The mesh belt furnace is a specialized piece of equipment used for heat treatment and thermo-chemical processing of small components. It operates in a fully automated manner, ensuring consistent and repeatable results. The process typically involves three main stages: annealing, recrystallization, and grain growth, often conducted under ammonia gas. Additionally, the furnace supports processes like carburizing, carbonitriding, hardening, and tempering. The system is designed to handle small elements, ensuring uniform treatment across all parts. While the furnace operates automatically, service personnel are responsible for loading and unloading the processed parts. This setup ensures efficiency, precision, and minimal human intervention during the heat treatment process.
Key Points Explained:
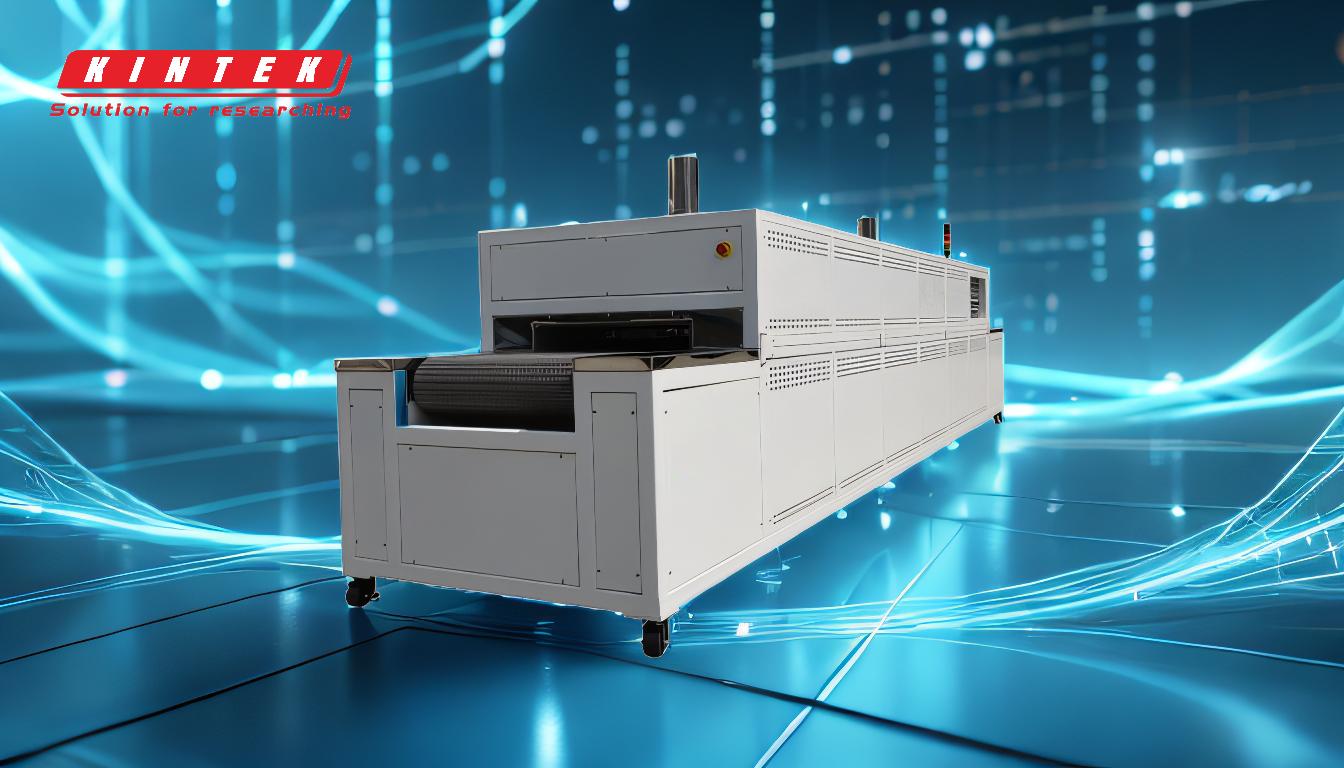
-
Three Main Stages of the Mesh Belt Furnace Process:
- Annealing: This stage involves heating the material to a specific temperature and then cooling it slowly to reduce hardness and improve ductility. It is often used to relieve internal stresses in metals.
- Recrystallization: During this stage, the material is heated to a temperature where new grains form, replacing the deformed grain structure. This process is crucial for restoring the material's properties after cold working.
- Grain Growth: This final stage involves heating the material to a higher temperature to allow the grains to grow larger, which can improve certain mechanical properties.
-
Automated Operation:
- The mesh belt furnace is fully automated, with a control system overseeing all operations. This ensures precision and consistency in the heat treatment process.
- Service personnel are only required to load the parts into the loader’s container and collect the processed parts after treatment. This minimizes human error and increases efficiency.
-
Supported Processes:
- Carburizing: A process that introduces carbon into the surface layer of low-carbon steel to increase hardness and wear resistance.
- Carbonitriding: Similar to carburizing but also introduces nitrogen into the surface layer, enhancing hardness and wear resistance while maintaining core toughness.
- Hardening: A process that increases the hardness of the material by heating it to a high temperature and then rapidly cooling it.
- Tempering: After hardening, tempering is performed to reduce brittleness and improve toughness by reheating the material to a lower temperature.
-
Design and Application:
- Mesh belt furnaces are specifically designed for the heat treatment and thermo-chemical treatment of small components. This ensures that each part receives uniform treatment, leading to consistent and repeatable results.
- The furnace is ideal for industries requiring precise control over the heat treatment process, such as automotive, aerospace, and jewelry manufacturing.
-
Advantages of Mesh Belt Furnaces:
- Homogeneous Treatment: The design ensures that all parts are treated uniformly, which is critical for maintaining consistent material properties.
- Repeatable Results: The automated nature of the furnace ensures that each batch of parts is treated under the same conditions, leading to repeatable and reliable outcomes.
- Efficiency: The fully automated process reduces the need for manual intervention, increasing throughput and reducing labor costs.
-
Safety and Monitoring:
- The furnace is equipped with monitoring systems to ensure that all processes are carried out safely and within the specified parameters. This reduces the risk of overheating or other issues that could compromise the quality of the treated parts.
In summary, the mesh belt furnace is a highly efficient and automated system designed for the precise heat treatment of small components. Its ability to perform various processes like annealing, hardening, and carburizing, combined with its automated operation, makes it an essential tool in industries requiring consistent and high-quality heat treatment results.
Summary Table:
Key Feature | Description |
---|---|
Automated Operation | Fully automated system for consistent and repeatable heat treatment processes. |
Main Processes | Annealing, recrystallization, grain growth, carburizing, hardening, tempering. |
Design | Optimized for small components, ensuring uniform treatment across all parts. |
Applications | Ideal for automotive, aerospace, and jewelry manufacturing industries. |
Advantages | Homogeneous treatment, repeatable results, high efficiency, and safety. |
Ready to optimize your heat treatment process? Contact us today to learn more about mesh belt furnaces!