Vacuum deposition is a process used to deposit thin layers of material onto a surface in a controlled environment, typically under high vacuum conditions. The principle revolves around the evaporation or sublimation of a source material, which then condenses onto a substrate to form a thin film. This process ensures minimal contamination and allows for precise control over the thickness and properties of the deposited layer. The key steps involve creating a vacuum to eliminate impurities, heating the source material to induce evaporation, and allowing the vaporized material to condense on the substrate. Techniques such as physical vapor deposition (PVD) and chemical vapor deposition (CVD) are commonly used, each with specific applications and advantages.
Key Points Explained:
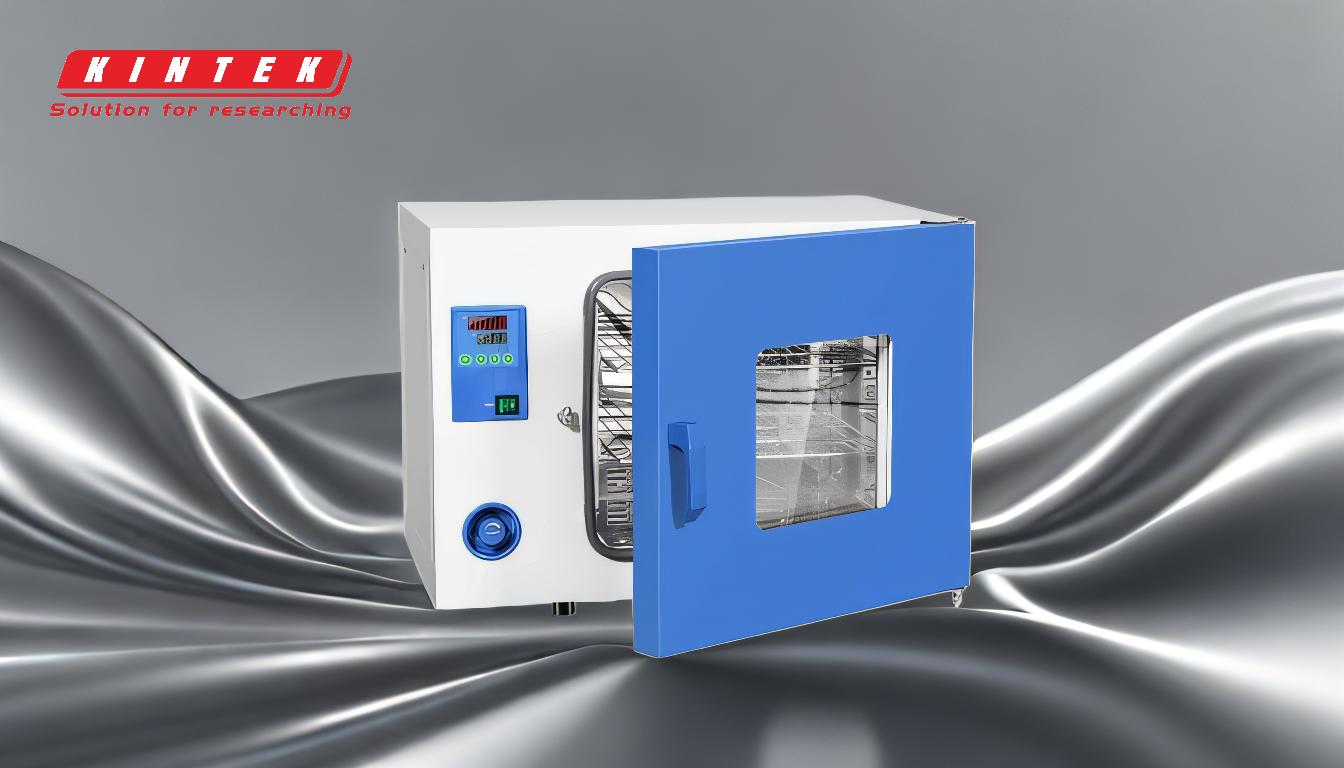
-
Definition and Purpose of Vacuum Deposition:
- Vacuum deposition is a technique used to deposit thin layers of material onto a substrate in a vacuum environment.
- The primary purpose is to create protective or functional layers on surfaces, such as metals, to enhance their properties (e.g., corrosion resistance, conductivity, or optical characteristics).
-
The Role of Vacuum in the Process:
- A vacuum environment is essential to eliminate air and other gases that could contaminate the deposition process.
- The absence of gas molecules ensures that the evaporated material travels unimpeded to the substrate, resulting in a uniform and high-quality film.
-
Evaporation and Condensation:
- The source material is heated to a point where it evaporates or sublimates, turning into a vapor.
- This vapor then travels through the vacuum and condenses onto the cooler substrate, forming a thin film.
- The thickness of the film can range from a single atomic layer to several micrometers, depending on the application.
-
Heat Source and Evaporation:
- A heat source, such as an electron beam or resistive heating, is used to provide the energy needed for the source material to evaporate.
- The choice of heat source depends on the material being deposited and the desired properties of the film.
-
Types of Vacuum Deposition Processes:
- Physical Vapor Deposition (PVD): Involves the physical transfer of material from the source to the substrate. Common PVD methods include sputtering and thermal evaporation.
- Chemical Vapor Deposition (CVD): Involves chemical reactions to deposit a thin film. The process typically occurs at low pressure and may use reactive gases to form the desired material on the substrate.
- Low-Pressure Plasma Spraying (LPPS): A variation of plasma spraying performed under vacuum conditions, allowing for the deposition of high-quality coatings with minimal oxidation.
-
Applications of Vacuum Deposition:
- Protective Coatings: Used to enhance the durability and resistance of metal parts against wear, corrosion, and oxidation.
- Optical Coatings: Applied to lenses and mirrors to improve reflectivity or anti-reflective properties.
- Semiconductor Manufacturing: Essential for depositing thin films in the production of integrated circuits and other electronic components.
- Decorative Coatings: Used to apply thin layers of metals like gold or chromium for aesthetic purposes.
-
Advantages of Vacuum Deposition:
- High Purity: The vacuum environment minimizes contamination, resulting in high-purity films.
- Precision Control: The process allows for precise control over film thickness and composition.
- Versatility: A wide range of materials can be deposited, including metals, ceramics, and polymers.
-
Challenges and Considerations:
- Equipment Cost: Vacuum deposition systems can be expensive due to the need for high-vacuum chambers and specialized heating sources.
- Complexity: The process requires careful control of parameters such as temperature, pressure, and deposition rate to achieve the desired film properties.
- Scalability: While effective for small-scale applications, scaling up the process for large-scale production can be challenging.
By understanding these key points, one can appreciate the intricate yet highly effective nature of vacuum deposition, making it a cornerstone technology in various industries.
Summary Table:
Aspect | Details |
---|---|
Definition | A process to deposit thin material layers on a substrate under vacuum. |
Purpose | Enhances surface properties like corrosion resistance and conductivity. |
Key Techniques | Physical Vapor Deposition (PVD), Chemical Vapor Deposition (CVD), LPPS. |
Applications | Protective coatings, optical coatings, semiconductor manufacturing, etc. |
Advantages | High purity, precision control, and versatility in material deposition. |
Challenges | High equipment cost, process complexity, and scalability issues. |
Discover how vacuum deposition can elevate your projects—contact our experts today!