Batch annealing is a heat treatment process used primarily for steel coils, where the material is heated, held at a specific temperature, and then cooled slowly over an extended period, typically around three days. Unlike continuous annealing, which processes steel strips quickly, batch annealing involves stacking coils, covering them, and using mobile furnaces to heat them intact. This method improves the material's ductility, reduces hardness, and eliminates internal stresses, making it more suitable for machining and coldworking processes. The process involves three key stages: recovery, recrystallization, and grain growth, which occur as the temperature increases and the material's microstructure evolves.
Key Points Explained:
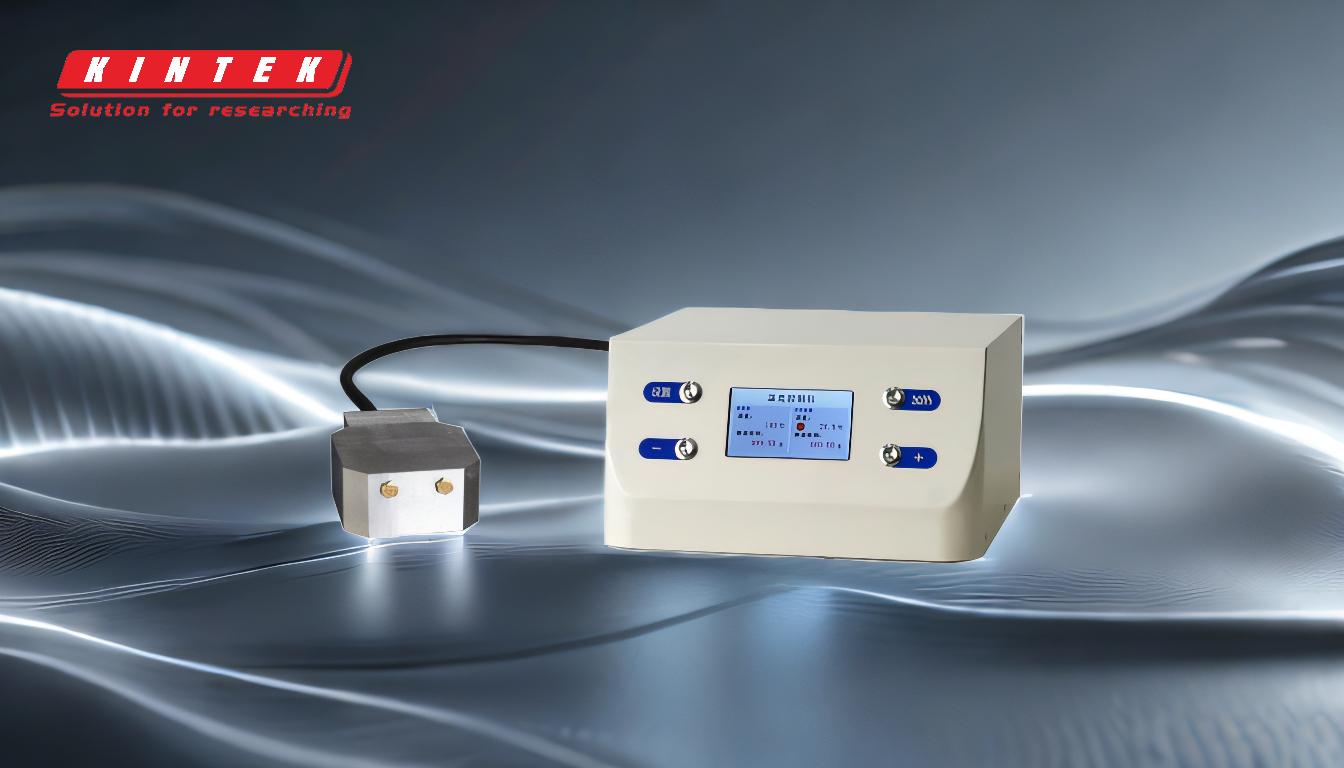
-
Batch Annealing Overview:
- Batch annealing is a slow, controlled heat treatment process used for steel coils.
- It differs from continuous annealing, which processes steel strips rapidly (in about 15 minutes).
- In batch annealing, steel coils are stacked four or five high on fixed bases, covered, and heated in mobile furnaces over approximately three days.
-
Key Stages of Batch Annealing:
- Recovery: At lower temperatures, internal stresses within the material begin to relax, and dislocations in the crystal structure start to rearrange.
- Recrystallization: As the temperature increases further, new, strain-free grains form, replacing the deformed grains. This stage reduces hardness and increases ductility.
- Grain Growth: At even higher temperatures, the newly formed grains grow, leading to a more uniform and homogeneous microstructure.
-
Steps in the Batch Annealing Process:
- Metal Heating: The steel coils are placed in the furnace and heated to a specific temperature, typically below the melting point but high enough to allow the crystalline structure to become fluid.
- Metal Insulation: The material is held at this temperature for a predetermined period, allowing defects in the crystal structure to repair themselves and ensuring uniformity in the microstructure.
- Metal Cooling: The material is cooled slowly, often in a controlled environment, to achieve the desired mechanical properties, such as increased ductility and reduced hardness.
-
Purpose and Benefits of Batch Annealing:
- Reduction of Hardness: Batch annealing reduces the hardness of the material, making it easier to machine and work with.
- Increase in Ductility: The process increases the material's ductility, allowing it to be shaped or formed without cracking.
- Stress Relief: Internal stresses that could lead to failure in service are relieved, improving the material's performance.
- Improved Microstructure: The process results in a more uniform and homogeneous internal structure, enhancing the material's overall properties.
-
Applications of Batch Annealing:
- Batch annealing is commonly used in the steel industry to prepare coils for further processing, such as cold rolling or forming.
- It is particularly useful for producing materials that require high ductility and low hardness, such as those used in automotive or construction applications.
-
Comparison with Continuous Annealing:
- Batch annealing is slower and more controlled than continuous annealing, which is a rapid process.
- Continuous annealing is typically used for thin steel strips, while batch annealing is used for thicker coils.
- Batch annealing allows for more precise control over the material's properties, making it suitable for applications requiring specific mechanical characteristics.
By understanding the batch annealing process, purchasers of equipment and consumables can make informed decisions about the heat treatment methods best suited for their specific applications, ensuring optimal material performance and cost-effectiveness.
Summary Table:
Aspect | Details |
---|---|
Process | Slow, controlled heat treatment for steel coils over ~3 days. |
Key Stages | Recovery, Recrystallization, Grain Growth. |
Steps | Heating, Insulation, Slow Cooling. |
Benefits | Reduced hardness, increased ductility, stress relief, improved microstructure. |
Applications | Steel industry, automotive, construction. |
Comparison | Slower and more controlled than continuous annealing. |
Discover how batch annealing can optimize your steel processing—contact us today for expert advice!