Forging hammers and forging presses are both essential tools in the metalworking industry, but they operate on fundamentally different principles and are suited for different applications. A forging hammer delivers rapid, high-impact blows to shape metal, relying on kinetic energy to deform the workpiece. In contrast, a forging press applies gradual, continuous pressure to shape the metal, using hydraulic or mechanical force. The choice between the two depends on factors like the type of metal, the desired precision, and the production volume. Understanding their differences helps in selecting the right equipment for specific forging needs.
Key Points Explained:
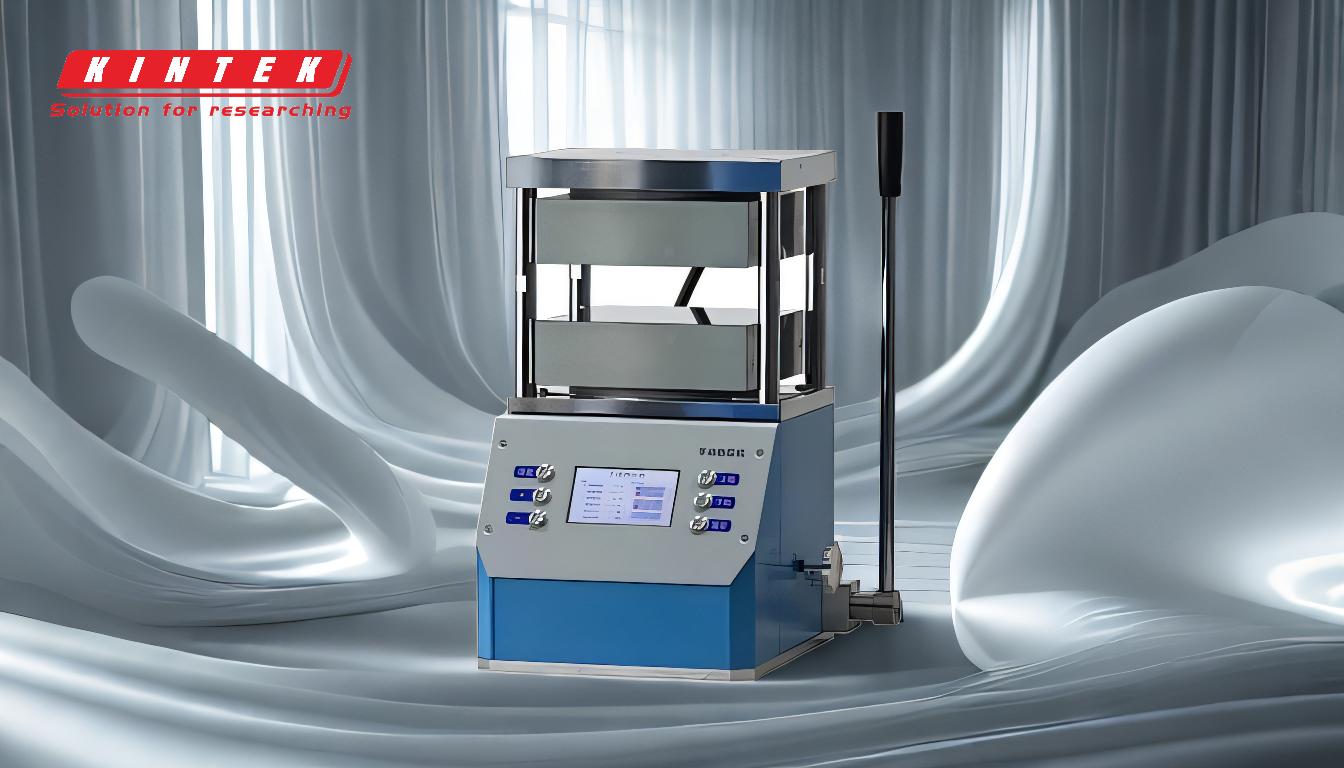
-
Operating Principle:
- Forging Hammer: Operates by delivering high-impact blows to the workpiece. The energy is transferred through the kinetic energy of the hammer, which is either powered by gravity (drop hammers) or compressed air (power hammers). This method is ideal for shaping softer metals or creating intricate designs that require rapid deformation.
- Forging Press: Applies continuous pressure to the workpiece, either through hydraulic or mechanical systems. The force is applied gradually, allowing for more precise control over the deformation process. This method is better suited for harder metals or when high precision is required.
-
Energy Transfer:
- Forging Hammer: The energy transfer is instantaneous and high-impact, which can lead to rapid deformation but may also cause internal stresses in the workpiece. This method is less controlled compared to a press.
- Forging Press: The energy transfer is gradual and controlled, reducing the risk of internal stresses and ensuring a more uniform deformation. This makes it suitable for applications requiring high precision and consistency.
-
Types of Forging Hammers:
- Drop Hammers: Use gravity to deliver the blow. The hammer is raised and then dropped onto the workpiece.
- Power Hammers: Use compressed air or steam to deliver the blows, providing more control and power compared to drop hammers.
-
Types of Forging Presses:
- Hydraulic Presses: Use hydraulic cylinders to generate the force. They are known for their high precision and ability to apply consistent pressure.
- Mechanical Presses: Use mechanical linkages to generate force. They are faster than hydraulic presses but may not offer the same level of precision.
-
Applications:
- Forging Hammer: Ideal for applications requiring rapid deformation, such as shaping softer metals or creating intricate designs. Commonly used in industries like automotive and aerospace for parts that do not require high precision.
- Forging Press: Better suited for applications requiring high precision and consistency, such as forging harder metals or creating parts with tight tolerances. Commonly used in industries like aerospace and defense for critical components.
-
Advantages and Disadvantages:
-
Forging Hammer:
- Advantages: High-speed operation, suitable for softer metals, cost-effective for certain applications.
- Disadvantages: Less control over the deformation process, potential for internal stresses, not suitable for high-precision applications.
-
Forging Press:
- Advantages: High precision, controlled deformation, suitable for harder metals, reduced risk of internal stresses.
- Disadvantages: Slower operation, higher initial cost, may require more maintenance.
-
Forging Hammer:
-
Material Considerations:
- Forging Hammer: Best for materials that can withstand rapid deformation without cracking, such as aluminum or softer steel alloys.
- Forging Press: Suitable for harder materials like titanium or high-strength steel, where controlled deformation is crucial to prevent cracking or other defects.
-
Production Volume:
- Forging Hammer: More suitable for lower to medium production volumes where speed is more critical than precision.
- Forging Press: Better for high-volume production where precision and consistency are paramount.
-
Maintenance and Operational Costs:
- Forging Hammer: Generally lower initial cost but may require more frequent maintenance due to the high-impact nature of the operation.
- Forging Press: Higher initial investment but often lower long-term maintenance costs due to the controlled and gradual application of force.
-
Environmental Impact:
- Forging Hammer: Can be noisier and may produce more vibrations, which can be a concern in certain environments.
- Forging Press: Generally quieter and produces less vibration, making it more suitable for environments where noise and vibration are concerns.
Understanding these key differences will help in making an informed decision when choosing between a forging hammer and a forging press, ensuring that the selected equipment aligns with the specific requirements of the forging process.
Summary Table:
Aspect | Forging Hammer | Forging Press |
---|---|---|
Operating Principle | High-impact blows using kinetic energy (gravity or compressed air). | Gradual, continuous pressure using hydraulic or mechanical force. |
Energy Transfer | Instantaneous, high-impact. Less controlled. | Gradual, controlled. Reduces internal stresses. |
Types | Drop hammers, power hammers. | Hydraulic presses, mechanical presses. |
Applications | Softer metals, intricate designs, lower precision. | Harder metals, high precision, tight tolerances. |
Advantages | High-speed, cost-effective for certain applications. | High precision, controlled deformation, reduced internal stresses. |
Disadvantages | Less control, potential internal stresses, not for high precision. | Slower operation, higher initial cost, may require more maintenance. |
Material Suitability | Best for aluminum, softer steel alloys. | Suitable for titanium, high-strength steel. |
Production Volume | Lower to medium volumes. | High-volume production. |
Maintenance Costs | Lower initial cost, higher maintenance frequency. | Higher initial investment, lower long-term maintenance. |
Environmental Impact | Noisier, more vibrations. | Quieter, less vibration. |
Need help choosing the right forging equipment? Contact our experts today for personalized advice!