Quenching is a critical heat treatment process used to achieve desired mechanical properties in metals by rapidly cooling them. The most commonly used quenching medium is oil, particularly for medium carbon alloy steels, as it provides an optimal balance between cooling rate and minimizing distortion or cracking. Other quenching methods include water, brine, nitrogen, and air, each chosen based on the material and desired properties. Oil quenching is widely favored in industries like aerospace and automotive due to its effectiveness in enhancing strength and hardness while maintaining dimensional stability.
Key Points Explained:
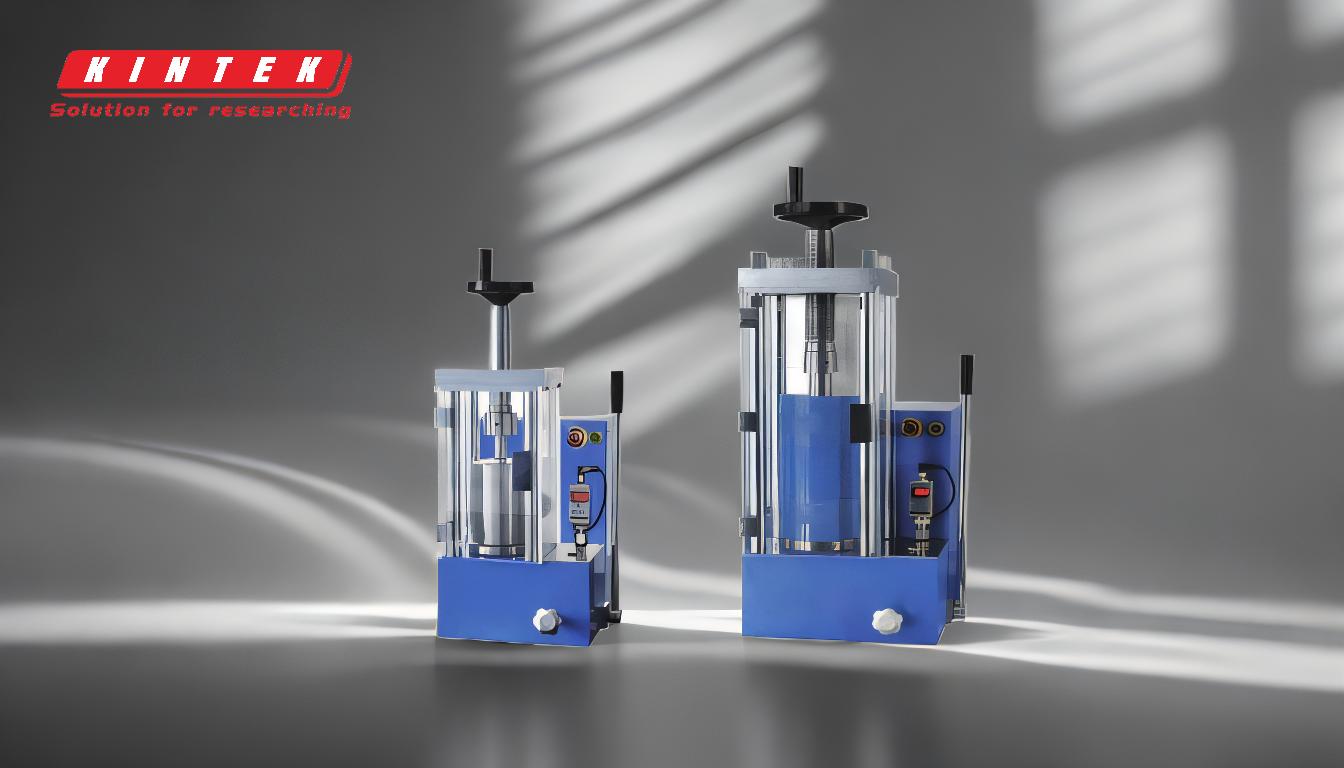
-
Definition of Quenching:
- Quenching is a heat treatment process that involves rapidly cooling a metal to achieve specific mechanical or physical properties. This rapid cooling locks the metal's microstructure in a hardened state, which is essential for applications requiring high strength and durability.
-
Common Quenching Media:
- Oil: The most commonly used quenching medium, especially for medium carbon alloy steels. Oil provides a controlled cooling rate, reducing the risk of cracking or distortion while achieving the desired hardness.
- Water and Brine: These are faster cooling mediums but are more likely to cause distortion or cracking, making them less suitable for certain applications.
- Nitrogen: Used in specialized applications, such as aerospace, where precise control over cooling rates is required.
- Air: The slowest cooling medium, used for materials that are less sensitive to rapid cooling.
-
Oil Quenching in Detail:
- Oil quenching is preferred for its ability to balance cooling speed and minimize thermal stress. It is particularly effective for hardening medium carbon alloy steels, as seen in the quench and temper process. This involves:
- Heating the metal above its transformation range.
- Rapidly cooling it to room temperature using oil.
- Reheating to a lower temperature to temper and achieve the final hardness range.
- Oil quenching is preferred for its ability to balance cooling speed and minimize thermal stress. It is particularly effective for hardening medium carbon alloy steels, as seen in the quench and temper process. This involves:
-
Applications of Oil Quenching:
- Oil quenching is widely used in industries such as aerospace, automotive, and tool manufacturing. It is ideal for components that require high strength, hardness, and dimensional stability, such as gears, shafts, and structural parts.
-
Advantages of Oil Quenching:
- Controlled Cooling Rate: Reduces the risk of cracking and distortion.
- Versatility: Suitable for a wide range of materials, including medium carbon alloy steels.
- Enhanced Properties: Improves strength, hardness, and wear resistance.
-
Comparison with Other Quenching Media:
- Water and Brine: Faster cooling rates but higher risk of distortion and cracking.
- Nitrogen: Used for specialized applications requiring precise cooling control.
- Air: Suitable for materials that do not require rapid cooling.
In summary, oil quenching is the most commonly used quenching medium due to its effectiveness, versatility, and ability to minimize defects. It plays a crucial role in achieving the desired mechanical properties in metals, making it a cornerstone of heat treatment processes in various industries.
Summary Table:
Quenching Medium | Cooling Rate | Key Benefits | Common Applications |
---|---|---|---|
Oil | Moderate | Controlled cooling, minimal distortion, versatile | Aerospace, automotive, tool manufacturing |
Water/Brine | Fast | Rapid cooling | Limited due to high risk of cracking |
Nitrogen | Precise | Specialized cooling control | Aerospace, high-precision industries |
Air | Slow | Gentle cooling | Materials less sensitive to rapid cooling |
Learn how oil quenching can optimize your metal heat treatment—contact our experts today!