Heat treatment is a critical process in metallurgy that involves controlled heating and cooling of metals, particularly steel, to alter their physical and mechanical properties. The primary goal is to enhance characteristics such as hardness, strength, ductility, toughness, and wear resistance, making the material suitable for specific applications. Common heat treatment processes for steel include annealing, quenching, tempering, case hardening, and normalizing. Each process involves precise temperature control, holding times, and cooling methods to achieve the desired microstructure and properties. These treatments are essential for optimizing steel's performance in industries like automotive, aerospace, and construction.
Key Points Explained:
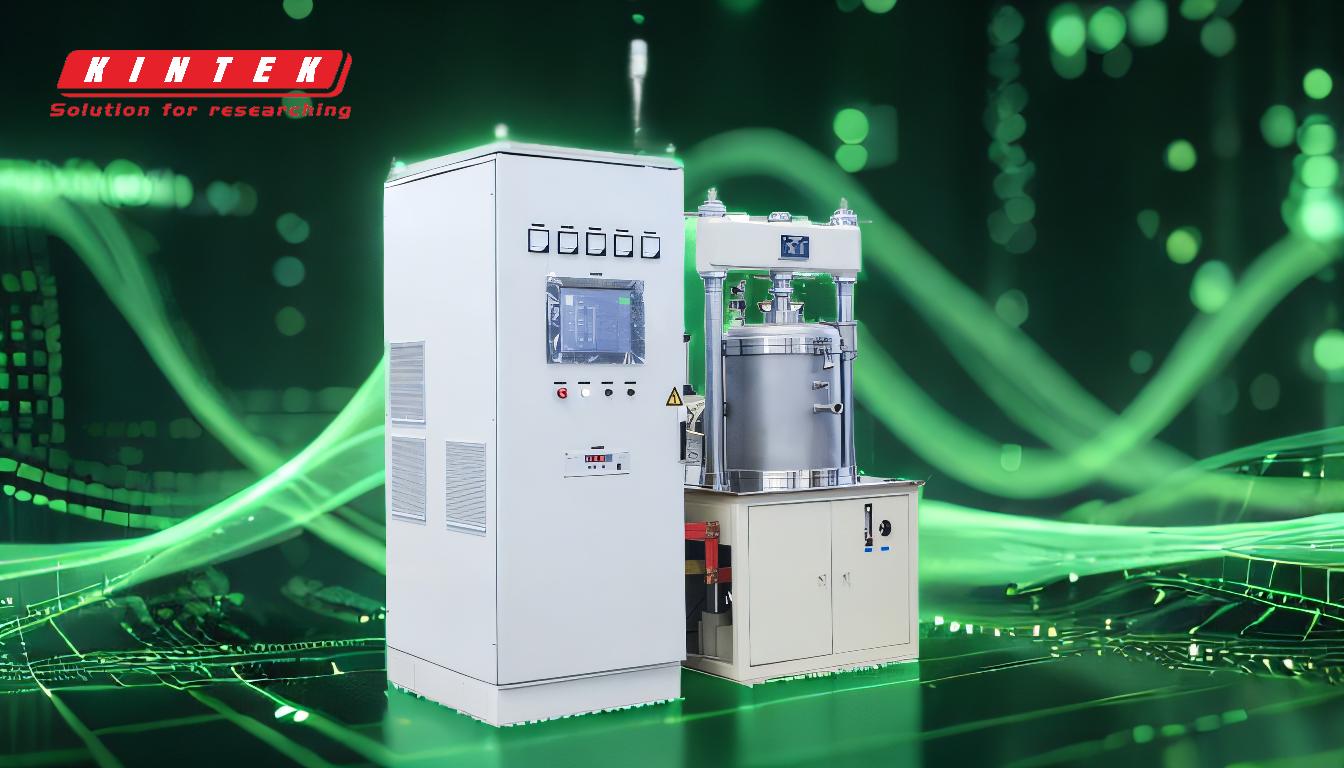
-
Annealing:
- Purpose: Annealing is used to soften steel, improve ductility, and relieve internal stresses. It also refines the grain structure, making the material more workable for subsequent manufacturing processes.
- Process: The steel is heated to a specific temperature (typically between 1,300°F and 1,600°F) and held at that temperature for a predetermined time. It is then slowly cooled, often in the furnace itself, to achieve a uniform microstructure.
- Applications: Commonly used in manufacturing processes like forging, machining, and cold working, where a softer, more ductile material is required.
-
Quenching:
- Purpose: Quenching rapidly cools steel to increase its hardness and strength. This process locks the steel's microstructure in a hardened state, typically forming martensite.
- Process: The steel is heated to a high temperature (above its critical transformation temperature) and then rapidly cooled using water, oil, or air. The cooling rate is critical to achieving the desired hardness.
- Applications: Used in applications requiring high wear resistance and strength, such as gears, shafts, and cutting tools.
-
Tempering:
- Purpose: Tempering reduces the brittleness of quenched steel while maintaining its hardness. It improves toughness and ductility by relieving internal stresses.
- Process: After quenching, the steel is reheated to a temperature below its critical point (typically between 300°F and 1,100°F) and then cooled. The temperature and duration of tempering determine the final properties.
- Applications: Essential for tools, springs, and structural components that require a balance of hardness and toughness.
-
Case Hardening:
- Purpose: Case hardening increases the surface hardness of steel while maintaining a softer, tougher core. This process is ideal for components that require wear resistance on the surface and impact resistance in the core.
- Process: Methods like carburizing, nitriding, and carbonitriding introduce carbon or nitrogen into the steel's surface layer. The material is then quenched to harden the surface.
- Applications: Commonly used for gears, bearings, and camshafts in automotive and industrial machinery.
-
Normalizing:
- Purpose: Normalizing refines the grain structure of steel, improves mechanical properties, and removes internal stresses. It produces a more uniform and predictable microstructure compared to annealing.
- Process: The steel is heated to a temperature above its critical range (typically 1,600°F to 1,800°F) and then air-cooled. This process is faster than annealing.
- Applications: Used for structural components, forgings, and castings that require improved strength and toughness.
-
Stress Relieving:
- Purpose: Stress relieving reduces residual stresses in steel caused by machining, welding, or cold working. It helps prevent distortion or cracking during subsequent processing or service.
- Process: The steel is heated to a temperature below its critical range (typically 1,000°F to 1,200°F) and held for a specific time before slow cooling.
- Applications: Commonly applied to welded structures, machined parts, and components subjected to high-stress environments.
-
Carburizing:
- Purpose: Carburizing increases the carbon content on the steel's surface, enhancing surface hardness and wear resistance while maintaining a tough core.
- Process: The steel is heated in a carbon-rich environment (e.g., gas, liquid, or solid) at high temperatures (1,600°F to 1,800°F) for several hours. Afterward, it is quenched to harden the surface.
- Applications: Used for gears, crankshafts, and other components requiring high surface hardness.
-
Precipitation Hardening:
- Purpose: Precipitation hardening increases the strength and hardness of certain alloys (e.g., stainless steels) by forming fine precipitates within the microstructure.
- Process: The steel is solution-treated (heated to dissolve alloying elements), quenched, and then aged at a lower temperature to allow precipitates to form.
- Applications: Common in aerospace and high-performance engineering applications.
-
Martensitic Transformation:
- Purpose: This transformation occurs during quenching and results in a hard, brittle microstructure called martensite.
- Process: Rapid cooling from high temperatures suppresses the formation of softer phases, locking the steel in a highly stressed, hard state.
- Applications: Essential for high-strength components like cutting tools and bearings.
-
Brazing:
- Purpose: Brazing joins metals using a filler material with a lower melting point than the base metals.
- Process: The assembly is heated to the filler material's melting point in a controlled atmosphere (e.g., hydrogen or nitrogen) to prevent oxidation.
- Applications: Used in the assembly of complex components in industries like electronics and automotive.
By understanding these heat treatment processes, purchasers of equipment and consumables can make informed decisions about the best materials and treatments for their specific applications. Each process offers unique benefits, and selecting the right one depends on the desired properties and performance requirements of the final product.
Summary Table:
Process | Purpose | Applications |
---|---|---|
Annealing | Softens steel, improves ductility, relieves stress, refines grain structure | Forging, machining, cold working |
Quenching | Increases hardness and strength by rapid cooling | Gears, shafts, cutting tools |
Tempering | Reduces brittleness while maintaining hardness | Tools, springs, structural components |
Case Hardening | Increases surface hardness with a tough core | Gears, bearings, camshafts |
Normalizing | Refines grain structure, improves mechanical properties | Structural components, forgings, castings |
Stress Relieving | Reduces residual stresses from machining or welding | Welded structures, machined parts |
Carburizing | Enhances surface hardness and wear resistance | Gears, crankshafts |
Precipitation Hardening | Increases strength and hardness of alloys | Aerospace, high-performance engineering |
Martensitic Transformation | Forms hard, brittle martensite during quenching | Cutting tools, bearings |
Brazing | Joins metals using a filler material | Electronics, automotive assembly |
Ready to optimize your steel's performance? Contact our experts today to find the best heat treatment solution for your needs!