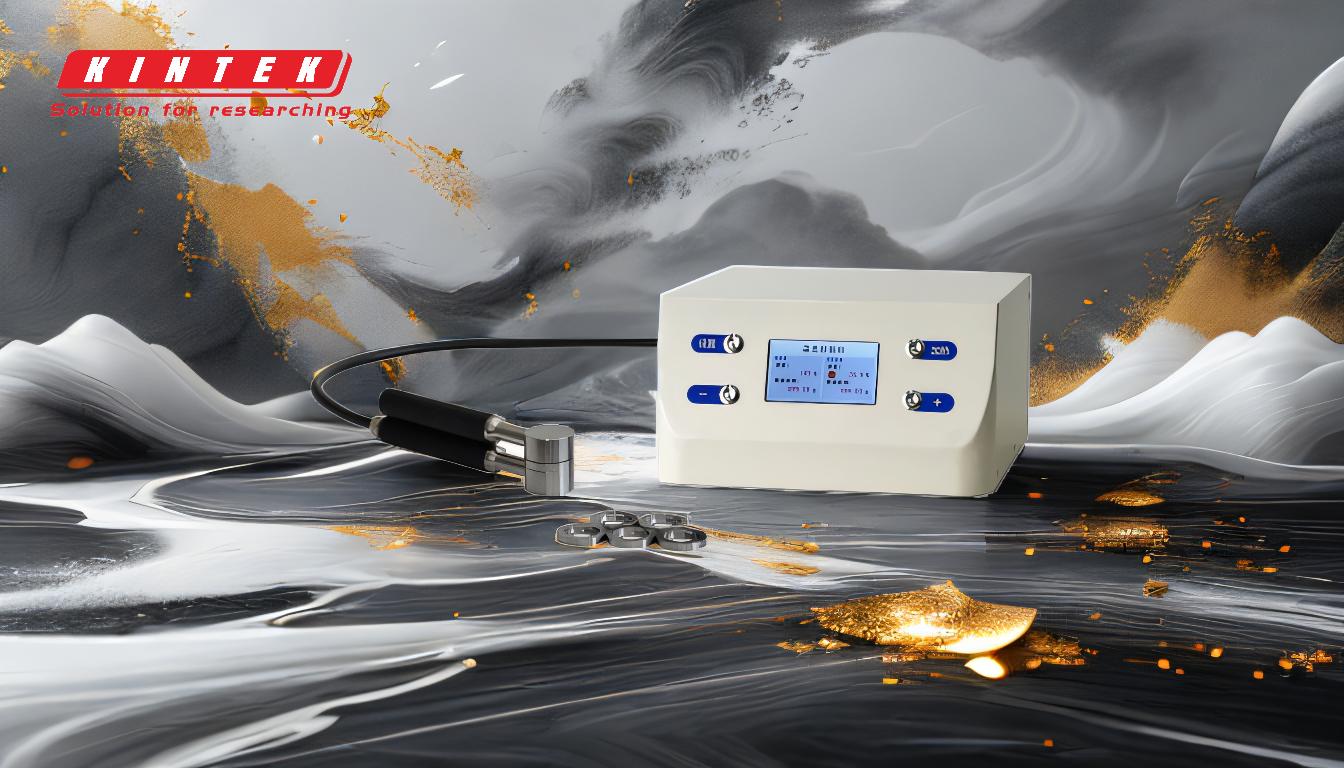
-
Heating Mechanism:
- Microwave Pyrolysis: Utilizes microwave radiation to directly heat biomass through dielectric properties or absorbers, enabling volumetric heating. This means heat is generated within the material itself, leading to uniform and rapid heating.
- Conventional Pyrolysis: Relies on external heat sources (e.g., furnaces) to transfer heat to the biomass. This indirect heating method results in slower and less uniform heating.
-
Heating Rate and Efficiency:
- Microwave Pyrolysis: Offers a much higher heating rate compared to conventional methods. This rapid heating reduces the time required to initiate pyrolysis reactions and lowers overall energy consumption.
- Conventional Pyrolysis: Has a slower heating rate due to the reliance on external heat transfer, leading to longer reaction times and higher energy requirements.
-
Temperature Control:
- Microwave Pyrolysis: Provides precise temperature control with very narrow margins, ensuring even heating throughout the feedstock. This accuracy minimizes the risk of overheating or underheating.
- Conventional Pyrolysis: Struggles with precise temperature control, often resulting in uneven heating and potential hotspots within the material.
-
Operational Temperatures:
- Microwave Pyrolysis: Can operate effectively at lower temperatures (200-300 °C), which is beneficial for preserving thermally labile compounds in the biomass.
- Conventional Pyrolysis: Typically requires higher temperatures to achieve the same level of pyrolysis, which can degrade sensitive compounds.
-
Product Quality:
- Microwave Pyrolysis: Produces bio-oil with higher concentrations of thermally labile, higher-value chemicals. This makes the bio-oil a potential replacement for crude oil in certain chemical processes.
- Conventional Pyrolysis: Often results in bio-oil with lower concentrations of valuable chemicals due to the higher temperatures and longer reaction times involved.
-
Response to Process Changes:
- Microwave Pyrolysis: Can quickly respond to changes in process parameters, allowing for more dynamic and adaptable operation.
- Conventional Pyrolysis: Has a slower response time to process changes, making it less flexible in adjusting to varying conditions.
-
Energy Consumption:
- Microwave Pyrolysis: Generally consumes less energy due to its efficient heating mechanism and shorter reaction times.
- Conventional Pyrolysis: Tends to consume more energy because of the longer heating periods and less efficient heat transfer.
In summary, microwave pyrolysis offers significant advantages over conventional pyrolysis in terms of heating efficiency, temperature control, product quality, and energy consumption. These benefits make microwave pyrolysis a more attractive option for producing high-value chemicals from biomass.
Summary Table:
Aspect | Microwave Pyrolysis | Conventional Pyrolysis |
---|---|---|
Heating Mechanism | Uses microwave radiation for volumetric heating, ensuring uniform and rapid heating. | Relies on external heat sources, leading to slower and less uniform heating. |
Heating Rate | Higher heating rate, reducing initiation time and energy consumption. | Slower heating rate, resulting in longer reaction times and higher energy use. |
Temperature Control | Precise control with narrow margins, minimizing overheating or underheating risks. | Less precise, often causing uneven heating and hotspots. |
Operational Temp. | Effective at lower temperatures (200-300 °C), preserving thermally labile compounds. | Requires higher temperatures, potentially degrading sensitive compounds. |
Product Quality | Produces bio-oil with higher concentrations of valuable chemicals. | Yields bio-oil with lower concentrations of valuable chemicals. |
Response to Changes | Quick response to process changes, enabling dynamic and adaptable operation. | Slower response, making it less flexible for varying conditions. |
Energy Consumption | Consumes less energy due to efficient heating and shorter reaction times. | Consumes more energy due to longer heating periods and less efficient heat transfer. |
Ready to explore the benefits of microwave pyrolysis for your applications? Contact us today to learn more!