Thermal evaporation is a widely used physical vapor deposition (PVD) technique for creating thin films on substrates. The process involves heating a target material in a vacuum chamber until it evaporates, forming a vapor that travels through the vacuum and deposits onto a substrate, creating a thin film. The heat source can be resistive heating (using a boat or coil) or electron beam heating. The method is favored for its simplicity, ability to produce high-purity films, and strong adhesion properties. It is commonly used in industries such as electronics, optics, and coatings for depositing metals, alloys, and other stable materials.
Key Points Explained:
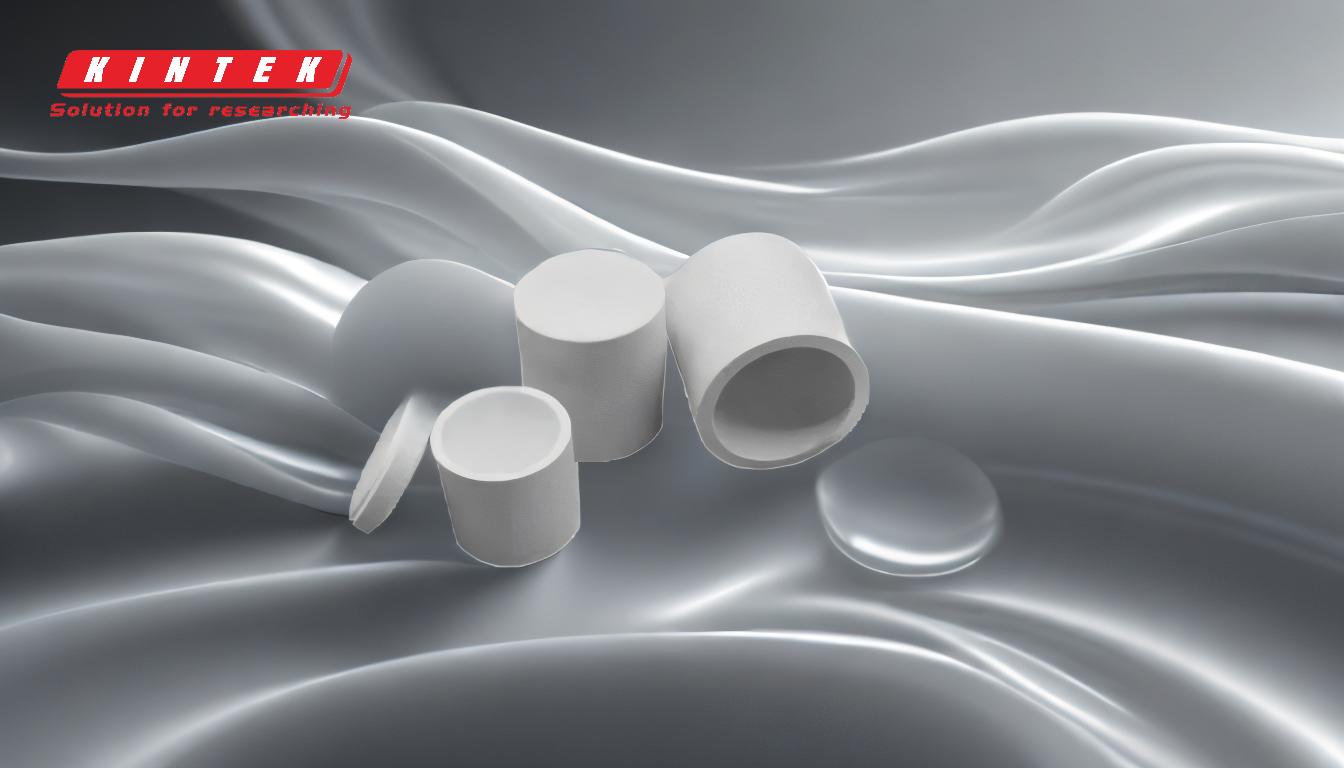
-
Vacuum Environment:
- Thermal evaporation takes place in a high vacuum chamber to minimize contamination and ensure efficient vapor travel.
- The vacuum reduces the presence of air molecules, preventing unwanted reactions and ensuring the vaporized material travels directly to the substrate.
-
Heating Mechanism:
- The target material is heated using either resistive heating (via a boat, coil, or basket) or electron beam heating.
- In resistive heating, an electric current passes through a refractory metal element, generating heat that melts and evaporates the material.
- Electron beam heating uses a focused beam of high-energy electrons to directly heat and vaporize the material.
-
Evaporation Process:
- The material is heated to its evaporation point, where it transitions from a solid or liquid state to a vapor.
- The vapor pressure created in the vacuum chamber allows the material to form a vapor cloud.
-
Vapor Travel and Deposition:
- The vaporized material travels through the vacuum chamber in a straight line due to the lack of air resistance.
- The vapor condenses onto the substrate, forming a thin film with good adhesion and purity.
-
Substrate Coating:
- The substrate is positioned above or near the evaporation source to ensure uniform coating.
- The resulting film thickness and uniformity depend on factors like material properties, evaporation rate, and substrate positioning.
-
Applications:
- Thermal evaporation is used in industries such as electronics (for metal contacts and interconnects), optics (for reflective and anti-reflective coatings), and decorative coatings.
- It is particularly suitable for depositing metals (e.g., aluminum, gold, silver) and alloys.
-
Advantages:
- High purity of deposited films due to the vacuum environment.
- Strong adhesion of the film to the substrate.
- Simple and cost-effective compared to other PVD techniques.
-
Limitations:
- Limited to materials that can be vaporized without decomposition.
- May not be suitable for materials with very high melting points or complex compositions.
By following these principles, thermal evaporation provides a reliable and efficient method for depositing thin films with precise control over thickness and composition.
Summary Table:
Key Aspect | Details |
---|---|
Vacuum Environment | High vacuum minimizes contamination and ensures efficient vapor travel. |
Heating Mechanism | Resistive heating (boat/coil) or electron beam heating. |
Evaporation Process | Material heated to vaporize, forming a vapor cloud in the vacuum chamber. |
Vapor Deposition | Vapor travels in a straight line, condensing onto the substrate. |
Applications | Electronics, optics, decorative coatings (e.g., aluminum, gold, silver). |
Advantages | High purity, strong adhesion, cost-effective. |
Limitations | Limited to materials that vaporize without decomposition. |
Interested in thermal evaporation for your thin film needs? Contact us today to learn more!