Forging is a critical manufacturing process used across various industries due to its ability to produce parts with superior strength, custom shapes, and unique performance specifications. Among the different types of forging, the most common is open-die forging, also known as free forging. This method involves shaping metal between multiple dies that do not entirely enclose the material, allowing for greater flexibility in the size and shape of the final product. Open-die forging is widely used in industries such as automotive, aerospace, and oilfield parts due to its versatility and ability to handle large and complex components. Below, we explore the key aspects of open-die forging and why it is the most common type of forging.
Key Points Explained:
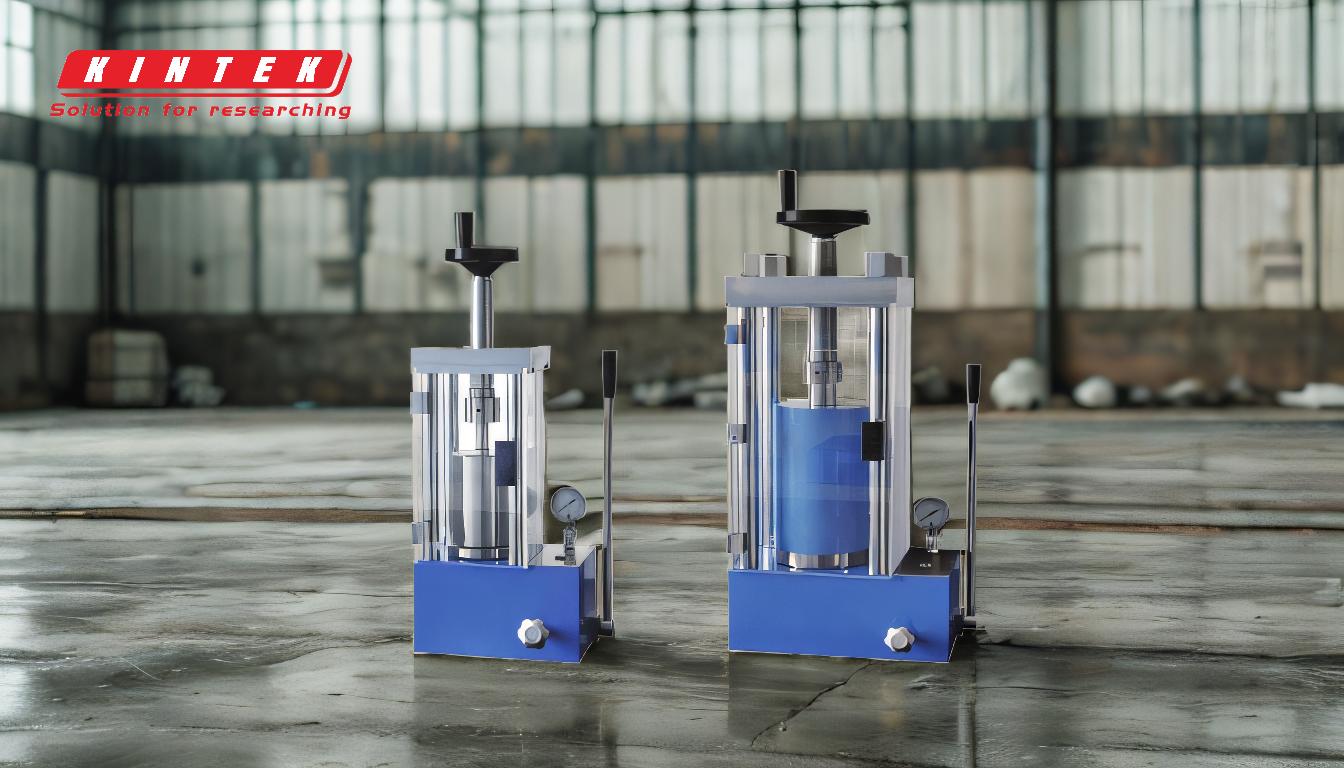
-
Definition of Open-Die Forging
Open-die forging is a process where metal is shaped between two or more dies that do not fully enclose the material. This allows for the creation of large, custom-shaped parts that are often used in heavy industries. The process involves repeated heating and hammering of the metal to achieve the desired shape and properties. -
Versatility in Applications
Open-die forging is highly versatile, making it suitable for a wide range of industries. For example:- Automotive: Used for producing crankshafts, axles, and other critical components.
- Aerospace: Ideal for creating large, high-strength parts like turbine shafts and landing gear components.
- Oilfield Parts: Used to manufacture drill bits, valves, and other heavy-duty equipment.
- Agricultural Equipment: Produces durable parts like plowshares and tractor components.
-
Superior Strength and Durability
The open-die forging process enhances the mechanical properties of the metal, such as strength, toughness, and fatigue resistance. This is achieved through the controlled deformation of the material, which aligns the grain structure and eliminates internal defects. -
Custom Shapes and Sizes
Unlike closed-die forging, which is limited by the shape of the dies, open-die forging allows for the creation of custom shapes and sizes. This flexibility is particularly valuable for producing large or uniquely shaped components that cannot be manufactured using other methods. -
Cost-Effectiveness for Large Parts
Open-die forging is often more cost-effective for producing large parts compared to other forging methods. The process requires less tooling and setup, making it a practical choice for low-volume or custom production runs. -
Common Materials Used
Open-die forging can be performed on a variety of metals, including:- Carbon and alloy steels
- Stainless steels
- Titanium
- Aluminum
- Nickel-based alloys
-
Environmental and Operational Benefits
The open-die forging process is energy-efficient and generates minimal waste, as excess material can often be reused. Additionally, the process can be automated to improve precision and reduce labor costs.
In summary, open-die forging is the most common type of forging due to its versatility, ability to produce high-strength parts, and suitability for large and custom components. Its widespread use across industries such as automotive, aerospace, and oilfield parts underscores its importance in modern manufacturing. For operations requiring superior part strength, custom shapes, and unique performance specifications, open-die forging remains a top choice.
Summary Table:
Aspect | Details |
---|---|
Definition | Shaping metal between dies that don't fully enclose the material. |
Applications | Automotive, aerospace, oilfield parts, agricultural equipment. |
Benefits | Superior strength, custom shapes, cost-effectiveness for large parts. |
Materials Used | Carbon/alloy steels, stainless steels, titanium, aluminum, nickel alloys. |
Environmental Benefits | Energy-efficient, minimal waste, reusable excess material. |
Interested in leveraging open-die forging for your manufacturing needs? Contact us today to learn more!