Hot isostatic pressing (HIP) is a manufacturing process that applies high temperature and pressure to materials to improve their density and mechanical properties. The maximum pressure used in HIP typically ranges between 15,000 psi to 44,000 psi (100 MPa to 300 MPa). This process is highly effective in eliminating porosity, enhancing material strength, and producing components with uniform density and fine grain structure. The combination of high pressure and temperature allows for the creation of high-quality parts that can withstand demanding environments, making HIP a preferred method in industries requiring robust and reliable materials.
Key Points Explained:
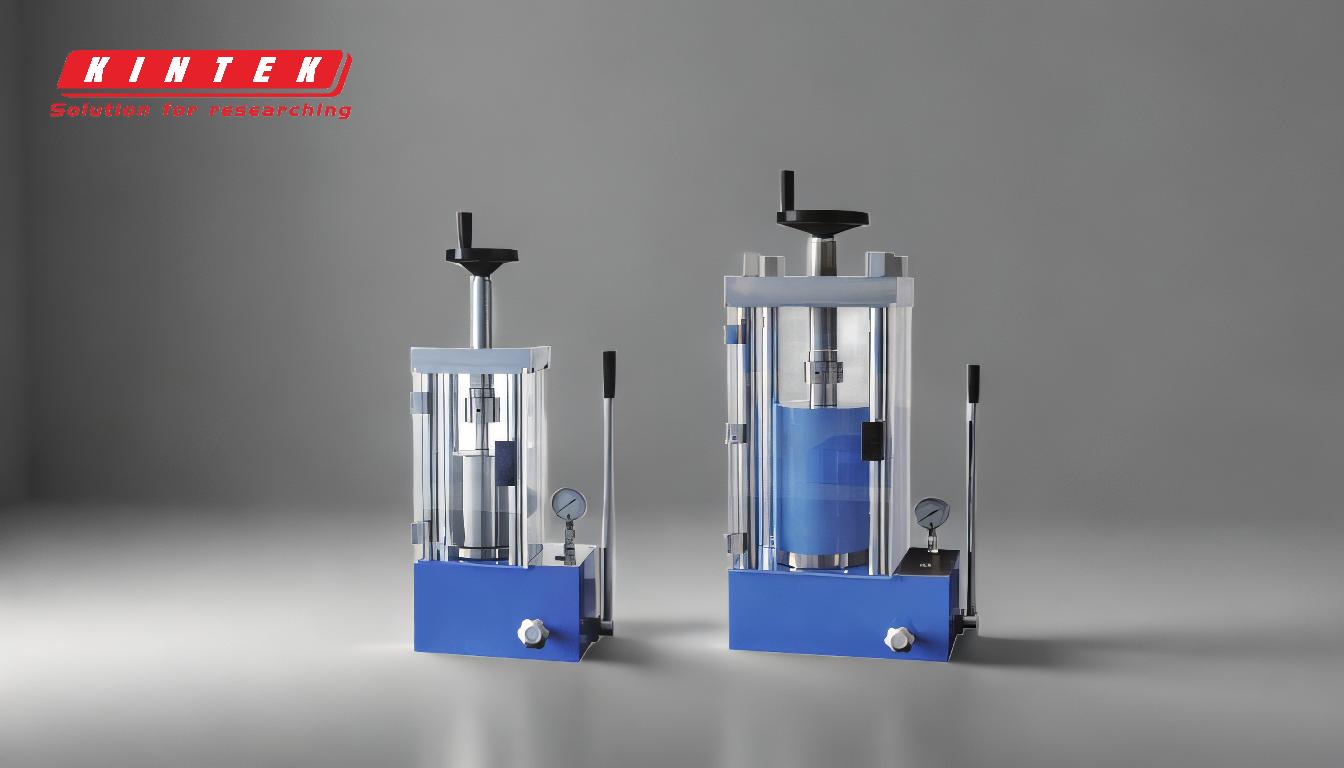
-
Pressure Range in Hot Isostatic Pressing:
- The work pressures in hot isostatic pressing (HIP) commonly range from 15,000 psi to 44,000 psi (100 MPa to 300 MPa). This high-pressure environment is crucial for achieving the desired material properties, such as increased density and improved mechanical strength.
-
Uniform Pressure Application:
- In HIP, the pressure is applied uniformly in all directions due to the isostatic nature of the process. This uniform pressure ensures that the material is compacted evenly, minimizing defects and ensuring consistent density throughout the component.
-
Temperature Control:
- Precise temperature control is achieved by heating the medium inside the high-pressure cylinder with a heat generator. The combination of high temperature and pressure facilitates the diffusion of atoms, leading to the elimination of porosity and the formation of a dense, uniform microstructure.
-
Advantages of Hot Isostatic Pressing:
- Elimination of Porosity: HIP effectively removes internal porosity, resulting in components with near-full density.
- Improved Mechanical Properties: The process enhances resistance to heat, wear, fatigue, and abrasion.
- Higher Productivity: HIP allows for more efficient production of high-quality parts.
- Reduced Scrap and Losses: The process minimizes material waste and defects.
- Lighter Designs: Components can be designed with reduced weight without compromising strength.
- Better Ductility and Toughness: HIP improves the material's ability to deform without breaking and its resistance to fracture.
- Reduced Property Fluctuations: The process ensures consistent material properties throughout the component.
- Longer Service Life: Components produced via HIP have a longer operational lifespan due to their enhanced properties.
- Metallurgical Bonds: HIP can form strong bonds between different materials, enabling the creation of composite structures.
-
Comparison with Hot Pressing:
- Compared to traditional hot pressing methods, HIP operates at lower temperatures while producing products with higher density and better mechanical properties. This makes HIP a more efficient and effective process for producing high-performance components.
-
Applications of Hot Isostatic Pressing:
- HIP is widely used in industries such as aerospace, automotive, medical, and energy, where high-strength, durable materials are essential. The process is particularly beneficial for manufacturing components that must withstand extreme conditions, such as turbine blades, medical implants, and structural parts.
In summary, hot isostatic pressing is a powerful manufacturing technique that leverages high pressure and temperature to produce materials with superior density, strength, and uniformity. The maximum pressure used in HIP, typically ranging from 15,000 psi to 44,000 psi, is a critical factor in achieving these desirable material properties. The process offers numerous advantages, including the elimination of porosity, improved mechanical properties, and the ability to create complex shapes, making it an invaluable tool in modern manufacturing.
Summary Table:
Aspect | Details |
---|---|
Pressure Range | 15,000 psi to 44,000 psi (100 MPa to 300 MPa) |
Uniform Pressure | Applied evenly in all directions, ensuring consistent density |
Temperature Control | Precise heating for uniform microstructure and porosity elimination |
Key Advantages | - Eliminates porosity - Enhances mechanical properties - Reduces scrap |
Applications | Aerospace, automotive, medical, energy |
Learn how hot isostatic pressing can transform your materials—contact us today!