Heat treatment processes like hardening and tempering are essential in metallurgy to enhance the mechanical properties of metals. Hardening heat treatment involves heating the metal to a high temperature and then rapidly cooling it, typically through quenching, to increase its hardness and strength. This rapid cooling locks the metal's microstructure in a hardened state, often making it brittle. On the other hand, tempering heat treatment follows hardening and involves reheating the hardened metal to a lower temperature and then cooling it slowly. This process reduces brittleness and improves toughness, making the metal more durable and less prone to cracking under stress.
Key Points Explained:
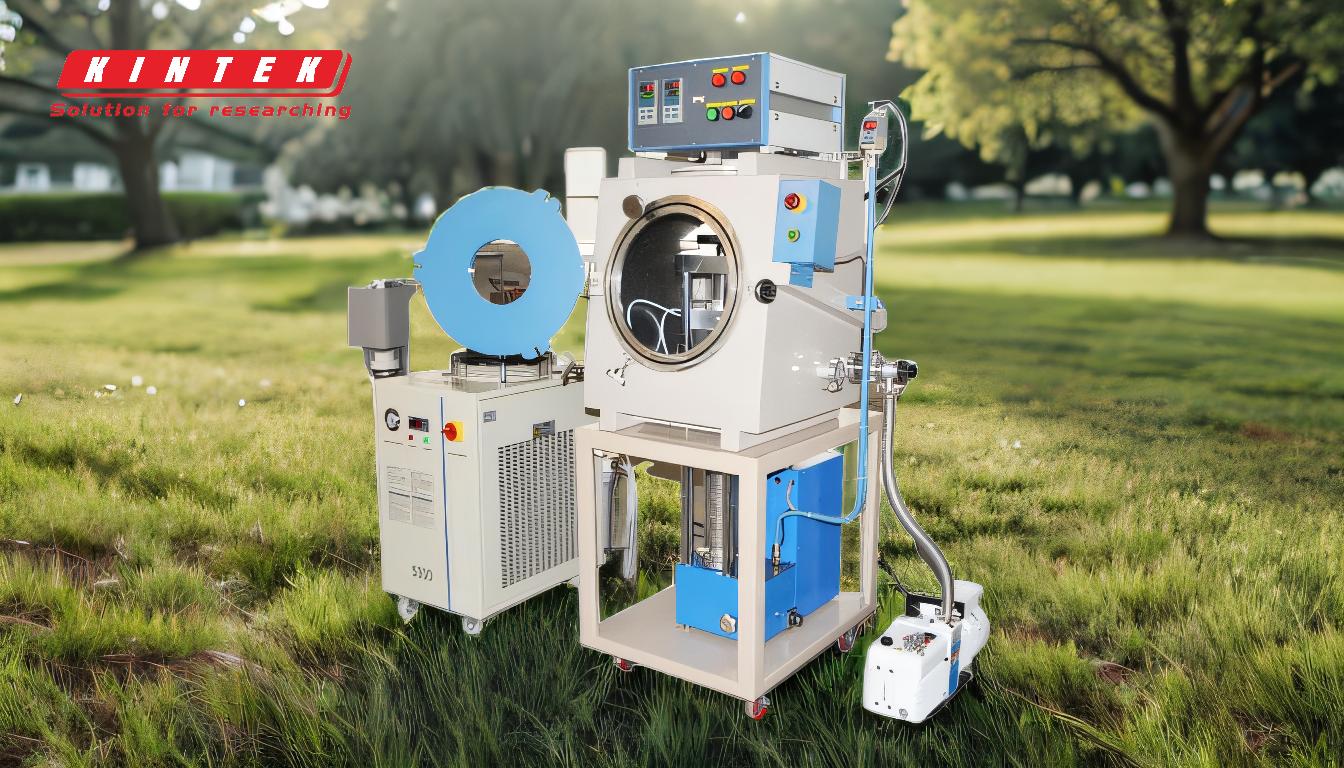
-
Purpose of Hardening Heat Treatment:
- Objective: The primary goal of hardening is to increase the hardness and strength of the metal.
- Process: The metal is heated to a temperature above its critical point (where its microstructure changes) and then rapidly cooled, often by quenching in water, oil, or air.
- Outcome: This rapid cooling transforms the metal's microstructure, typically forming martensite, which is very hard but also brittle.
-
Purpose of Tempering Heat Treatment:
- Objective: Tempering aims to reduce the brittleness caused by hardening and to improve the metal's toughness and ductility.
- Process: After hardening, the metal is reheated to a temperature below its critical point and then cooled slowly. The temperature and duration of tempering can be adjusted to achieve specific mechanical properties.
- Outcome: This process allows some of the martensite to transform into softer and more ductile structures, balancing hardness with toughness.
-
Microstructural Changes:
- Hardening: The rapid cooling during hardening locks the metal's microstructure in a stressed state, forming martensite. This phase is characterized by high hardness but also high internal stresses, leading to brittleness.
- Tempering: During tempering, the reheating allows some of the martensite to decompose into ferrite and cementite, which are more stable and less brittle phases. This reduces internal stresses and improves the metal's overall toughness.
-
Applications:
- Hardening: Commonly used for tools, gears, and other components that require high surface hardness and wear resistance.
- Tempering: Essential for components that need to withstand impact or cyclic loading, such as springs, axles, and structural parts.
-
Temperature and Cooling Rates:
- Hardening: Involves high temperatures (above the critical point) and rapid cooling rates to achieve the desired hardness.
- Tempering: Involves lower temperatures (below the critical point) and slower cooling rates to reduce brittleness and improve toughness.
-
Mechanical Properties:
- Hardening: Increases hardness and strength but decreases ductility and toughness.
- Tempering: Balances hardness with improved toughness and ductility, making the metal more suitable for practical applications.
In summary, hardening and tempering are complementary heat treatment processes that, when used together, optimize the mechanical properties of metals. Hardening increases hardness and strength, while tempering reduces brittleness and enhances toughness, resulting in a material that is both strong and durable.
Summary Table:
Aspect | Hardening Heat Treatment | Tempering Heat Treatment |
---|---|---|
Objective | Increase hardness and strength | Reduce brittleness and improve toughness |
Process | Heat above critical point, then rapidly cool (quenching) | Reheat below critical point, then cool slowly |
Outcome | Forms martensite: high hardness but brittle | Transforms martensite: balances hardness with toughness |
Applications | Tools, gears, components requiring high hardness and wear resistance | Springs, axles, structural parts needing impact resistance |
Temperature | High temperatures (above critical point) | Lower temperatures (below critical point) |
Cooling Rate | Rapid cooling | Slow cooling |
Mechanical Properties | Increases hardness and strength, decreases ductility and toughness | Balances hardness with improved toughness and ductility |
Need expert advice on heat treatment processes? Contact us today to optimize your metal components!