The pressure in the Chemical Vapor Deposition (CVD) process varies depending on the specific type of CVD being used and the desired outcome. Most systems employ Low-Pressure CVD (LPCVD) with pressures ranging from 1 to 1500 Pa, as low pressures help prevent unwanted reactions and ensure uniform deposition thickness. However, Atmospheric Pressure CVD (APCVD) is also used, operating at or slightly below atmospheric pressure, which simplifies the system by eliminating the need for high vacuum pumps. The pressure plays a critical role in controlling the rate of chemical reactions, mass transfer, and the quality of the deposited film. Optimal pressure regulation is essential for achieving high-quality results, such as uniform film thickness, purity, and growth rate, especially in applications like graphene or diamond growth.
Key Points Explained:
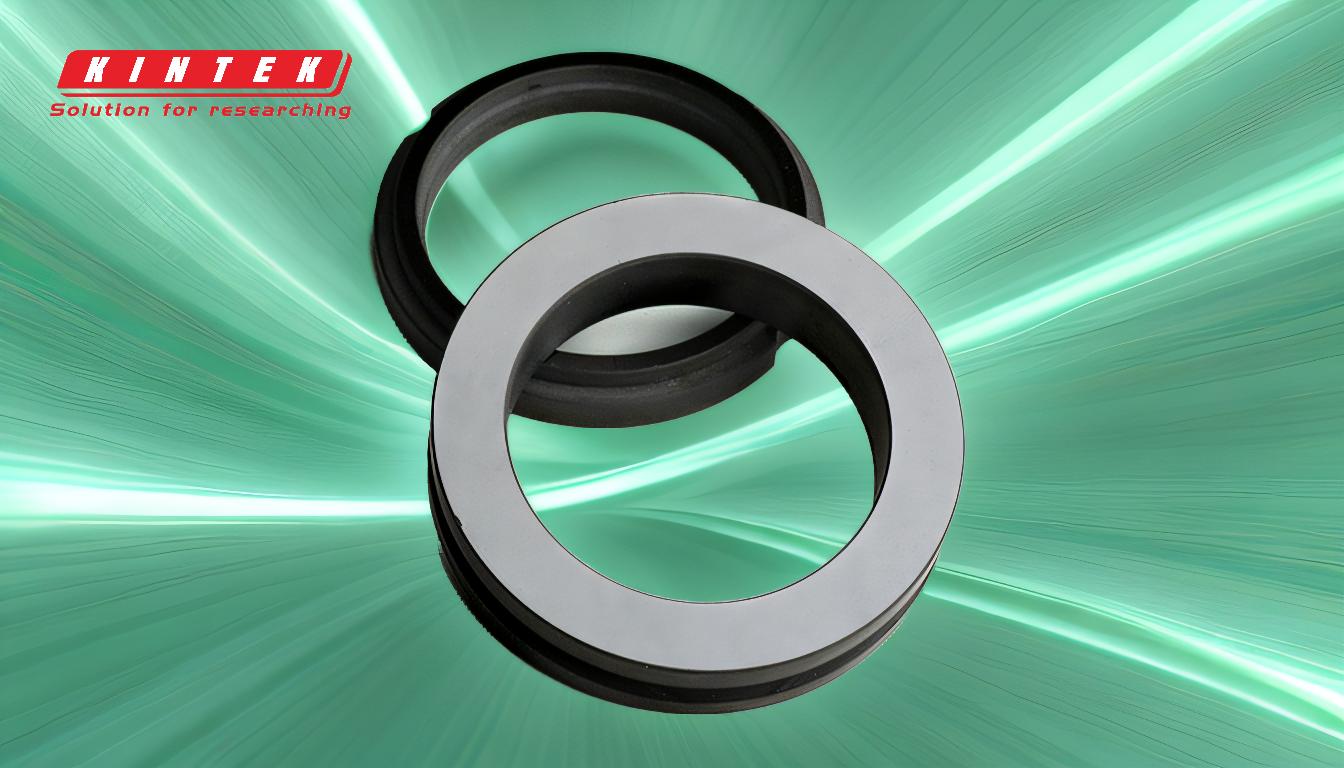
-
Pressure Range in CVD Processes:
- LPCVD (Low-Pressure CVD): Operates at pressures ranging from 1 to 1500 Pa. This low-pressure environment is preferred for its ability to prevent unwanted side reactions and ensure uniform deposition on the substrate.
- APCVD (Atmospheric Pressure CVD): Operates at or slightly below atmospheric pressure. This eliminates the need for high vacuum pumps, reducing costs and simplifying the system. APCVD is advantageous for achieving laminar flow, enabling non-line-of-sight deposition and conformal film coverage on irregular or closely packed substrates.
-
Role of Pressure in CVD:
- Chemical Reaction Rate: Pressure influences the rate of chemical reactions. At low pressures, the reaction phase can be limited, while at high pressures, the diffusion phase is more controlled.
- Mass Transfer: Pressure affects the transport of precursor molecules to the substrate surface. Low pressures result in shorter free path lengths for reactive radicals, promoting uniform nucleation of solid particles in the gas phase.
- Film Quality: Optimal pressure regulation ensures high-quality deposition, including uniform thickness, purity, and growth rate. For example, in diamond growth, the balance of pressure and temperature is crucial for achieving the desired color and purity.
-
Pressure in Plasma-Enhanced CVD (PECVD):
- In PECVD, low-pressure plasma is used, typically in the range of 10^−5 to 10 torr. This range is suitable for applications requiring precise control over the deposition process, such as in semiconductor manufacturing.
-
Pressure and System Design:
- LPCVD Systems: Require vacuum pumps to maintain low pressures, which can increase system complexity and cost.
- APCVD Systems: Operate at higher pressures, simplifying the system by eliminating the need for high vacuum pumps. This makes APCVD more cost-effective for certain applications.
-
Pressure and Deposition Uniformity:
- Low pressures in LPCVD reduce gas-phase reactions, ensuring that deposition occurs primarily on the substrate surface. This results in more uniform film thickness and better control over the deposition process.
- In APCVD, the higher pressure contributes to laminar flow properties, enabling conformal coverage on complex or irregular substrates.
-
Pressure and Growth Rate:
- The growth rate of the deposited material is influenced by pressure. For example, in diamond CVD, the balance of pressure and temperature directly affects the growth rate, purity, and color of the diamonds.
-
Pressure and By-Product Removal:
- Low pressures facilitate the desorption of by-product molecules from the substrate surface, making room for more precursor molecules. This is critical for maintaining a continuous and efficient deposition process.
-
Pressure in Graphene CVD:
- For graphene growth, strict control of pressure is essential to ensure high-quality results. Low pressures are often preferred to minimize unwanted reactions and achieve uniform thickness.
In summary, the pressure in the CVD process is a critical parameter that varies depending on the type of CVD and the desired outcome. Low pressures are commonly used to ensure uniform deposition and prevent unwanted reactions, while atmospheric pressures simplify system design and enable conformal coverage on complex substrates. Proper regulation of pressure is essential for achieving high-quality results in applications ranging from semiconductor manufacturing to diamond growth.
Summary Table:
CVD Type | Pressure Range | Key Benefits |
---|---|---|
LPCVD | 1 to 1500 Pa | Prevents unwanted reactions, ensures uniform deposition, and reduces gas-phase reactions. |
APCVD | At or below atmospheric | Simplifies system design, enables conformal coverage, and reduces costs. |
PECVD | 10^−5 to 10 torr | Ideal for precise control in semiconductor manufacturing. |
Need help optimizing your CVD process? Contact our experts today for tailored solutions!