Sintering is a critical manufacturing process used to create solid materials from powdered substances by applying heat and pressure without reaching the point of liquefaction. This process involves several stages, including shaping the powder, compacting it, heating it in a sintering furnace to facilitate particle bonding, and cooling it to form a cohesive structure. The physics of sintering revolves around the diffusion of particles, neck formation, and densification, which occur at temperatures below the material's melting point. This method is widely used in industries such as metallurgy, ceramics, and dentistry, where precise control of temperature, pressure, and atmosphere is essential to achieve high-quality and thermally resistant products.
Key Points Explained:
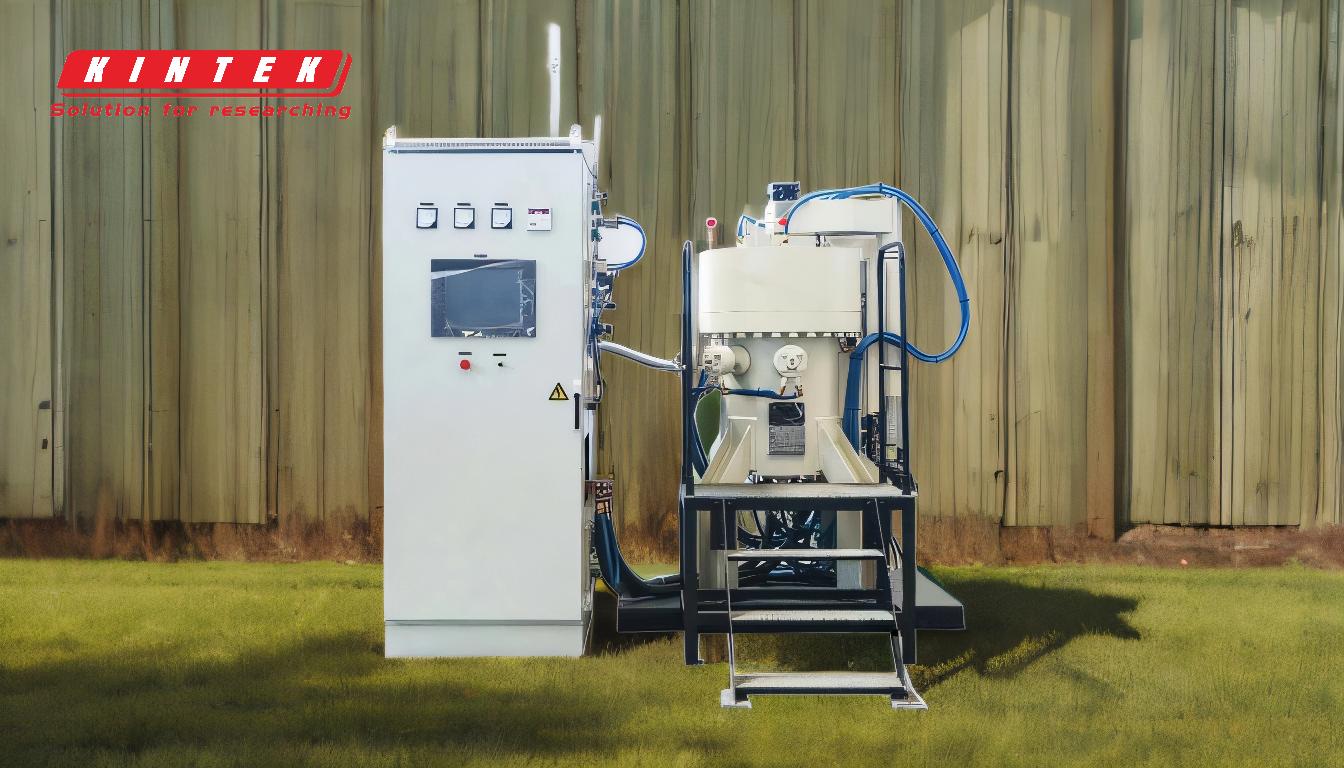
-
Definition and Purpose of Sintering:
- Sintering is a process that compacts and forms solid materials from powdered substances using heat and pressure, without melting the material completely.
- It is used in various industries, including metallurgy, ceramics, and dentistry, to create durable and thermally resistant products.
-
Stages of the Sintering Process:
- Forming the Powder: The raw material, usually in powder form, is shaped into the desired configuration.
- Compacting: The powder is compressed under pressure to eliminate voids and ensure uniformity.
- Heating: The compacted material is heated in a sintering furnace at controlled temperatures below the material's melting point. This stage facilitates particle bonding through diffusion, leading to neck formation and densification.
- Cooling: The sintered product is cooled to solidify into a rigid and cohesive structure.
-
Role of Bonding Agents:
- In the initial stage, a bonding agent (such as water, wax, or polymer) is used to stick the powder particles together.
- During heating, the bonding agent evaporates or burns away, allowing the primary particles to fuse at their surfaces or through an intermediate bonding agent like bronze.
-
Physics of Sintering:
- Diffusion: At elevated temperatures, atoms diffuse across particle boundaries, leading to the formation of necks between particles.
- Neck Formation: As particles bond, necks grow, reducing porosity and increasing the material's density.
- Densification: The material becomes more compact and dense as voids are eliminated, resulting in a stronger and more cohesive structure.
-
Importance of Temperature Control:
- Precise temperature control is crucial in the sintering process to ensure that particles bond effectively without melting completely.
- In specialized applications like dental sintering, maintaining the correct temperature, pressure, and atmosphere is essential for producing high-quality and stable restorations.
-
Applications of Sintering:
- Sintering is used to manufacture a wide range of products, including metal components, ceramic tiles, and dental prosthetics.
- The process is valued for its ability to produce complex shapes with high precision and excellent material properties.
By understanding the physics of sintering and the role of a sintering furnace, manufacturers can optimize the process to produce high-quality, durable, and thermally resistant materials for various industrial applications.
Summary Table:
Key Aspect | Description |
---|---|
Definition | A process that compacts powdered substances using heat and pressure. |
Stages | Forming, compacting, heating, and cooling. |
Physics | Diffusion, neck formation, and densification. |
Importance | Precise temperature control ensures effective particle bonding. |
Applications | Used in metallurgy, ceramics, and dentistry for high-quality products. |
Discover how sintering can transform your manufacturing process—contact our experts today!