The highest temperature a furnace can reach depends on its type, design, and materials used. For standard preheating furnaces, the maximum temperature is typically around 1,200°C. However, for ultra-high-temperature applications, specialized furnaces, such as those offered by MRF, can operate continuously at temperatures up to 3,000°C (5,430°F). These extreme temperatures require materials like graphite or tungsten for the hot zones, as few materials can withstand such conditions. It is critical to adhere to the furnace's maximum temperature limits to ensure safety, longevity, and optimal performance.
Key Points Explained:
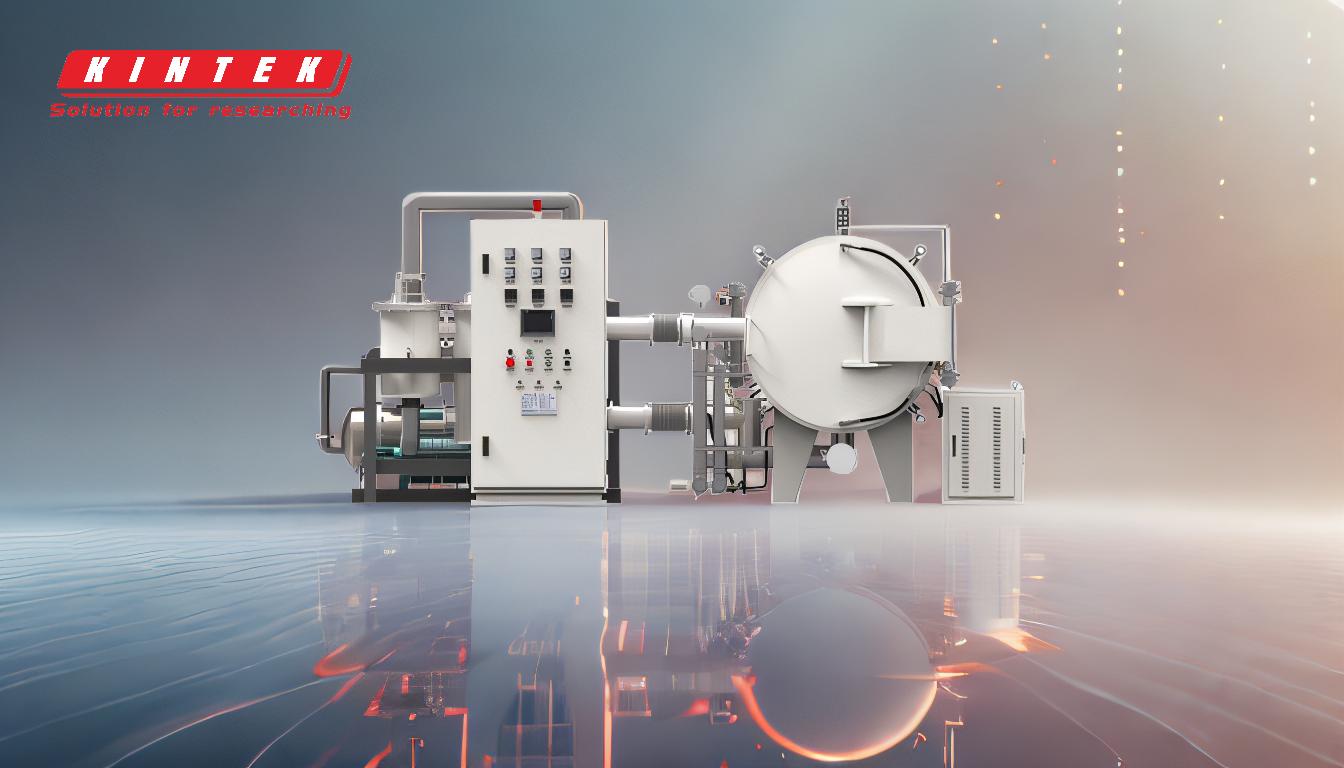
-
Standard Preheating Furnaces:
- These furnaces are commonly used in industrial and laboratory settings.
- They typically reach maximum temperatures of around 1,200°C.
- These temperatures are suitable for many standard applications, such as heat treatment, annealing, and material testing.
-
Ultra-High-Temperature Furnaces:
- For applications requiring extreme heat, specialized furnaces are available.
- These can operate continuously at temperatures as high as 3,000°C (5,430°F).
- Such furnaces are often used in advanced scientific research, aerospace, and materials science.
-
Material Considerations:
- At ultra-high temperatures, the choice of materials for the furnace's hot zone is critical.
- Graphite and tungsten are commonly used due to their ability to withstand extreme heat without degrading.
- These materials ensure the furnace's durability and performance under harsh conditions.
-
Safety and Operational Limits:
- It is essential to not exceed the maximum temperature specified for the furnace.
- Doing so can compromise the furnace's integrity, lead to material failure, and pose safety risks.
- Adhering to operational limits ensures the furnace's longevity and reliability.
-
Applications of High-Temperature Furnaces:
- Furnaces capable of reaching 3,000°C are used in specialized fields such as:
- Material synthesis (e.g., creating advanced ceramics or composites).
- Aerospace testing (e.g., simulating high-temperature environments).
- Scientific research (e.g., studying material properties at extreme temperatures).
- Furnaces capable of reaching 3,000°C are used in specialized fields such as:
-
Energy Efficiency and Performance:
- High-temperature furnaces are designed to provide uniform temperature distribution, stable control, and fast heating.
- Modern designs also focus on energy efficiency, reducing operational costs while maintaining high performance.
In summary, the highest temperature of a furnace varies widely depending on its type and purpose. While standard furnaces typically reach 1,200°C, ultra-high-temperature models can achieve up to 3,000°C, provided they are constructed with suitable materials and operated within their specified limits.
Summary Table:
Furnace Type | Max Temperature | Key Applications | Material Considerations |
---|---|---|---|
Standard Preheating Furnace | ~1,200°C | Heat treatment, annealing, material testing | Standard materials |
Ultra-High-Temperature Furnace | Up to 3,000°C | Material synthesis, aerospace testing, scientific research | Graphite, tungsten for hot zones |
Safety & Operational Limits | Critical | Avoid exceeding max temperature to ensure safety, longevity, and optimal performance | Adherence to specified limits |
Need a furnace for extreme temperatures? Contact our experts today to find the right solution for your needs!