Chemical Vapor Deposition (CVD) is a sophisticated thin-film deposition process that involves the chemical reaction of gaseous precursors to form a solid material on a substrate. This process is widely used in various industries, including semiconductors, optics, and nanotechnology, due to its ability to produce high-quality, uniform coatings. The CVD process typically involves several key steps: the transport of reacting gaseous species to the surface, adsorption of these species, surface-catalyzed reactions, surface diffusion, nucleation and growth of the film, and finally, the desorption and removal of gaseous reaction products. Each step is crucial for ensuring the quality and properties of the final coating.
Key Points Explained:
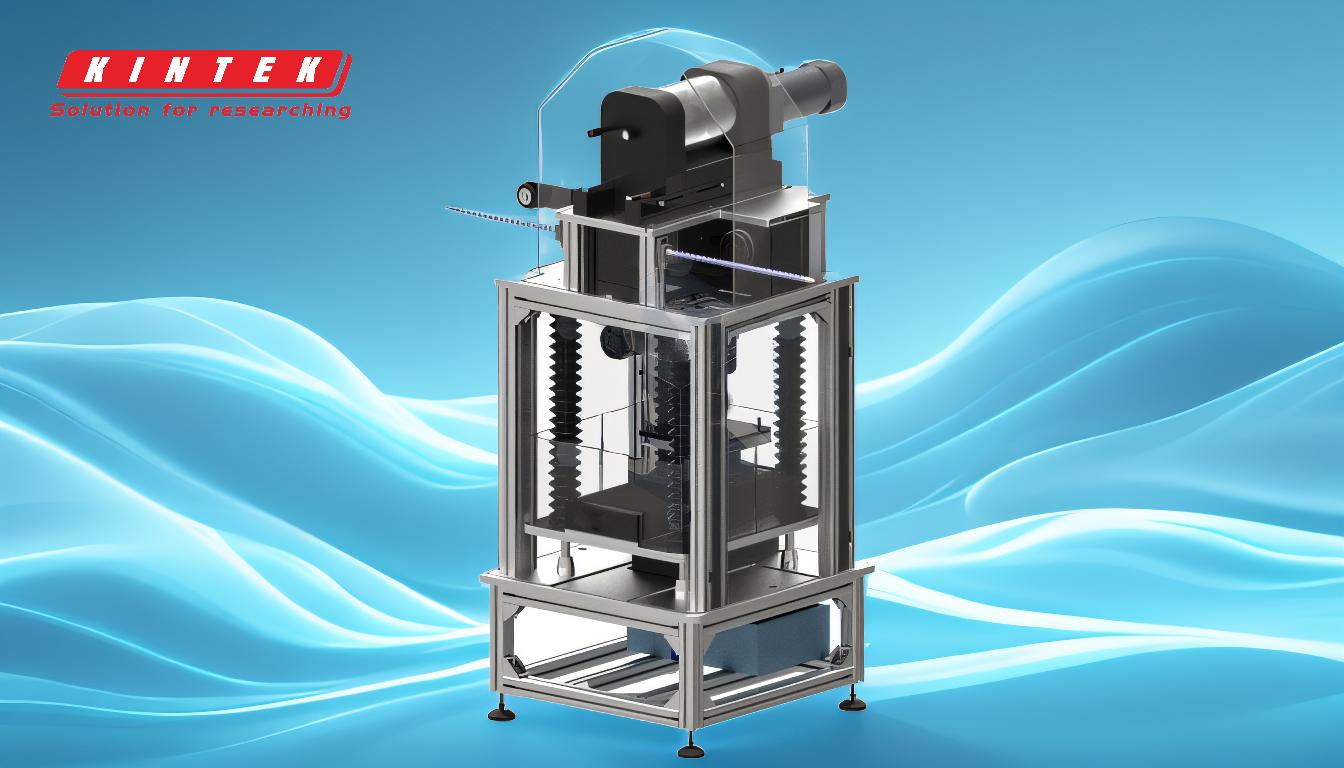
-
Transport of Reacting Gaseous Species to the Surface:
- The process begins with the introduction of gaseous precursors into a reaction chamber. These gases are transported to the substrate surface, often under controlled temperature and pressure conditions. The efficiency of this transport is critical for ensuring a uniform deposition.
-
Adsorption of Species on the Surface:
- Once the gaseous species reach the substrate, they adsorb onto its surface. This step is influenced by the surface properties of the substrate and the chemical nature of the precursors. Proper adsorption is essential for initiating the subsequent chemical reactions.
-
Heterogeneous Surface-Catalyzed Reactions:
- The adsorbed species undergo chemical reactions on the substrate surface, often catalyzed by the surface itself. These reactions transform the gaseous precursors into the desired solid material. The nature of these reactions determines the composition and properties of the deposited film.
-
Surface Diffusion of Species to Growth Sites:
- After the chemical reactions, the resulting atoms or molecules diffuse across the surface to find suitable growth sites. This diffusion process helps in the formation of a uniform and continuous film.
-
Nucleation and Growth of the Film:
- The diffused species nucleate at specific sites on the substrate, forming small clusters that grow into a continuous film. The nucleation and growth rates are influenced by factors such as temperature, pressure, and the concentration of reacting species.
-
Desorption of Gaseous Reaction Products and Transportation Away from the Surface:
- As the film grows, gaseous by-products are formed and desorb from the surface. These by-products are then transported away from the reaction zone to prevent contamination and ensure the purity of the deposited film.
-
Applications and Importance of CVD:
- CVD is used in a variety of applications, including the deposition of magnetic coatings on computer hard drives, the growth of carbon nanotubes, and the production of high-quality optical coatings. Its ability to produce nano-scale layers makes it a key technology in the field of nanotechnology.
-
Variations and Specific Processes:
- There are several variations of the CVD process, such as low-pressure CVD (LPCVD) and plasma-enhanced CVD (PECVD), each tailored for specific applications and materials. For example, in the growth of synthetic diamonds, the CVD method involves the introduction of carbon atoms into an ion gas reactor, where they grow into diamonds at high temperatures and low pressures.
By understanding each of these steps and their significance, one can appreciate the complexity and precision required in the CVD coating process. This knowledge is essential for anyone involved in the procurement or application of CVD equipment and materials, as it directly impacts the quality and performance of the final product.
Summary Table:
Step | Description |
---|---|
Transport of Gaseous Species | Gaseous precursors are introduced and transported to the substrate under controlled conditions. |
Adsorption on Surface | Gaseous species adsorb onto the substrate, initiating chemical reactions. |
Surface-Catalyzed Reactions | Adsorbed species react on the surface, forming the desired solid material. |
Surface Diffusion | Atoms or molecules diffuse across the surface to find growth sites. |
Nucleation and Film Growth | Species nucleate and grow into a continuous film, influenced by temperature and pressure. |
Desorption of By-Products | Gaseous by-products desorb and are removed to ensure film purity. |
Applications | Used in semiconductors, optics, nanotechnology, and more for high-quality coatings. |
Variations | Includes LPCVD, PECVD, and other tailored processes for specific materials and applications. |
Discover how CVD coating can enhance your projects—contact our experts today for tailored solutions!