The PACVD (Plasma-Assisted Chemical Vapor Deposition) method is a specialized thin-film deposition technique that combines chemical vapor deposition (CVD) with plasma activation to enhance the deposition process. This method is widely used in industries such as semiconductors, optics, and protective coatings due to its ability to produce high-quality, uniform films at relatively low temperatures. PACVD leverages plasma to break down precursor gases into reactive species, which then deposit onto a substrate to form a thin film. This process allows for precise control over film properties such as thickness, composition, and structure, making it a versatile tool for advanced material fabrication.
Key Points Explained:
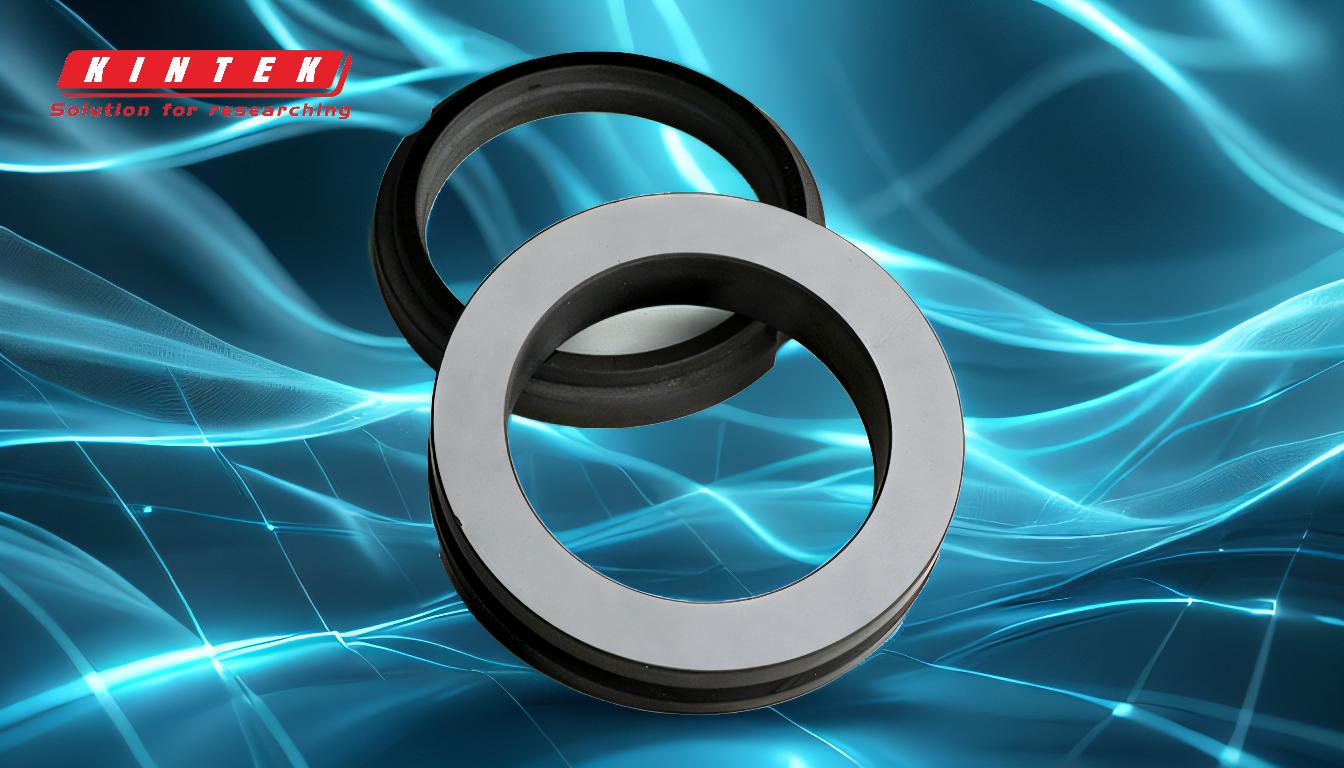
-
Definition of PACVD:
- PACVD stands for Plasma-Assisted Chemical Vapor Deposition. It is a hybrid technique that integrates the principles of chemical vapor deposition with plasma activation.
- The plasma is used to ionize and dissociate precursor gases, creating highly reactive species that facilitate the deposition process at lower temperatures compared to traditional CVD.
-
How PACVD Works:
- Precursor Introduction: Gaseous precursors are introduced into a vacuum chamber where the substrate is placed.
- Plasma Generation: A plasma is generated using an external energy source, such as radio frequency (RF) or microwave power. This plasma ionizes the precursor gases, breaking them into reactive ions and radicals.
- Deposition: The reactive species are deposited onto the substrate, forming a thin film. The plasma enhances the reaction kinetics, enabling deposition at lower temperatures.
- Film Growth: The process continues until the desired film thickness and properties are achieved.
-
Advantages of PACVD:
- Low-Temperature Processing: PACVD allows for thin-film deposition at temperatures much lower than traditional CVD, making it suitable for heat-sensitive substrates.
- Enhanced Film Quality: The use of plasma improves the uniformity, density, and adhesion of the deposited films.
- Versatility: PACVD can be used to deposit a wide range of materials, including metals, ceramics, and polymers, with precise control over film properties.
- Scalability: The process is scalable and can be adapted for industrial applications.
-
Applications of PACVD:
- Semiconductor Industry: PACVD is used to deposit dielectric layers, passivation layers, and other functional films in semiconductor devices.
- Optical Coatings: The method is employed to create anti-reflective, scratch-resistant, and protective coatings for optical components.
- Protective Coatings: PACVD is used to deposit hard, wear-resistant coatings on tools, molds, and other industrial components.
- Biomedical Applications: The technique is utilized to create biocompatible coatings for medical implants and devices.
-
Comparison with Other Deposition Methods:
- PACVD vs. CVD: PACVD operates at lower temperatures and offers better control over film properties due to plasma activation, whereas CVD typically requires higher temperatures.
- PACVD vs. PVD (Physical Vapor Deposition): PACVD involves chemical reactions and plasma activation, while PVD relies on physical processes like sputtering or evaporation. PACVD often results in better adhesion and conformal coverage.
-
Challenges and Limitations:
- Complexity: The process requires precise control over plasma parameters, gas flow rates, and substrate conditions, making it more complex than some other deposition methods.
- Equipment Cost: PACVD systems can be expensive due to the need for specialized vacuum and plasma generation equipment.
- Film Stress: The use of plasma can sometimes introduce stress in the deposited films, which may affect their mechanical properties.
-
Future Trends in PACVD:
- Nanotechnology: PACVD is being explored for the deposition of nanostructured films and coatings with unique properties.
- Green Chemistry: Efforts are being made to develop environmentally friendly precursors and reduce the environmental impact of the process.
- Integration with Other Technologies: PACVD is increasingly being combined with other deposition and patterning techniques to enable advanced material fabrication.
In summary, PACVD is a powerful and versatile thin-film deposition method that leverages plasma activation to enhance the chemical vapor deposition process. Its ability to produce high-quality films at low temperatures makes it an invaluable tool in various industries, from semiconductors to biomedical applications. Despite some challenges, ongoing advancements in PACVD technology continue to expand its capabilities and applications.
Summary Table:
Aspect | Details |
---|---|
Definition | Plasma-Assisted Chemical Vapor Deposition (PACVD) combines CVD with plasma. |
Key Advantage | Low-temperature processing, superior film quality, and versatility. |
Applications | Semiconductors, optical coatings, protective coatings, biomedical devices. |
Comparison with CVD | Lower temperatures, better control over film properties. |
Challenges | Complexity, high equipment costs, and potential film stress. |
Future Trends | Nanotechnology, green chemistry, and integration with advanced techniques. |
Learn how the PACVD method can transform your material fabrication process—contact our experts today!