Pressure sintering, also known as pressure-assisted sintering, is a manufacturing process that combines heat and applied pressure to densify powdered materials into solid components with minimal porosity. This process is widely used in industries requiring high-strength, low-porosity materials, such as aerospace, automotive, and electronics. Pressure sintering techniques include hot pressing, spark plasma sintering (SPS), and hot isostatic pressing (HIP). The process typically involves steps like powder preparation, compaction, heating under pressure, and cooling. By applying pressure during sintering, the process reduces sintering time, enhances material density, and improves mechanical properties. Variations like atmospheric pressure sintering and vacuum sintering offer tailored solutions for specific materials and applications.
Key Points Explained:
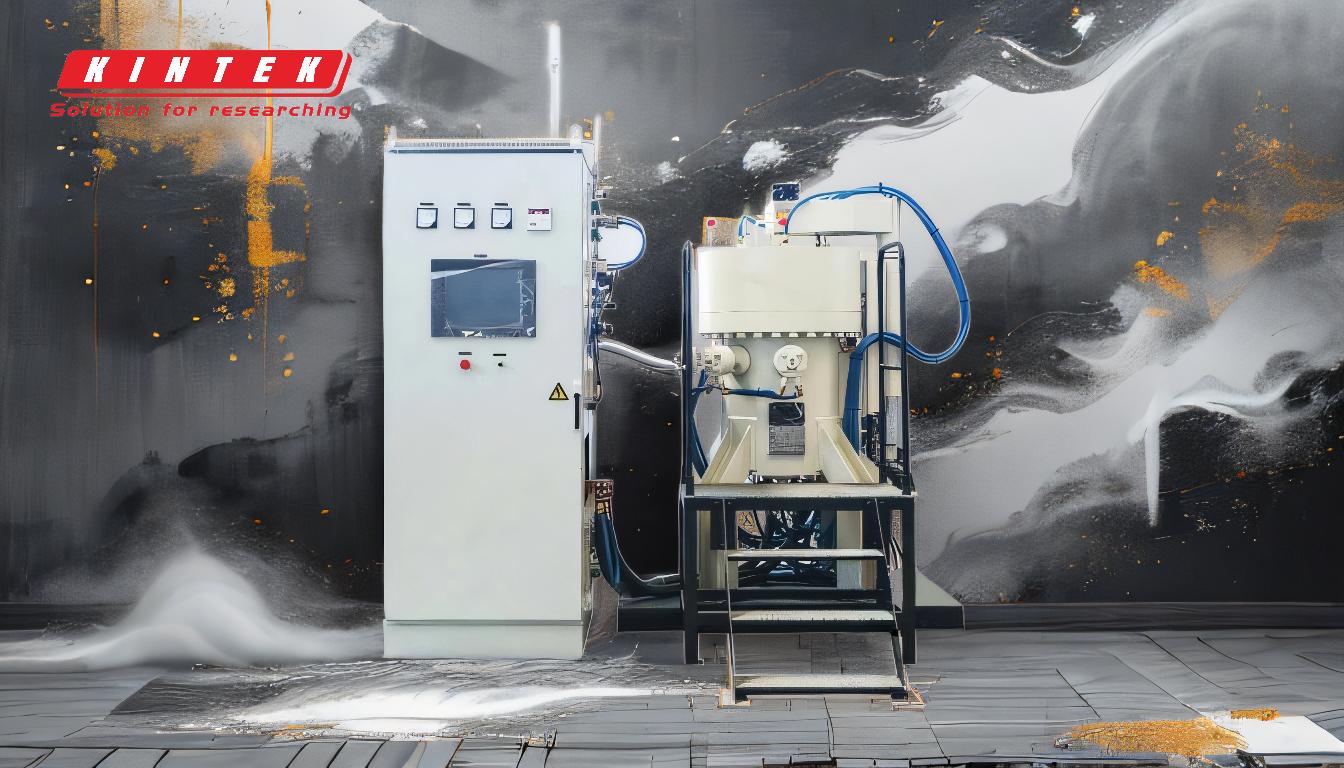
-
Definition and Purpose of Pressure Sintering:
- Pressure sintering is a manufacturing technique that uses heat and external pressure to densify powdered materials into solid components.
- It aims to reduce porosity, improve material density, and enhance mechanical properties like strength and durability.
- Common applications include producing high-performance ceramics, metals, and composites for industries requiring precision and reliability.
-
Key Techniques in Pressure Sintering:
- Hot Pressing: Combines heat and uniaxial pressure to densify materials in a die.
- Spark Plasma Sintering (SPS): Uses pulsed electric current and pressure to achieve rapid densification at lower temperatures.
- Hot Isostatic Pressing (HIP): Applies uniform pressure from all directions using a gas medium, ideal for complex shapes and eliminating internal defects.
-
Steps in the Pressure Sintering Process:
- Powder Preparation: Selecting and mixing raw materials to achieve the desired composition.
- Compaction: Pressing the powder into a specific shape using a die or mold.
- Heating and Pressurization: Applying heat and pressure simultaneously to bond particles and reduce porosity.
- Cooling: Gradual cooling to solidify the material and prevent cracking or warping.
-
Advantages of Pressure Sintering:
- Reduced Sintering Time: Pressure accelerates particle bonding, shortening the overall process.
- Improved Density: Minimizes porosity, resulting in stronger and more durable materials.
- Enhanced Material Properties: Achieves superior mechanical, thermal, and electrical characteristics.
-
Variations of Pressure Sintering:
- Atmospheric Pressure Sintering: Conducted under normal atmospheric pressure, often in an inert gas environment, suitable for materials like silicon carbide.
- Vacuum Sintering: Performed in a vacuum to eliminate impurities and oxidation, ideal for high-purity materials.
- Liquid-Phase Sintering: Introduces a liquid phase to enhance particle bonding and reduce sintering temperatures.
-
Applications of Pressure Sintering:
- Used in the production of advanced ceramics, metal alloys, and composite materials.
- Common in industries such as aerospace (turbine blades), automotive (engine components), and electronics (substrates and insulators).
-
Comparison with Conventional Sintering:
- Conventional sintering relies solely on heat, often resulting in higher porosity and longer processing times.
- Pressure sintering achieves better material properties and faster densification, making it more suitable for high-performance applications.
By understanding these key points, equipment and consumable purchasers can make informed decisions about selecting the appropriate sintering method for their specific needs, ensuring optimal material performance and cost-effectiveness.
Summary Table:
Aspect | Details |
---|---|
Definition | Combines heat and pressure to densify powdered materials into solid forms. |
Key Techniques | Hot Pressing, Spark Plasma Sintering (SPS), Hot Isostatic Pressing (HIP). |
Process Steps | Powder Preparation, Compaction, Heating & Pressurization, Cooling. |
Advantages | Reduced sintering time, improved density, enhanced material properties. |
Variations | Atmospheric, Vacuum, and Liquid-Phase Sintering. |
Applications | Aerospace, automotive, electronics (e.g., turbine blades, engine parts). |
Comparison | Superior to conventional sintering in density, strength, and processing. |
Discover how pressure sintering can optimize your material performance—contact our experts today!