Hot working and forging are both metalworking processes, but they differ in their scope, techniques, and applications. Hot working refers to the deformation of metal at temperatures above its recrystallization point, which allows for easier shaping and improved mechanical properties. Forging, on the other hand, is a specific type of hot working that involves shaping metal using localized compressive forces, often with the use of dies or hammers. While all forging is a form of hot working, not all hot working processes are forging. Understanding these distinctions is crucial for selecting the appropriate method for specific manufacturing needs.
Key Points Explained:
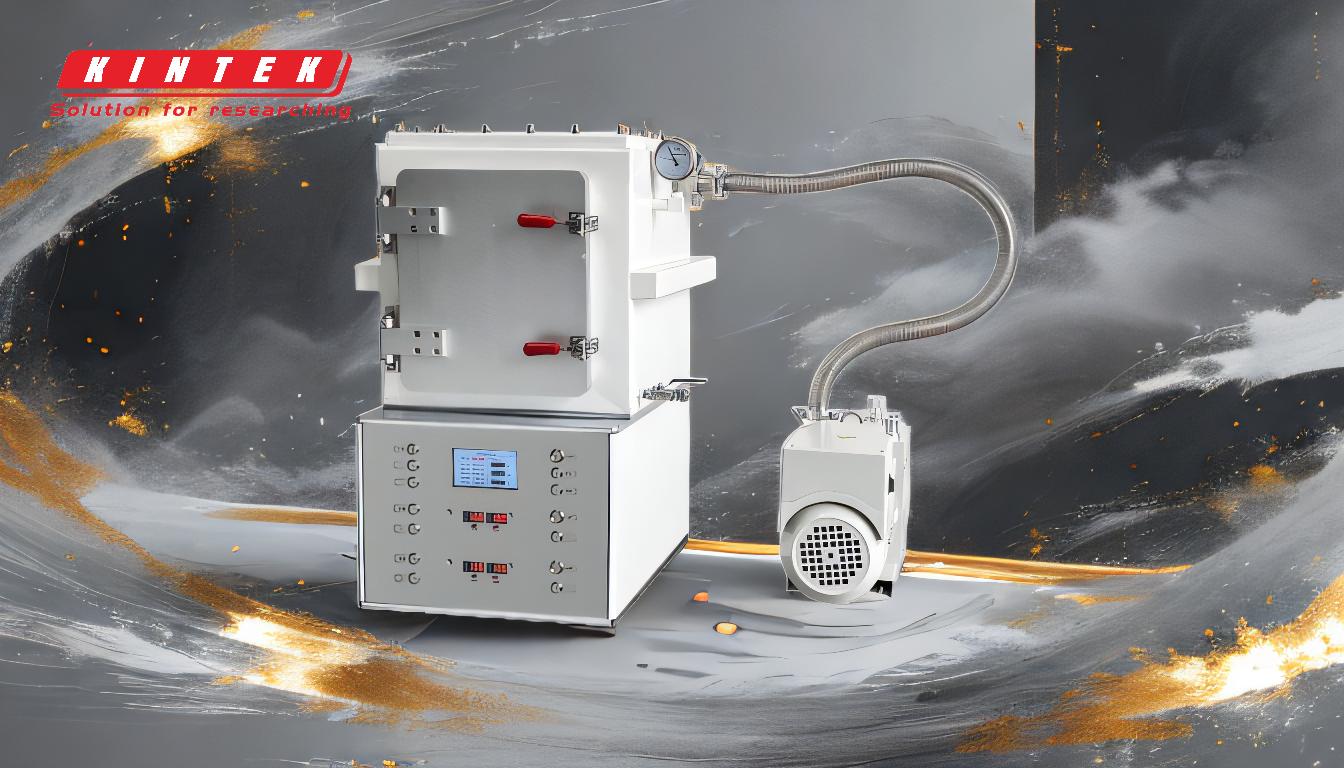
-
Definition and Scope:
- Hot Working: This is a broad term that encompasses any metal deformation process performed above the metal's recrystallization temperature. It includes processes like rolling, extrusion, and drawing, in addition to forging. The primary goal is to shape the metal while maintaining or enhancing its mechanical properties.
- Forging: This is a specific subset of hot working where metal is shaped using compressive forces, typically with tools like hammers or presses. Forging is often used to produce high-strength components with precise shapes.
-
Temperature Considerations:
- Both hot working and forging require the metal to be heated above its recrystallization temperature. This ensures that the metal remains ductile and can be shaped without cracking. However, the exact temperature range can vary depending on the type of metal and the specific process being used.
-
Mechanical Properties:
- Hot Working: The process generally improves the metal's grain structure, leading to enhanced mechanical properties such as toughness and ductility. It also reduces the likelihood of internal stresses and defects.
- Forging: In addition to the benefits of hot working, forging can further refine the grain structure, resulting in even greater strength and fatigue resistance. This makes forged components particularly suitable for high-stress applications.
-
Equipment and Techniques:
- Hot Working: This can involve a variety of equipment, including rolling mills, extrusion presses, and drawing machines. The techniques are diverse and can be tailored to produce a wide range of shapes and sizes.
- Forging: Typically requires specialized equipment such as forging hammers, presses, and dies. The process is more focused and often used for creating complex, high-precision parts.
-
Applications:
- Hot Working: Commonly used in the production of sheets, bars, and structural components. It is versatile and applicable to a wide range of industries, from construction to automotive.
- Forging: Often used in the manufacture of critical components that require high strength and durability, such as gears, crankshafts, and aircraft parts. The process is particularly valued in industries where reliability and performance are paramount.
-
Advantages and Limitations:
- Hot Working: Offers the advantage of improved material properties and the ability to work with a wide range of metals. However, it may require significant energy input and can be less precise than cold working processes.
- Forging: Provides superior strength and precision but is generally more expensive and time-consuming than other hot working methods. It is also limited by the complexity of the shapes that can be produced.
By understanding these key differences, manufacturers can make informed decisions about which process to use based on the specific requirements of their projects.
Summary Table:
Aspect | Hot Working | Forging |
---|---|---|
Definition | Broad term for metal deformation above recrystallization temperature. | Specific type of hot working using compressive forces, often with dies. |
Temperature | Above recrystallization temperature for ductility and shaping. | Same as hot working, but precise temperature varies by metal and process. |
Mechanical Properties | Improves grain structure, toughness, and ductility; reduces internal stresses. | Further refines grain structure for superior strength and fatigue resistance. |
Equipment | Rolling mills, extrusion presses, drawing machines. | Forging hammers, presses, and dies for precise, high-strength components. |
Applications | Sheets, bars, structural components; versatile across industries. | Critical components like gears, crankshafts, and aircraft parts. |
Advantages | Enhanced material properties; works with a wide range of metals. | Superior strength, precision, and durability for high-stress applications. |
Limitations | High energy input; less precise than cold working. | More expensive, time-consuming, and limited by shape complexity. |
Need help deciding between hot working and forging for your project? Contact our experts today for tailored solutions!