Induction melting furnaces are widely used in metallurgy for their efficiency, precision, and versatility. The frequency of an induction melting furnace plays a critical role in determining its performance, heating depth, and application suitability. Higher frequencies result in thinner heating layers and precise control over the heating process, making them ideal for applications requiring fine temperature regulation. Conversely, lower frequencies are better suited for deeper penetration and larger-scale operations. The choice of frequency depends on the specific requirements of the melting process, such as material type, desired heating depth, and production scale.
Key Points Explained:
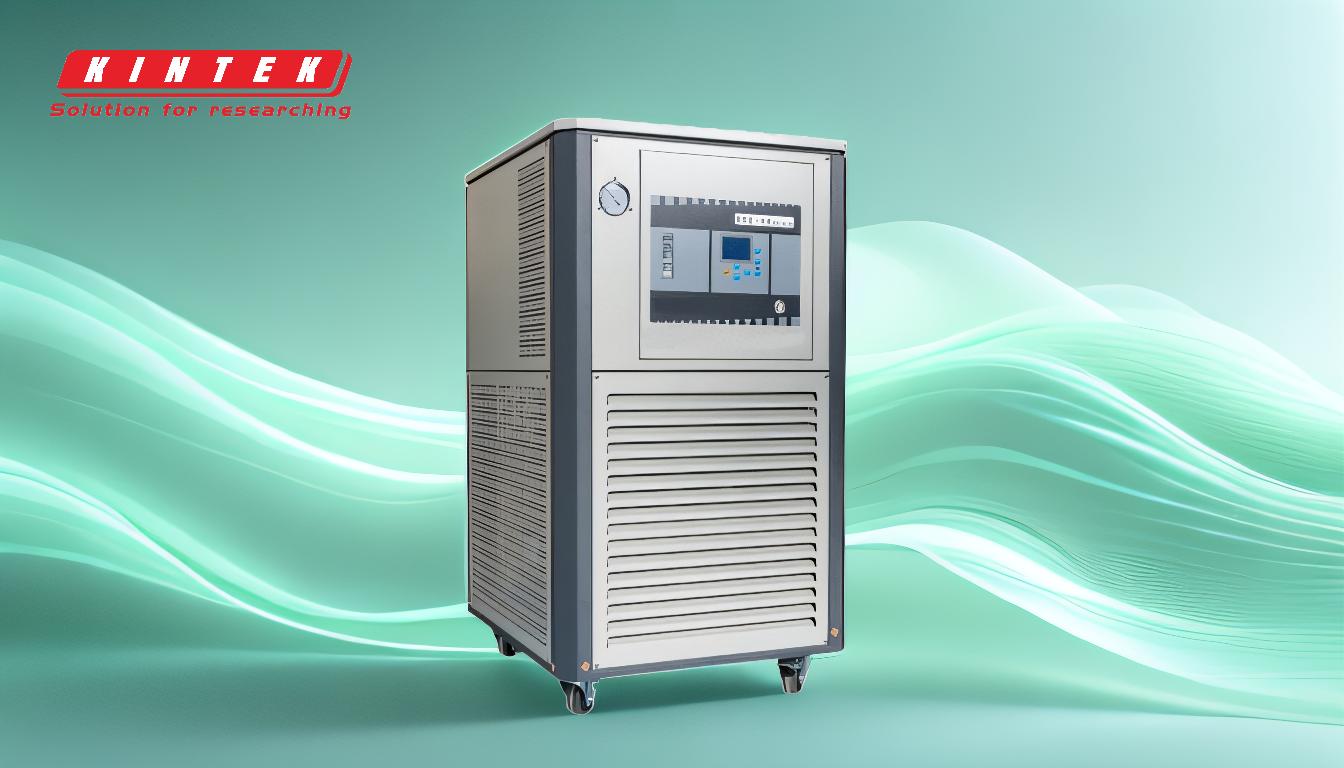
-
Frequency and Heating Depth:
- The frequency of an induction melting furnace directly affects the heating depth of the material. Higher frequencies result in a thinner heating layer, which is ideal for processes requiring precise temperature control, such as surface hardening or small-scale melting. Lower frequencies, on the other hand, provide deeper penetration, making them suitable for larger workpieces or bulk melting applications.
-
Power and Efficiency:
- Higher operating frequencies allow for greater power application in smaller furnaces, enhancing efficiency and reducing energy consumption. This is particularly beneficial for high-precision applications where uniform heating and fast melting are required.
-
Magnetic Stirring Effect:
- The medium frequency magnetic field in induction melting furnaces creates a magnetic stirring effect, which improves the uniformity of the molten metal's composition and aids in scum removal. This feature is crucial for producing high-quality metals with consistent properties.
-
Applications Based on Frequency:
- Induction melting furnaces are used in a variety of applications, including:
- High-frequency furnaces: Ideal for precise heating, such as motor rotor heating, mold diathermy, and small-scale metal melting.
- Medium-frequency furnaces: Suitable for larger-scale operations like forging, steel pipe heating, and bulk metal melting.
- Vacuum induction furnaces: Used for melting precious and reactive metals like titanium alloys, where a vacuum environment prevents chemical reactions and ensures high purity.
- Induction melting furnaces are used in a variety of applications, including:
-
Operational Advantages:
- Induction melting furnaces offer numerous operational benefits, including:
- Fast melting: High frequencies enable rapid temperature rise, reducing smelting time.
- Energy efficiency: Less heat loss and lower environmental impact compared to traditional furnaces.
- Automation: Easy to automate, reducing labor costs and improving consistency.
- Flexibility: Allows for easy changes in furnace bodies to meet different smelting requirements.
- Induction melting furnaces offer numerous operational benefits, including:
-
Technical Features:
- Modern induction melting furnaces are equipped with advanced features such as:
- IGBT frequency conversion: Ensures precise power regulation and comprehensive protection against overcurrent, overheating, and other faults.
- Display functions: Provide real-time monitoring of current, voltage, and time, aiding in process optimization.
- Compact design: Ultra-small volume and lightweight construction make the furnace portable and space-efficient.
- Modern induction melting furnaces are equipped with advanced features such as:
-
Environmental and Economic Benefits:
- Induction melting furnaces are environmentally friendly, producing less pollution and consuming less energy compared to traditional methods. Their cost-effectiveness and ability to produce high-quality metals make them a preferred choice in modern metallurgy.
In conclusion, the frequency of an induction melting furnace is a critical factor that determines its heating depth, efficiency, and suitability for specific applications. By understanding the relationship between frequency and performance, users can select the right furnace for their needs, ensuring optimal results in terms of quality, speed, and cost-effectiveness.
Summary Table:
Aspect | High Frequency | Medium Frequency | Low Frequency |
---|---|---|---|
Heating Depth | Thin layer, precise control | Moderate depth | Deep penetration |
Applications | Small-scale melting, surface hardening | Forging, steel pipe heating | Bulk melting, large workpieces |
Power & Efficiency | High power in small furnaces, energy-saving | Balanced power and efficiency | Suitable for large-scale operations |
Magnetic Stirring | Limited | Improves uniformity, aids scum removal | Limited |
Operational Benefits | Fast melting, automation, flexibility | Cost-effective, consistent results | Ideal for large-scale, high-volume processes |
Ready to choose the right induction melting furnace for your needs? Contact our experts today for personalized guidance!