Internal and external quenching are two distinct methods used in heat treatment processes, particularly in the context of metalworking and material science. Internal quenching refers to the process where the cooling medium is introduced directly into the core of the material being treated, often through channels or passages within the material itself. This method ensures uniform cooling throughout the material, which can be critical for achieving desired mechanical properties and minimizing distortion. External quenching, on the other hand, involves immersing the material in a cooling medium, such as water, oil, or air, from the outside. This method is more common and easier to implement but may result in less uniform cooling and potential surface stresses. Understanding the differences between these two methods is crucial for selecting the appropriate quenching technique based on the material properties and the desired outcomes.
Key Points Explained:
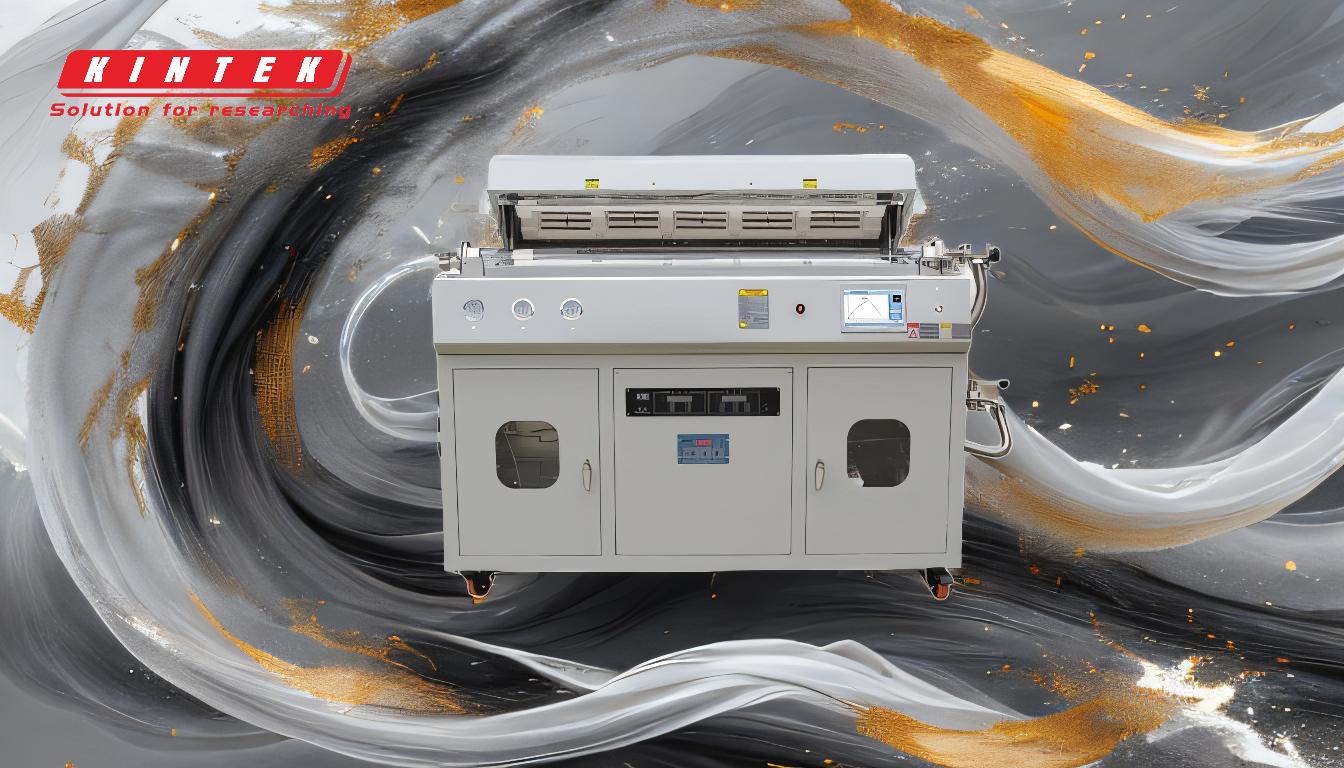
-
Definition and Mechanism:
- Internal Quenching: This method involves introducing the cooling medium directly into the core of the material. This can be achieved through internal channels or passages that allow the coolant to flow through the material, ensuring that the cooling process is uniform from the inside out.
- External Quenching: In this method, the material is immersed in a cooling medium, such as water, oil, or air, from the outside. The cooling process starts at the surface and progresses inward, which can sometimes lead to uneven cooling rates.
-
Uniformity of Cooling:
- Internal Quenching: Provides more uniform cooling throughout the material, which is essential for achieving consistent mechanical properties and minimizing internal stresses and distortion.
- External Quenching: May result in less uniform cooling, particularly in thicker or more complex shapes, leading to potential surface stresses and uneven material properties.
-
Application and Suitability:
- Internal Quenching: Often used in specialized applications where uniform cooling is critical, such as in the heat treatment of large or complex components, or in materials that are prone to distortion.
- External Quenching: More commonly used in general heat treatment processes due to its simplicity and ease of implementation. It is suitable for a wide range of materials and shapes, though it may not be ideal for components requiring extremely uniform properties.
-
Equipment and Implementation:
- Internal Quenching: Requires specialized equipment and setup, such as internal cooling channels or passages within the material, which can increase the complexity and cost of the process.
- External Quenching: Utilizes standard quenching tanks or chambers, making it more accessible and cost-effective for a wide range of applications.
-
Impact on Material Properties:
- Internal Quenching: Can lead to more consistent mechanical properties throughout the material, which is beneficial for applications requiring high precision and reliability.
- External Quenching: May result in variations in material properties, particularly between the surface and the core, which can affect the overall performance of the component.
-
Considerations for Selection:
- The choice between internal and external quenching depends on several factors, including the material type, the geometry of the component, the desired mechanical properties, and the specific application requirements. Internal quenching is typically chosen for high-precision applications where uniform cooling is essential, while external quenching is more suitable for general-purpose heat treatment.
By understanding these key differences, manufacturers and engineers can make informed decisions about the most appropriate quenching method for their specific needs, ensuring optimal material performance and longevity.
Summary Table:
Aspect | Internal Quenching | External Quenching |
---|---|---|
Definition | Cooling medium introduced directly into the core of the material. | Material immersed in a cooling medium from the outside. |
Uniformity of Cooling | Ensures uniform cooling throughout the material. | May result in less uniform cooling, especially in thicker or complex shapes. |
Applications | Used in specialized applications requiring uniform cooling (e.g., large components). | Suitable for general-purpose heat treatment due to simplicity and cost-effectiveness. |
Equipment | Requires specialized equipment with internal cooling channels. | Utilizes standard quenching tanks or chambers. |
Material Properties | Leads to consistent mechanical properties throughout the material. | May cause variations in properties between the surface and core. |
Selection Factors | Ideal for high-precision applications needing uniform cooling. | Best for general applications where extreme uniformity is not critical. |
Need help choosing the right quenching method for your application? Contact our experts today!