DC sputtering and RF sputtering are two distinct thin-film deposition techniques used in various industries, such as semiconductor manufacturing, optics, and coatings. The primary difference lies in the power source and their ability to handle different types of target materials. DC sputtering uses a Direct Current (DC) power source and is ideal for conductive materials, offering high deposition rates and cost-efficiency for large substrates. RF sputtering, on the other hand, uses an Alternating Current (AC) power source at a fixed frequency of 13.56 MHz, making it suitable for both conductive and non-conductive (dielectric) materials. RF sputtering overcomes the limitations of DC sputtering by preventing charge buildup on insulating targets, but it has a lower deposition rate and is more expensive, making it better suited for smaller substrates.
Key Points Explained:
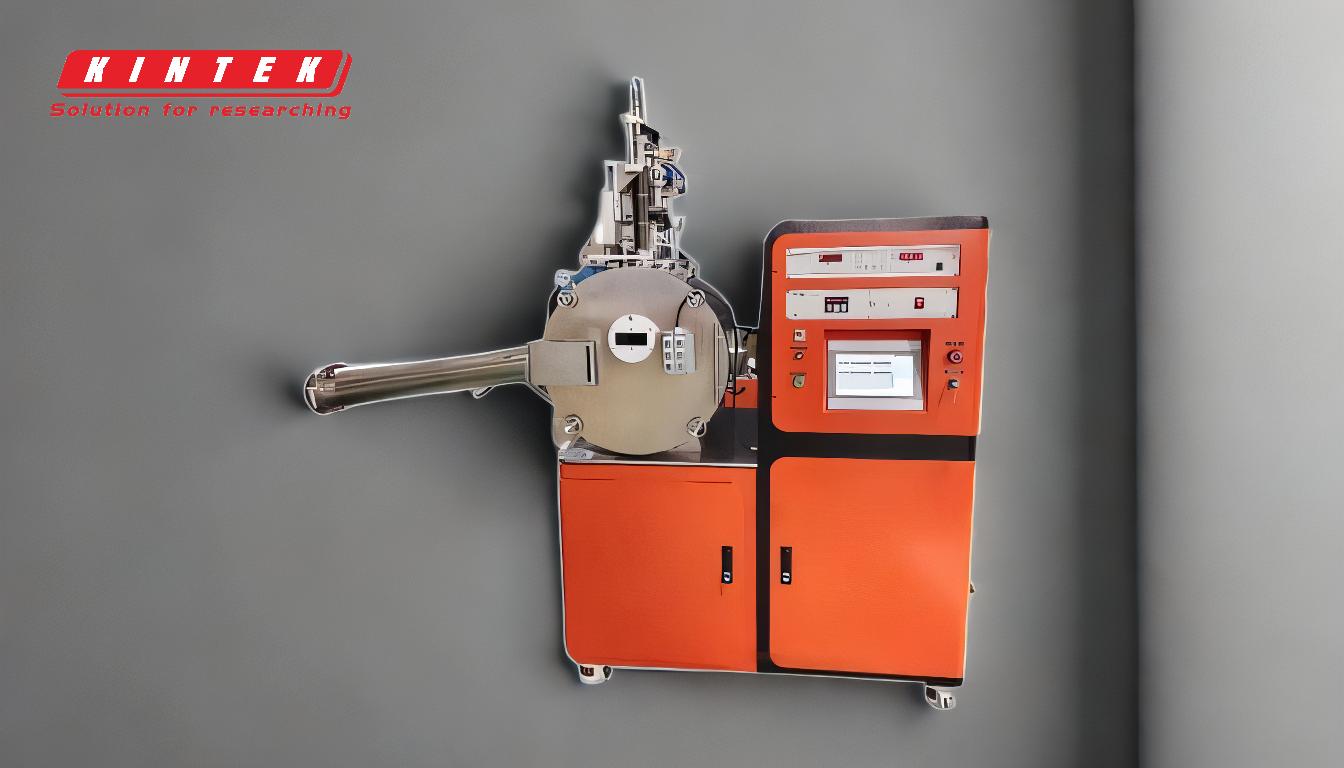
-
Power Source and Mechanism:
- DC Sputtering: Uses a Direct Current (DC) power source. Positively charged gas ions are accelerated toward the target (cathode), which acts as the deposition source. The substrate and vacuum chamber walls often serve as the anode. This method is straightforward and effective for conductive materials.
- RF Sputtering: Uses an Alternating Current (AC) power source, typically at 13.56 MHz. The process involves a cathode (target) and anode connected in series with a blocking capacitor, which is part of an impedance-matching network. This setup facilitates power transfer from the RF source to the plasma discharge, enabling the sputtering of insulating materials.
-
Material Compatibility:
- DC Sputtering: Primarily used for conductive materials like pure metals. It struggles with dielectric (insulating) materials due to charge accumulation on the target surface, which can disrupt the sputtering process.
- RF Sputtering: Capable of handling both conductive and non-conductive materials. The alternating current prevents charge buildup on insulating targets, making it ideal for dielectric materials.
-
Deposition Rate and Efficiency:
- DC Sputtering: Offers high deposition rates, making it cost-effective and efficient for large-scale production. It is widely used in industries where high throughput is essential.
- RF Sputtering: Has a lower deposition rate compared to DC sputtering. The process is more complex and expensive, making it less suitable for large-scale applications but ideal for smaller substrates or specialized coatings.
-
Voltage Requirements:
- DC Sputtering: Operates at high voltages, typically in the range of 2,000-5,000 volts. This high voltage is necessary to create the plasma and accelerate ions toward the target.
- RF Sputtering: Requires even higher voltages, often exceeding 1,012 volts. However, it can maintain gas plasma at lower chamber pressures, reducing collisions and improving the quality of the deposited film.
-
Applications and Suitability:
- DC Sputtering: Best suited for applications involving conductive materials, such as metal coatings in electronics, optics, and decorative finishes. It is economical and effective for processing large quantities of substrates.
- RF Sputtering: Ideal for applications requiring the deposition of insulating materials, such as dielectric films in semiconductors, optical coatings, and specialized thin films. Its ability to handle non-conductive materials makes it indispensable in advanced manufacturing processes.
-
Cost and Complexity:
- DC Sputtering: Generally more cost-effective and simpler to implement. The equipment is less expensive, and the process is easier to control, making it a popular choice for many industrial applications.
- RF Sputtering: More expensive due to the complexity of the RF power supply and impedance-matching network. The process requires precise control and is typically used in applications where the benefits outweigh the higher costs.
In summary, the choice between DC and RF sputtering depends on the specific requirements of the application, including the type of material to be deposited, the desired deposition rate, and the scale of production. DC sputtering is the go-to method for conductive materials and large-scale production, while RF sputtering is essential for handling insulating materials and specialized applications.
Summary Table:
Feature | DC Sputtering | RF Sputtering |
---|---|---|
Power Source | Direct Current (DC) | Alternating Current (AC) at 13.56 MHz |
Material Compatibility | Conductive materials only | Conductive and non-conductive materials |
Deposition Rate | High | Lower |
Voltage Requirements | 2,000-5,000 volts | Exceeds 1,012 volts |
Applications | Large-scale production, conductive coatings | Specialized coatings, dielectric films |
Cost and Complexity | Cost-effective, simpler to implement | More expensive, complex process |
Need help choosing the right sputtering technique for your application? Contact our experts today!