The melting process in an induction furnace involves converting solid metal into a liquid state using electromagnetic induction. This process is highly efficient, cost-effective, and environmentally friendly compared to traditional melting methods. Key factors influencing the process include temperature, power input, and the presence of impurities. Induction furnaces, particularly those using IGBT technology, offer advantages such as reduced power consumption, faster melting rates, and the ability to produce high-quality, homogeneous metals. The process includes steps like crucible preparation, charge loading, melting, refining, and pouring. Overall, induction furnaces are widely used in industries requiring precise and consistent metal melting.
Key Points Explained:
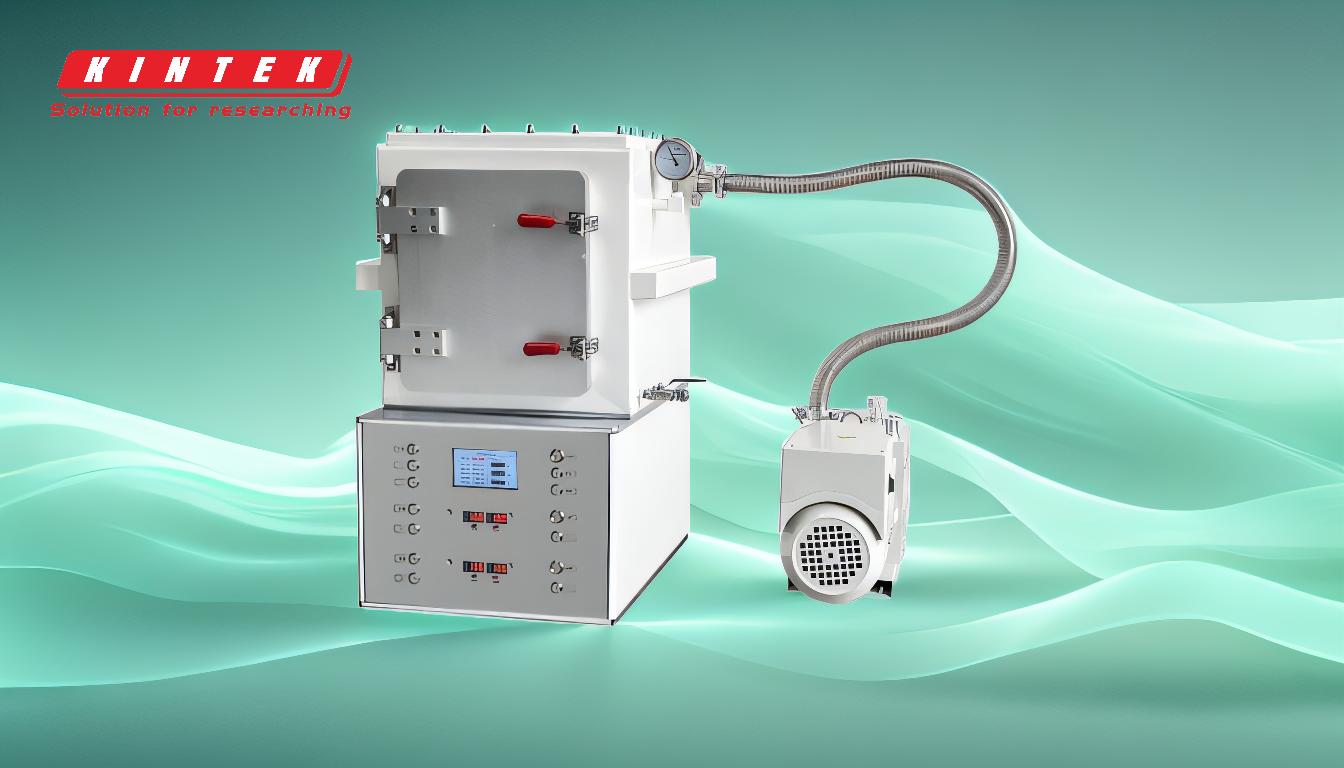
-
Principle of Induction Melting:
- Induction furnaces use electromagnetic induction to generate heat within the metal itself. An alternating current passes through a coil, creating a magnetic field that induces eddy currents in the metal, causing it to heat up and melt.
- This method eliminates the need for an electric arc, reducing metal burning and ensuring a more homogeneous melt.
-
Factors Influencing the Melting Process:
- Temperature: Higher temperatures accelerate melting but must be controlled to avoid overheating.
- Power Input: The melting rate is directly proportional to the power supplied. For example, a 325 kW IGBT induction furnace can melt steel at a rate of 520 kg/hour.
- Impurities and Slags: The presence of impurities can affect the quality of the melt, while slags help in refining the metal by removing unwanted elements.
-
Advantages of Induction Melting:
- Energy Efficiency: Induction furnaces consume less power compared to traditional methods, reducing operational costs.
- Quality Control: The electrodynamic circulation of the molten metal ensures a homogeneous mass, resulting in high-quality products.
- Environmental Benefits: Reduced heat loss and minimal emissions make induction melting an eco-friendly option.
- Automation: Modern induction furnaces are easy to automate, improving consistency and reducing labor costs.
-
Steps in the Melting Process:
- Crucible Preparation: The crucible, made of refractory material, is selected and prepared to withstand high temperatures.
- Charge Loading: Metal scraps or raw materials are loaded into the crucible.
- Melting and Refining: The metal is heated until it melts, and impurities are removed using slags or other refining agents.
- Pouring: The molten metal is poured into molds or transferred for further processing.
-
Applications and Industry Use:
- Induction melting is widely used in industries such as steel production, foundries, and metal recycling. Its ability to produce high-quality metals with minimal waste makes it a preferred choice for precision manufacturing.
By leveraging the efficiency and precision of IGBT induction furnaces, industries can achieve faster melting rates, lower energy consumption, and superior metal quality, making it a cornerstone of modern metal processing.
Summary Table:
Aspect | Details |
---|---|
Principle | Electromagnetic induction generates heat within the metal, ensuring homogeneous melting. |
Key Factors | Temperature, power input, and impurities influence the melting process. |
Advantages | Energy-efficient, high-quality metal, eco-friendly, and easy to automate. |
Steps | Crucible preparation, charge loading, melting, refining, and pouring. |
Applications | Steel production, foundries, and metal recycling industries. |
Ready to optimize your metal melting process? Contact us today to learn more about induction furnaces!