Thin film deposition is a critical process in various industries, including electronics, optics, and coatings, where thin layers of material are deposited onto a substrate. The methods used for thin film deposition can be broadly categorized into chemical and physical techniques. Chemical methods, such as Chemical Vapor Deposition (CVD) and Atomic Layer Deposition (ALD), rely on chemical reactions to form the thin film. Physical methods, like Physical Vapor Deposition (PVD), involve the physical transfer of material from a source to the substrate through processes like evaporation or sputtering. Each method has its own advantages and is chosen based on the specific requirements of the application, such as film thickness, uniformity, and material properties.
Key Points Explained:
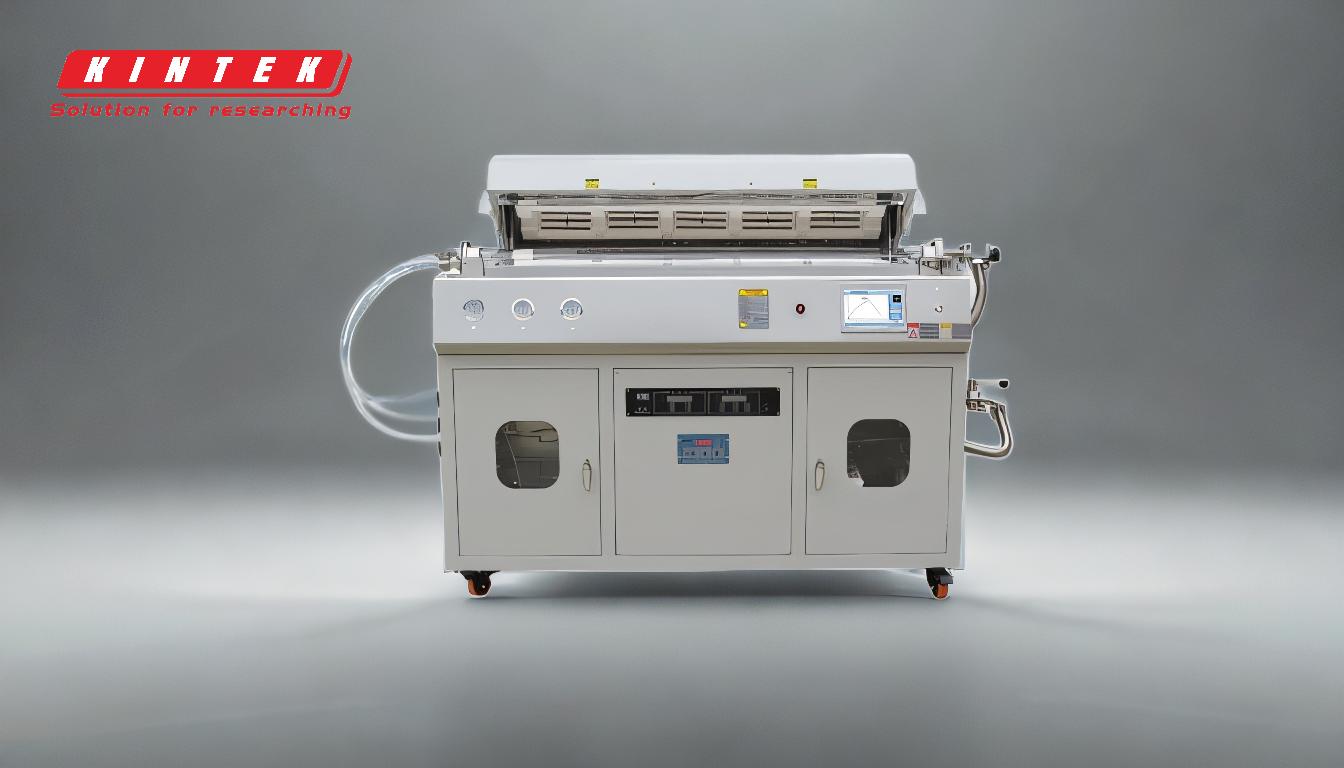
-
Physical Vapor Deposition (PVD):
- Process: PVD involves the physical transfer of material from a source to a substrate. This is typically done in a vacuum environment to prevent contamination.
-
Techniques: Common PVD techniques include:
- Thermal Evaporation: The source material is heated until it evaporates, and the vapor condenses on the substrate.
- Sputtering: A target material is bombarded with high-energy ions, causing atoms to be ejected and deposited onto the substrate.
- Electron Beam Evaporation: An electron beam is used to heat the source material, causing it to evaporate and deposit on the substrate.
- Pulsed Laser Deposition (PLD): A laser is used to ablate the target material, creating a plume of vapor that deposits on the substrate.
- Applications: PVD is widely used in the semiconductor industry, for coating tools, and in the production of optical coatings.
-
Chemical Vapor Deposition (CVD):
- Process: CVD involves the use of chemical reactions to deposit a thin film on a substrate. The process typically involves the introduction of a precursor gas into a reaction chamber, where it reacts on the substrate surface to form the desired film.
-
Variants: There are several variants of CVD, including:
- Plasma-Enhanced CVD (PECVD): Uses plasma to enhance the chemical reaction, allowing for lower temperatures and faster deposition rates.
- Low-Pressure CVD (LPCVD): Conducted at reduced pressures to improve film uniformity and reduce contamination.
- Atomic Layer Deposition (ALD): A specialized form of CVD where the film is deposited one atomic layer at a time, allowing for precise control over film thickness and composition.
- Applications: CVD is used in the production of semiconductors, coatings for wear resistance, and in the fabrication of nanomaterials.
-
Spray Pyrolysis:
- Process: Spray pyrolysis involves spraying a solution containing the desired material onto a heated substrate. The solution undergoes thermal decomposition, leaving behind a thin film.
- Advantages: This method is relatively simple and can be used to deposit a wide range of materials.
- Applications: Spray pyrolysis is commonly used in the production of solar cells, sensors, and thin-film transistors.
-
Other Methods:
- Electroplating: A chemical method where a thin film is deposited on a conductive substrate by passing an electric current through a solution containing metal ions.
- Sol-Gel: A chemical method that involves the transition of a solution (sol) into a gel, which is then dried and annealed to form a thin film.
- Dip Coating and Spin Coating: These methods involve immersing or spinning the substrate in a solution, followed by drying and annealing to form a thin film.
- Molecular Beam Epitaxy (MBE): A highly controlled PVD technique used to grow high-quality crystalline films, often used in the production of semiconductor devices.
-
Selection Criteria:
- Material Properties: The choice of deposition method depends on the material properties required, such as electrical conductivity, optical transparency, or mechanical strength.
- Substrate Compatibility: The method must be compatible with the substrate material and its thermal and chemical stability.
- Film Thickness and Uniformity: Different methods offer varying levels of control over film thickness and uniformity, which is critical for applications like semiconductor manufacturing.
- Cost and Scalability: The cost of the deposition process and its scalability for large-scale production are also important considerations.
In conclusion, the method used for thin film deposition depends on the specific requirements of the application, including the desired material properties, substrate compatibility, and production scale. Each method has its own advantages and limitations, and the choice of technique is often a balance between these factors.
Summary Table:
Method | Process | Techniques | Applications |
---|---|---|---|
Physical Vapor Deposition (PVD) | Physical transfer of material in a vacuum environment. | Thermal Evaporation, Sputtering, Electron Beam Evaporation, Pulsed Laser Deposition | Semiconductor industry, tool coatings, optical coatings. |
Chemical Vapor Deposition (CVD) | Chemical reactions to deposit thin films. | Plasma-Enhanced CVD (PECVD), Low-Pressure CVD (LPCVD), Atomic Layer Deposition (ALD) | Semiconductors, wear-resistant coatings, nanomaterials. |
Spray Pyrolysis | Spraying a solution onto a heated substrate for thermal decomposition. | N/A | Solar cells, sensors, thin-film transistors. |
Other Methods | Includes electroplating, sol-gel, dip coating, spin coating, and MBE. | N/A | Conductive films, optical coatings, high-quality crystalline films for semiconductors. |
Need help selecting the right thin film deposition method for your project? Contact our experts today!