Extrusion coating and extrusion lamination are two distinct processes used in the packaging and manufacturing industries to apply thermoplastic materials to substrates. While both processes involve the extrusion of thermoplastic materials, they differ in their application and the number of substrate layers involved. Extrusion coating applies a single layer of thermoplastic material to a substrate, such as paper, to enhance its properties like moisture resistance or durability. In contrast, extrusion lamination involves bonding two substrate layers together using the extruded thermoplastic as an adhesive, creating a multi-layered composite material with combined properties.
Key Points Explained:
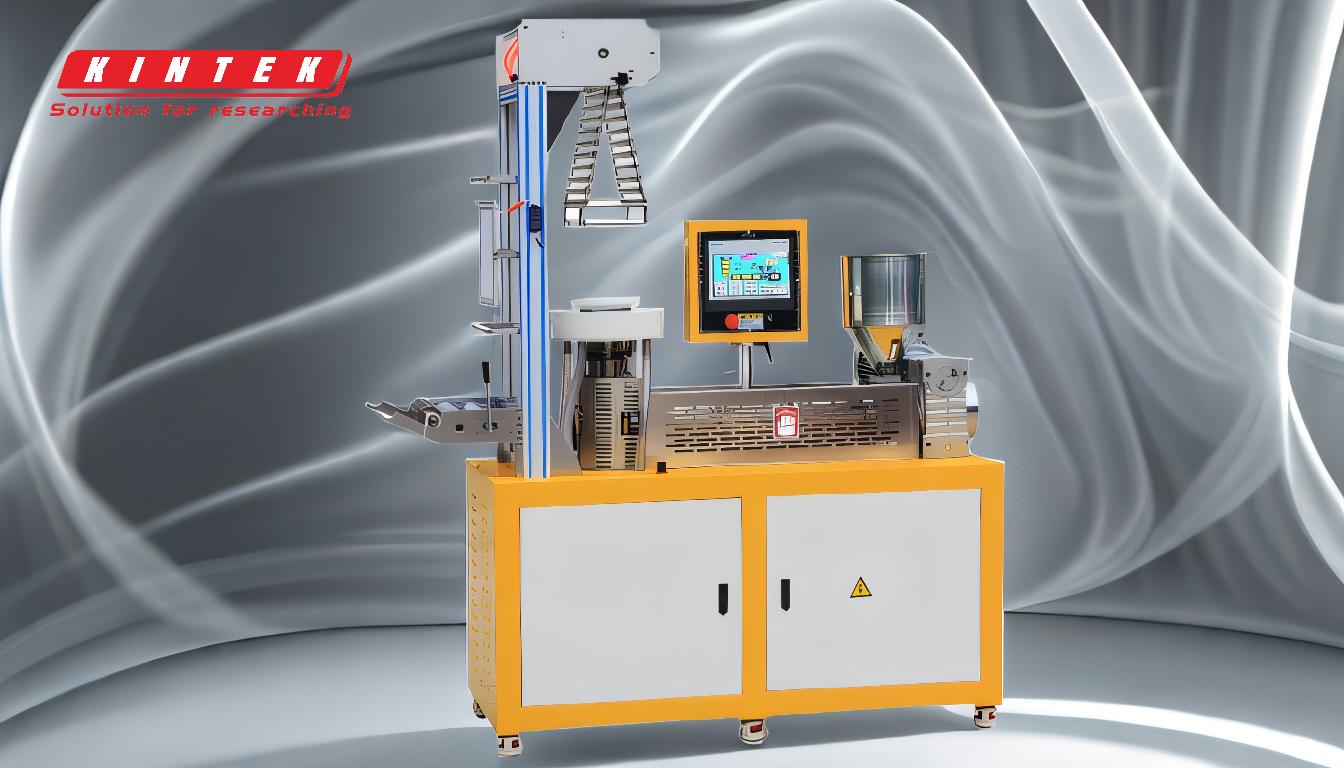
-
Definition and Purpose:
- Extrusion Coating: This process involves applying a layer of thermoplastic material onto a single substrate web, such as paper, film, or foil. The primary purpose is to enhance the substrate's properties, such as improving barrier properties (e.g., moisture resistance), increasing durability, or providing a heat-sealable surface.
- Extrusion Lamination: In this process, two substrate webs are bonded together using an extruded thermoplastic layer as an adhesive. The goal is to combine the properties of both substrates, such as strength, barrier properties, and printability, into a single composite material.
-
Process Mechanics:
- Extrusion Coating: The thermoplastic material is melted and extruded through a flat die, forming a thin film. This film is then pressed onto the substrate using a chill roll, which cools and solidifies the coating. The result is a single substrate with a thermoplastic coating.
- Extrusion Lamination: Here, the thermoplastic material is also extruded through a flat die, but instead of coating a single substrate, it acts as an adhesive between two substrate layers. The thermoplastic layer is sandwiched between the two substrates and then passed through a nip roll to ensure proper bonding.
-
Number of Substrates:
- Extrusion Coating: Involves only one substrate, which is coated with the thermoplastic material.
- Extrusion Lamination: Involves two substrates, which are laminated together using the extruded thermoplastic material as the bonding agent.
-
Applications:
- Extrusion Coating: Commonly used in applications where a single layer of protection or enhancement is needed, such as in food packaging (e.g., coated paperboard for milk cartons), medical packaging, and industrial wraps.
- Extrusion Lamination: Used in applications where the combination of multiple material properties is required, such as in flexible packaging (e.g., snack bags, pouches), where one layer provides strength and another provides barrier properties.
-
Material Considerations:
- Extrusion Coating: The choice of thermoplastic material (e.g., polyethylene, polypropylene) depends on the desired properties of the final product, such as flexibility, heat resistance, or barrier performance.
- Extrusion Lamination: The thermoplastic material must have good adhesive properties to bond the two substrates effectively. Additionally, the materials of the substrates must be compatible with the thermoplastic to ensure strong adhesion.
-
Equipment and Process Control:
- Extrusion Coating: Requires precise control of the extrusion temperature, die gap, and chill roll temperature to ensure uniform coating thickness and adhesion.
- Extrusion Lamination: Requires similar controls but with additional considerations for the alignment and tension of the two substrate webs to ensure proper bonding and avoid defects like delamination.
-
Advantages and Limitations:
- Extrusion Coating: Offers simplicity in application and is cost-effective for single-layer enhancements. However, it may not provide the same level of combined properties as lamination.
- Extrusion Lamination: Provides the ability to combine multiple material properties, offering enhanced performance characteristics. However, it is more complex and may involve higher costs due to the need for precise alignment and bonding.
In summary, while both extrusion coating and extrusion lamination involve the extrusion of thermoplastic materials, they serve different purposes and are used in different applications. Extrusion coating is ideal for enhancing a single substrate, whereas extrusion lamination is used to create multi-layered composites with combined properties. Understanding these differences is crucial for selecting the appropriate process based on the desired outcome and application requirements.
Summary Table:
Aspect | Extrusion Coating | Extrusion Lamination |
---|---|---|
Definition | Applies a single thermoplastic layer to a substrate to enhance properties. | Bonds two substrates using thermoplastic as an adhesive to create a composite. |
Substrates | One substrate (e.g., paper, film, foil). | Two substrates bonded together. |
Purpose | Enhances properties like moisture resistance, durability, or heat-sealability. | Combines properties (e.g., strength, barrier, printability) of multiple substrates. |
Applications | Food packaging (e.g., milk cartons), medical packaging, industrial wraps. | Flexible packaging (e.g., snack bags, pouches). |
Material Considerations | Thermoplastic choice depends on flexibility, heat resistance, or barrier performance. | Thermoplastic must have adhesive properties; substrates must be compatible. |
Advantages | Simple, cost-effective for single-layer enhancements. | Combines multiple material properties for enhanced performance. |
Limitations | Limited to single-layer enhancements. | More complex and costly due to precise alignment and bonding requirements. |
Need help choosing the right process for your application? Contact our experts today!