VAR (Vacuum Arc Remelting) and ESR (Electroslag Remelting) are two distinct steel refining processes used to produce high-quality alloys with improved mechanical properties, cleanliness, and homogeneity. While both processes aim to enhance material quality, they differ significantly in their methods, principles, and outcomes. VAR involves remelting a consumable electrode under vacuum using an electric arc, which removes dissolved gases and impurities while achieving directional solidification. In contrast, ESR uses a molten slag layer to refine the electrode, focusing on improving inclusion cleanliness and reducing segregation. Below, the key differences between VAR and ESR steel are explained in detail.
Key Points Explained:
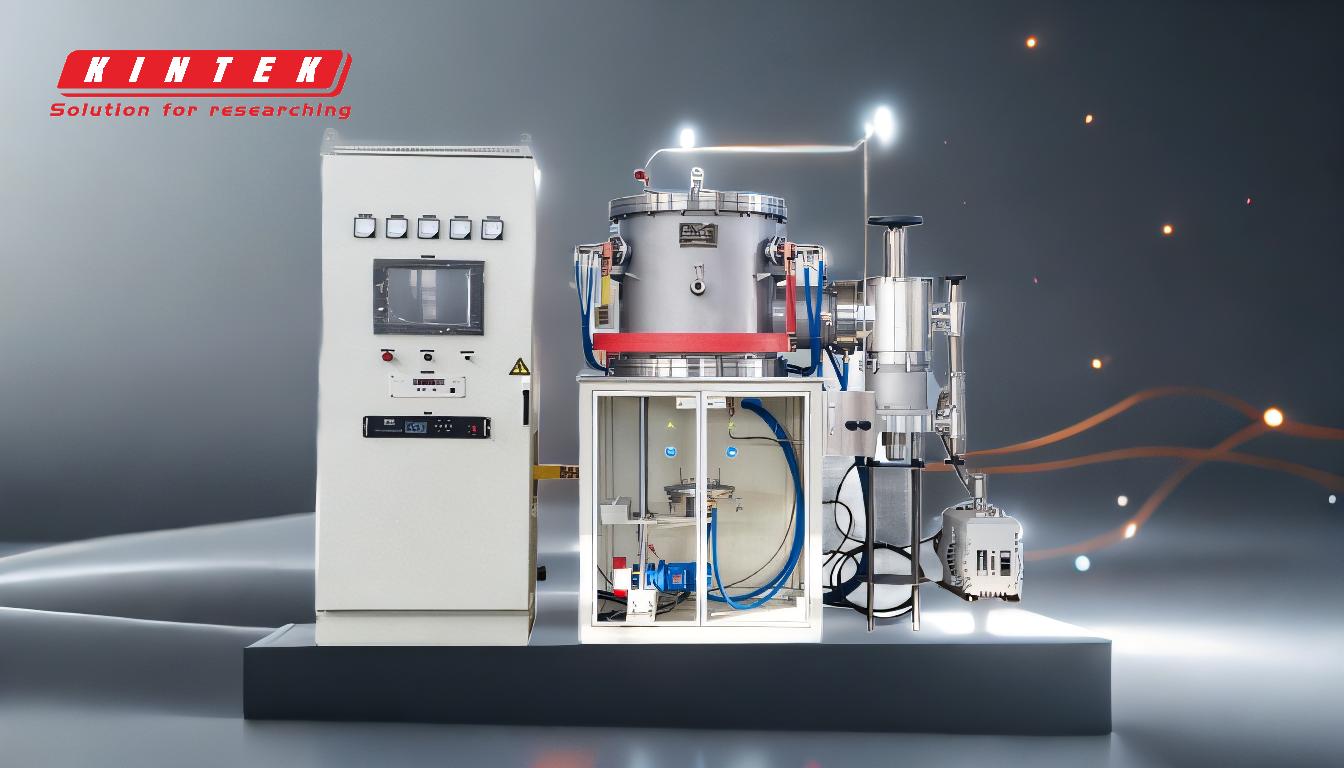
-
Process Mechanism:
-
VAR:
- Uses an electric arc under vacuum to remelt a consumable electrode.
- The electrode is melted by the intense heat of the arc, and droplets fall into a water-cooled mold, forming a new ingot.
- Operates in a high vacuum environment, which helps remove dissolved gases (e.g., hydrogen, nitrogen) and volatile impurities.
-
ESR:
- Uses a molten slag layer to refine the electrode.
- The electrode is melted by electrical resistance heating as it passes through the conductive slag.
- The slag acts as a filter, trapping impurities and non-metallic inclusions, improving the cleanliness of the steel.
-
VAR:
-
Environmental Conditions:
-
VAR:
- Conducted in a vacuum, which prevents oxidation and eliminates atmospheric contamination.
- Ideal for reactive metals like titanium and zirconium, as well as high-performance steels and superalloys.
-
ESR:
- Conducted in an inert gas atmosphere or under a protective slag layer.
- The slag provides a barrier against atmospheric contamination but does not offer the same level of gas removal as a vacuum.
-
VAR:
-
Impurity Removal:
-
VAR:
- Excels at removing dissolved gases (hydrogen, nitrogen, carbon dioxide) and volatile trace elements.
- The vacuum environment allows for the extraction of impurities with high vapor pressure.
-
ESR:
- Focuses on removing non-metallic inclusions and improving oxide cleanliness.
- The slag captures and holds impurities, resulting in a cleaner final product.
-
VAR:
-
Solidification Control:
-
VAR:
- Achieves directional solidification from the bottom to the top of the ingot.
- Reduces macro-segregation and minimizes micro-segregation, leading to a more homogeneous structure.
-
ESR:
- Also promotes directional solidification but relies on the cooling rate and slag interaction.
- The solidification process is influenced by the slag layer, which can affect the final microstructure.
-
VAR:
-
Energy Efficiency:
-
VAR:
- Known for its low energy input compared to other remelting processes.
- The vacuum environment and controlled arc heating contribute to energy efficiency.
-
ESR:
- Requires more energy due to the need to maintain the molten slag layer and the electrical resistance heating process.
-
VAR:
-
Applications:
-
VAR:
- Primarily used for reactive metals (titanium, zirconium) and high-performance alloys (superalloys, tool steels).
- Ideal for applications requiring ultra-clean materials with minimal gas content.
-
ESR:
- Commonly used for high-quality steels, such as tool steels, bearing steels, and stainless steels.
- Suitable for applications where inclusion cleanliness and homogeneity are critical.
-
VAR:
-
Advantages:
-
VAR:
- Removes dissolved gases and volatile impurities.
- Achieves directional solidification for improved mechanical properties.
- Low energy consumption and ceramic-free melting process.
-
ESR:
- Improves inclusion cleanliness and reduces segregation.
- Enhances the homogeneity and mechanical properties of the steel.
- Effective for refining a wide range of steel grades.
-
VAR:
-
Limitations:
-
VAR:
- Limited to materials that benefit from vacuum refining.
- Higher equipment and operational costs due to the vacuum system.
-
ESR:
- Less effective at removing dissolved gases compared to VAR.
- Requires careful control of the slag composition and temperature.
-
VAR:
In summary, VAR and ESR are complementary processes, each with unique strengths. VAR is preferred for reactive metals and applications requiring ultra-clean materials with minimal gas content, while ESR is favored for improving inclusion cleanliness and homogeneity in high-quality steels. The choice between the two depends on the specific material requirements and desired properties.
Summary Table:
Aspect | VAR (Vacuum Arc Remelting) | ESR (Electroslag Remelting) |
---|---|---|
Process Mechanism | Uses an electric arc under vacuum to remelt a consumable electrode. | Uses a molten slag layer to refine the electrode via electrical resistance heating. |
Environmental Conditions | Conducted in a vacuum, ideal for reactive metals like titanium and zirconium. | Conducted in an inert gas atmosphere or under a protective slag layer. |
Impurity Removal | Excels at removing dissolved gases (hydrogen, nitrogen) and volatile trace elements. | Focuses on removing non-metallic inclusions and improving oxide cleanliness. |
Solidification Control | Achieves directional solidification, reducing macro-segregation and improving homogeneity. | Promotes directional solidification but influenced by slag interaction. |
Energy Efficiency | Low energy input due to vacuum environment and controlled arc heating. | Requires more energy to maintain the molten slag layer and electrical resistance heating. |
Applications | Reactive metals (titanium, zirconium) and high-performance alloys (superalloys, tool steels). | High-quality steels (tool steels, bearing steels, stainless steels) requiring cleanliness. |
Advantages | Removes dissolved gases, achieves directional solidification, low energy consumption. | Improves inclusion cleanliness, enhances homogeneity, effective for refining various steels. |
Limitations | Limited to vacuum-refining materials, higher equipment and operational costs. | Less effective at removing dissolved gases, requires careful slag composition control. |
Need help choosing the right steel refining process for your application? Contact our experts today!