The process of an arc melting furnace involves the use of an electric arc to generate extremely high temperatures, which are used to melt metals without altering their chemical properties. The furnace operates by converting high-voltage electricity into a low-voltage, high-current supply, which creates an arc between electrodes and the metal charge. This arc produces intense heat, melting the metal, which can then be poured into molds or shaped as needed. The process is efficient for melting scrap steel and other metals, maintaining their integrity while transforming them into a liquid state for further processing.
Key Points Explained:
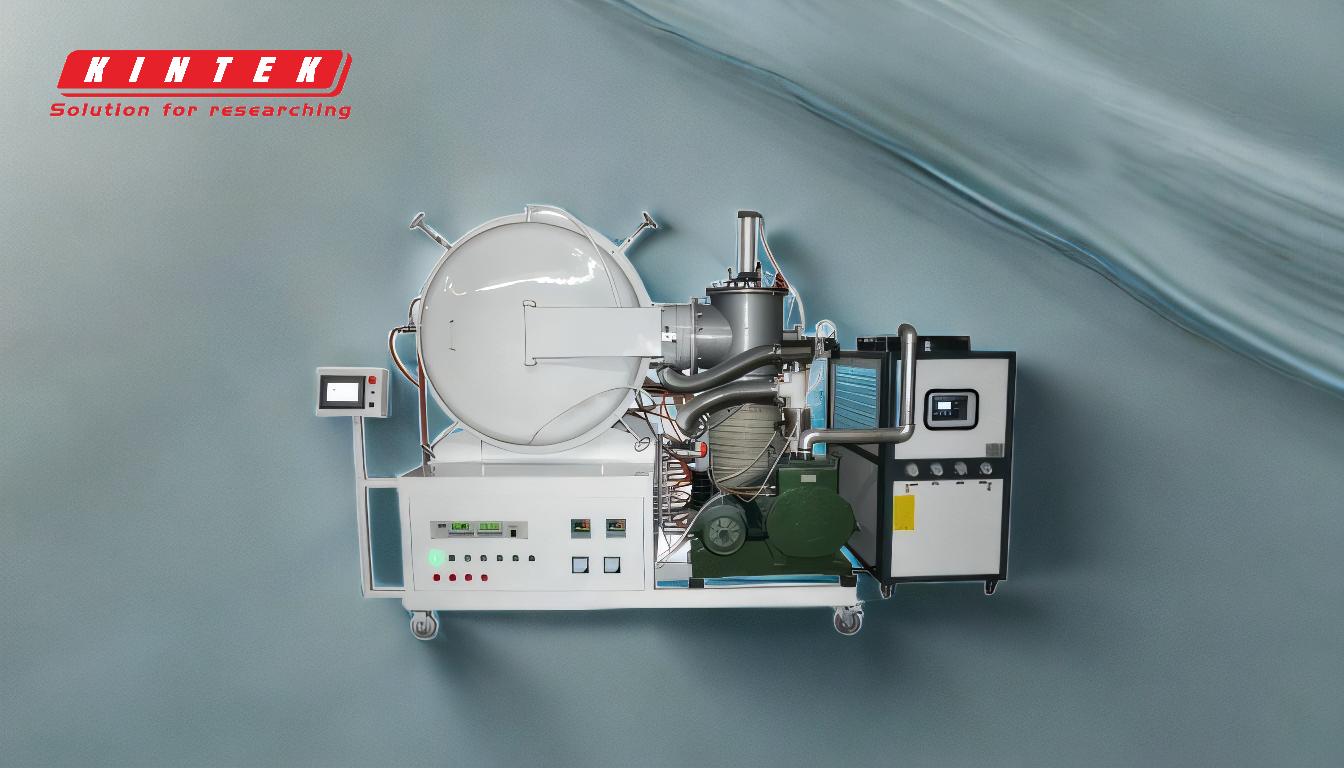
-
Electric Arc Generation:
- The core of the arc melting furnace is the electric arc, which is a self-sustaining discharge phenomenon.
- The arc is created by an instantaneous short circuit between the positive and negative poles of the electric welder, which converts standard 220V or 380V electricity into a low-voltage, high-current supply.
- This arc generates thermal plasma with temperatures high enough to melt metals.
-
Heating and Melting Process:
- The furnace heats the charged material (typically scrap steel or other metals) using the electric arc.
- The arc forms between graphitized electrodes and the metal charge, producing intense heat that melts the metal.
- The process ensures that the chemical properties of the metal remain unchanged, making it ideal for recycling and reprocessing metals.
-
Furnace Components:
- The furnace is equipped with burners and lances that create an atmosphere rich in oxygen and hydrogen.
- This atmosphere promotes more complete oxidation of the metal, enhancing the melting process.
- The furnace operates on three-phase electric current, ensuring a stable and consistent energy supply for the arc.
-
Post-Melting Processing:
- Once the metal is melted, it can be poured into molds to create specific shapes or pressed into sheets.
- This step is crucial for further manufacturing processes, allowing the molten metal to be transformed into usable products.
-
Applications and Advantages:
- Arc melting furnaces are primarily used in the recycling of scrap steel and other metals.
- The process is efficient and cost-effective, as it allows for the melting of large quantities of metal without the need for chemical alterations.
- The high temperatures and controlled atmosphere ensure that the metal is melted uniformly and with minimal impurities.
By understanding these key points, one can appreciate the efficiency and precision of the arc melting furnace process, which is essential for modern metal recycling and manufacturing industries.
Summary Table:
Aspect | Details |
---|---|
Electric Arc Generation | Converts high-voltage electricity into a low-voltage, high-current supply. |
Heating Process | Intense heat from the arc melts metals without altering their properties. |
Furnace Components | Burners, lances, and three-phase electric current ensure efficient melting. |
Post-Melting Processing | Molten metal is poured into molds or pressed into sheets for manufacturing. |
Applications | Ideal for recycling scrap steel and other metals efficiently. |
Discover how an arc melting furnace can revolutionize your metal processing—contact us today for expert advice!