Annealing is a critical heat treatment process primarily aimed at improving the physical, mechanical, and sometimes chemical properties of materials. Its main purpose is to relieve internal stresses, enhance ductility, and reduce hardness, making materials more workable and suitable for further processing. Annealing achieves this by heating the material above its recrystallization temperature, maintaining that temperature for a specific duration, and then cooling it. This process helps in creating a more uniform and homogeneous internal structure, which improves the material's quality, service life, and performance in various applications.
Key Points Explained:
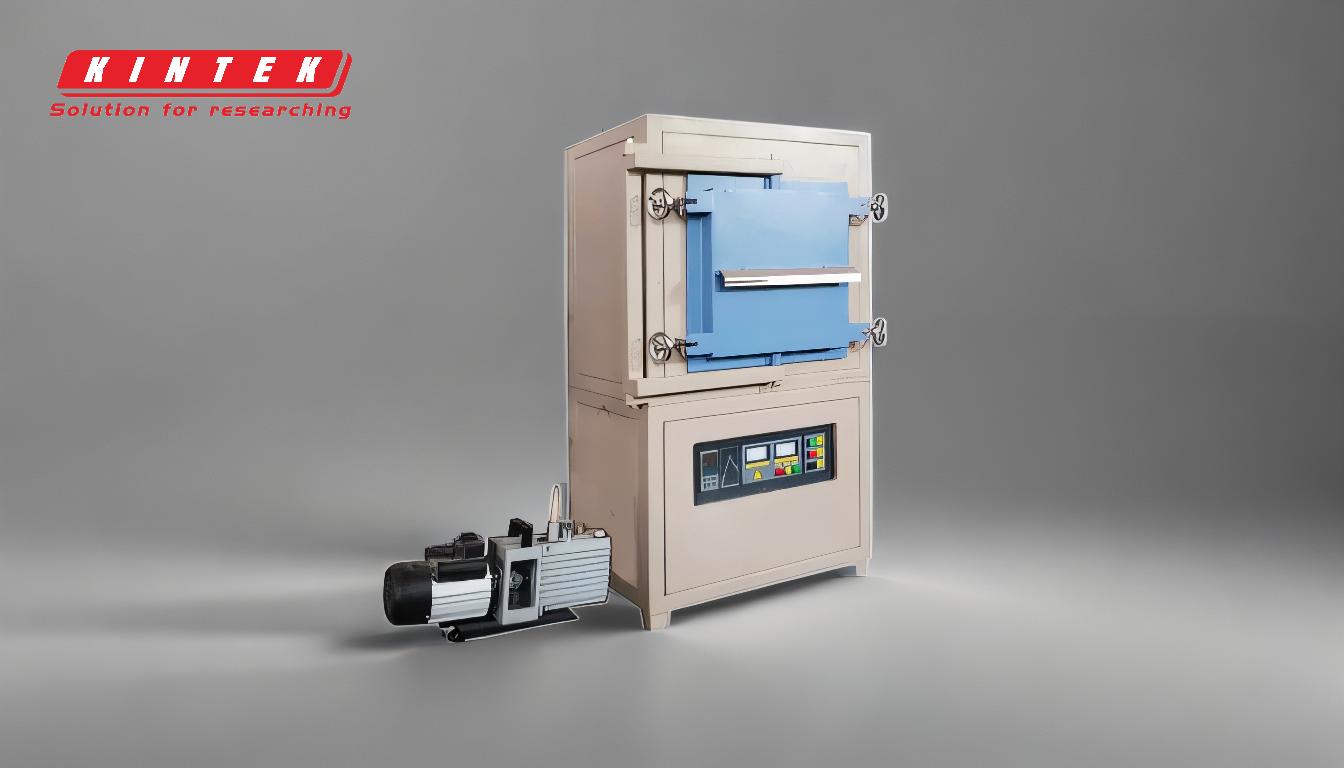
-
Relieving Internal Stresses:
- Explanation: Internal stresses can develop in materials during manufacturing processes such as casting, machining, or cold working. These stresses can lead to material failure or deformation during service. Annealing helps to alleviate these stresses by allowing the material to reach a thermal equilibrium state, redistributing and reducing internal strains.
- Impact: This makes the material more stable and less prone to cracking or warping under stress, which is particularly important for components subjected to mechanical loads.
-
Improving Ductility and Reducing Hardness:
- Explanation: Annealing increases the ductility (ability to deform without breaking) and reduces the hardness of a material. This is achieved by reducing the number of dislocations in the crystal structure, which makes the material more pliable and easier to work with.
- Impact: Enhanced ductility makes the material more suitable for processes like machining, cold working, or forming, where flexibility is required. Reduced hardness also improves machinability, allowing for smoother cutting and shaping.
-
Creating a Uniform and Homogeneous Structure:
- Explanation: During annealing, the material is heated to a temperature above its recrystallization point, which allows the grains within the material to reform into a more uniform and homogeneous structure. This process eliminates irregularities and inconsistencies in the material's internal structure.
- Impact: A uniform structure improves the material's mechanical properties, such as strength and toughness, and enhances its overall quality and performance.
-
Enhancing Physical and Chemical Properties:
- Explanation: Annealing can improve the physical properties of materials, such as density, strength, and thermal stability. In some cases, it can also enhance chemical properties, making the material more resistant to corrosion or other environmental factors.
- Impact: This makes annealed materials stronger, lighter, and more durable, which is beneficial for applications requiring high performance and longevity.
-
Stabilizing Surface Coatings:
- Explanation: For materials with surface coatings, annealing helps to stabilize the coating by ensuring it adheres properly to the base material. This prevents issues like peeling or cracking of the coating during use.
- Impact: Stabilized coatings improve the material's appearance, functionality, and resistance to wear and tear, extending its service life.
-
Improving Machinability and Workability:
- Explanation: By reducing hardness and increasing ductility, annealing makes materials easier to machine and work with. This is particularly important for complex manufacturing processes where precision and ease of shaping are required.
- Impact: Improved machinability reduces production costs and time, while also minimizing the risk of defects during manufacturing.
-
Applications in Various Industries:
- Explanation: Annealing is widely used in industries such as metallurgy, ceramics, and electronics. For example, in steel manufacturing, annealing is used to prepare the material for further processing, while in ceramics, it enhances the material's density and strength.
- Impact: The versatility of annealing makes it a valuable process across multiple industries, contributing to the production of high-quality, durable, and reliable materials.
In summary, annealing serves as a vital process for optimizing material properties, ensuring they meet the demands of specific applications. By relieving internal stresses, improving ductility, and creating a uniform structure, annealing enhances the overall performance, workability, and longevity of materials.
Summary Table:
Key Benefit | Explanation | Impact |
---|---|---|
Relieving Internal Stresses | Reduces internal strains caused by manufacturing processes. | Increases material stability and reduces risk of cracking or warping. |
Improving Ductility & Reducing Hardness | Makes materials more pliable and easier to work with. | Enhances machinability and suitability for cold working or forming. |
Creating a Uniform Structure | Forms a homogeneous internal structure by heating above recrystallization temp. | Improves mechanical properties like strength and toughness. |
Enhancing Physical & Chemical Properties | Boosts density, strength, and corrosion resistance. | Produces stronger, lighter, and more durable materials. |
Stabilizing Surface Coatings | Ensures proper adhesion of coatings to the base material. | Improves appearance, functionality, and resistance to wear and tear. |
Improving Machinability | Reduces hardness and increases ductility for easier shaping. | Lowers production costs and minimizes defects during manufacturing. |
Applications in Various Industries | Used in metallurgy, ceramics, and electronics for material optimization. | Contributes to high-quality, durable, and reliable material production. |
Learn how annealing can optimize your materials—contact our experts today for tailored solutions!