The primary objective of an induction furnace is to efficiently and cleanly melt metals, such as scrap steel, pig iron, aluminum, copper, and precious metals, into high-quality molten metal with precise control over composition, temperature, and purity. This process involves melting solid raw materials, adjusting chemical compositions, removing harmful elements, and ensuring the molten metal is suitable for casting. Induction furnaces are favored for their energy efficiency, environmental friendliness, and ability to produce homogeneous molten metal with minimal contamination. They are widely used in foundries for producing castings with superior quality and consistency.
Key Points Explained:
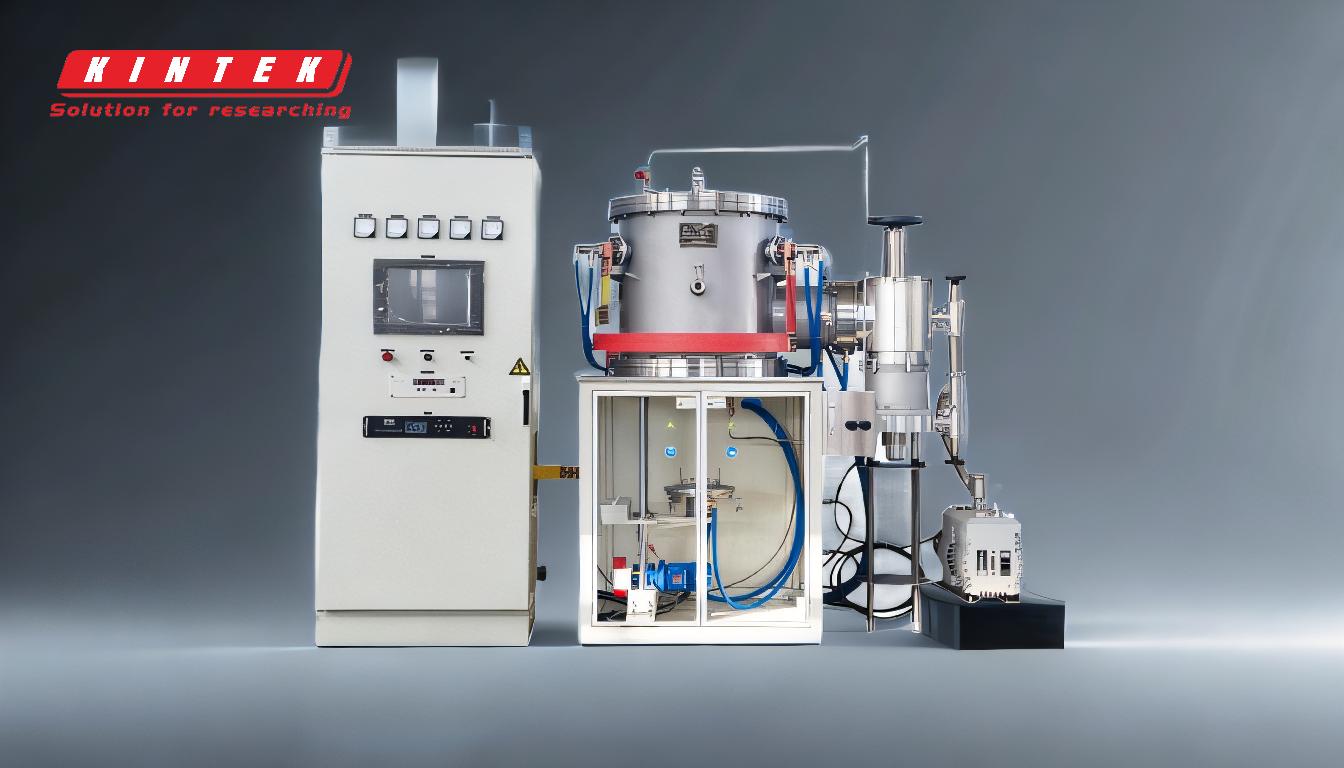
-
Efficient Melting of Metals:
- Induction furnaces are designed to melt solid raw materials like scrap steel, pig iron, aluminum, and other metals into molten form. This is achieved through electromagnetic induction, which generates heat directly within the metal, ensuring rapid and uniform heating.
- The process is faster and more energy-efficient compared to traditional melting methods, such as cupolas or gas furnaces.
-
Precise Control Over Composition and Temperature:
- Induction furnaces allow for precise adjustments to the chemical composition of the molten metal. For example, elements like silicon and carbon can be fine-tuned to meet specific requirements.
- The temperature of the molten metal is closely controlled, ensuring it reaches the optimal state for pouring and casting. This precision minimizes defects in the final product.
-
Purification and Removal of Harmful Elements:
- The furnace facilitates the removal of harmful elements like sulfur and phosphorus, which can degrade the quality of the metal. This purification process ensures the molten metal has low gas content and high inclusion quality.
- The electromagnetic stirring action in induction furnaces creates a homogeneous mixture, further enhancing the purity and consistency of the molten metal.
-
Energy Efficiency and Environmental Benefits:
- Induction furnaces are known for their low energy consumption and minimal environmental impact. They produce less noise, smoke, gas, dust, and waste residue compared to traditional melting methods.
- The absence of combustion or arcs makes the process cleaner and safer, reducing pollution and improving working conditions for operators.
-
Superior Casting Quality:
- The controlled melting process ensures that the molten metal has a small temperature difference between the core and surface, resulting in high-quality castings with fewer defects.
- The ability to operate in both atmospheric and vacuum conditions further reduces contamination, making induction furnaces ideal for producing high-purity metals.
-
Versatility in Applications:
- Induction furnaces are used in foundries to melt a wide range of metals, including iron, steel, copper, aluminum, and precious metals. Once melted, the metal is poured into molds to create castings.
- The flexibility to handle different metals and the ability to produce consistent results make induction furnaces a preferred choice in modern metalworking industries.
-
Cost Efficiency and Operational Advantages:
- The rapid heating and melting process reduces production time and costs. Induction furnaces also minimize material loss due to oxidation and decarburization, saving on raw material and die costs.
- The improved working environment and reduced maintenance requirements further contribute to cost savings and operational efficiency.
In summary, the objective of an induction furnace is to provide a clean, efficient, and controlled method for melting metals, ensuring high-quality molten metal with precise composition and temperature. This makes it an indispensable tool in modern foundries and metalworking industries.
Summary Table:
Key Feature | Description |
---|---|
Efficient Melting | Rapid and uniform heating using electromagnetic induction for faster melting. |
Precise Control | Adjust chemical composition and temperature for optimal casting results. |
Purification | Removes harmful elements like sulfur and phosphorus for high-purity metal. |
Energy Efficiency | Low energy consumption and minimal environmental impact. |
Superior Casting Quality | Produces high-quality castings with minimal defects and contamination. |
Versatility | Melts a wide range of metals, including steel, aluminum, and precious metals. |
Cost Efficiency | Reduces production time, material loss, and operational costs. |
Discover how an induction furnace can transform your metalworking process—contact us today for expert advice!