Hot pressing steel is a manufacturing process that combines heat and pressure to shape and densify steel materials. This method is particularly useful for creating high-strength, durable components with precise dimensions. The process involves heating the steel to a temperature below its melting point, applying significant pressure to deform it, and then cooling it to achieve the desired properties. Hot pressing is commonly used in industries such as automotive, aerospace, and tool manufacturing, where high-performance materials are essential. The process enhances the mechanical properties of steel, such as hardness, wear resistance, and fatigue strength, making it ideal for demanding applications.
Key Points Explained:
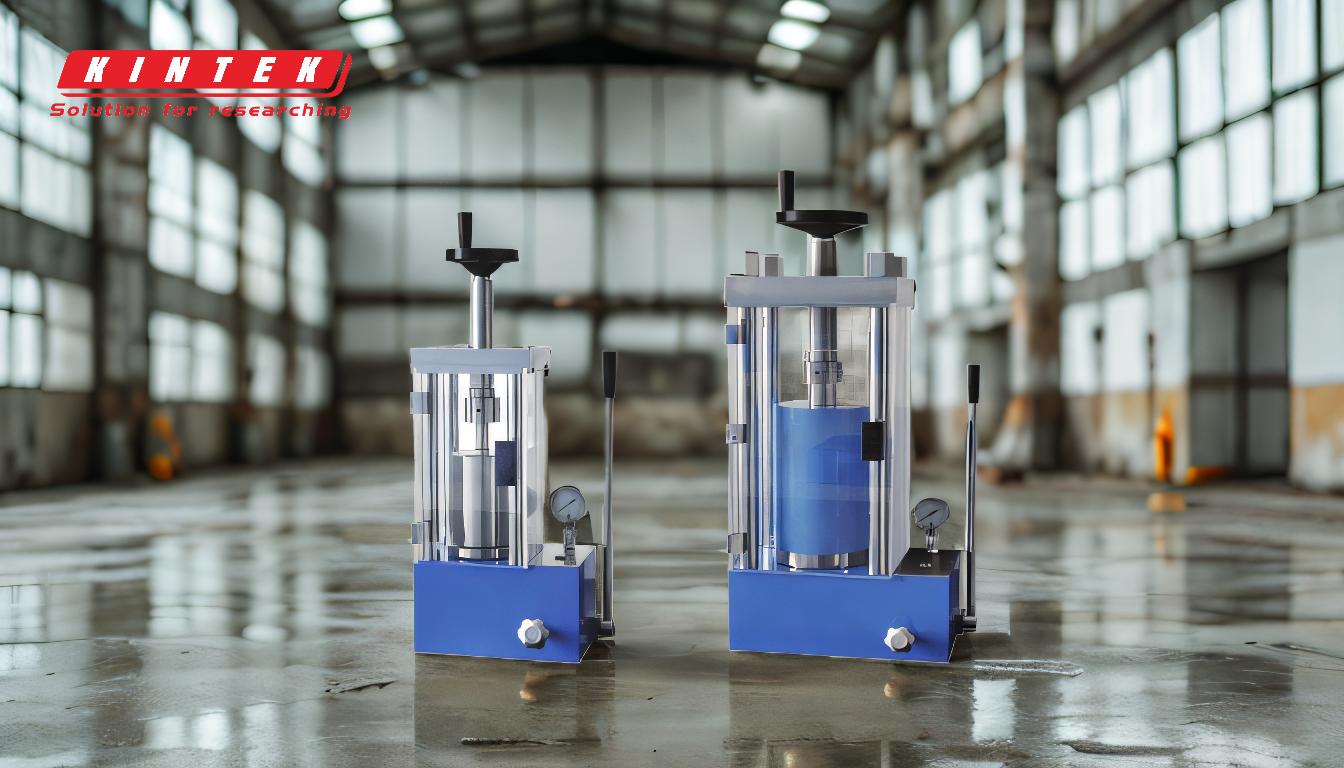
-
Definition and Purpose of Hot Pressing Steel:
- Hot pressing steel is a technique that uses heat and pressure to shape and densify steel materials.
- The primary goal is to produce components with improved mechanical properties, such as increased hardness, wear resistance, and fatigue strength.
- This process is particularly beneficial for applications requiring high-performance materials, such as in the automotive and aerospace industries.
-
Temperature and Heating Process:
- The steel is heated to a temperature below its melting point, typically in the range of 800°C to 1200°C, depending on the specific alloy and desired properties.
- Heating is usually done in a controlled environment, such as a furnace, to ensure uniform temperature distribution throughout the material.
- The temperature must be carefully controlled to avoid overheating, which could lead to undesirable microstructural changes or melting.
-
Application of Pressure:
- Once the steel reaches the desired temperature, significant pressure is applied using hydraulic or mechanical presses.
- The pressure helps to deform the steel, allowing it to take the shape of the die or mold used in the process.
- The amount of pressure applied depends on the specific requirements of the component being produced, but it is generally in the range of 50 to 500 MPa.
-
Cooling and Solidification:
- After the pressing process, the steel is cooled at a controlled rate to achieve the desired microstructure and mechanical properties.
- Cooling can be done in air, oil, or water, depending on the specific alloy and the desired outcome.
- Rapid cooling (quenching) can increase hardness, while slower cooling (annealing) can improve ductility and reduce internal stresses.
-
Advantages of Hot Pressing Steel:
- Improved Mechanical Properties: Hot pressing enhances the strength, hardness, and wear resistance of steel, making it suitable for high-stress applications.
- Precision and Consistency: The process allows for the production of components with precise dimensions and consistent quality.
- Material Efficiency: Hot pressing can reduce material waste by enabling the production of near-net-shape components, which require minimal machining.
-
Applications of Hot Pressed Steel:
- Automotive Industry: Used for manufacturing gears, bearings, and other high-stress components.
- Aerospace Industry: Ideal for producing lightweight, high-strength parts such as turbine blades and structural components.
- Tool Manufacturing: Commonly used to create durable cutting tools, dies, and molds.
-
Considerations for Purchasers:
- Material Selection: Choose the appropriate steel alloy based on the specific application and required properties.
- Equipment Requirements: Ensure that the hot pressing equipment can achieve the necessary temperature and pressure levels.
- Quality Control: Implement strict quality control measures to ensure the consistency and reliability of the hot-pressed components.
By understanding the process and benefits of hot pressing steel, purchasers can make informed decisions when selecting materials and equipment for their specific applications. This method offers a reliable way to produce high-performance steel components that meet the demanding requirements of various industries.
Summary Table:
Aspect | Details |
---|---|
Process | Combines heat and pressure to shape and densify steel materials. |
Temperature Range | 800°C to 1200°C, below the melting point. |
Pressure Range | 50 to 500 MPa, applied via hydraulic or mechanical presses. |
Cooling Methods | Air, oil, or water, depending on desired properties. |
Key Benefits | Improved hardness, wear resistance, precision, and material efficiency. |
Applications | Automotive, aerospace, and tool manufacturing. |
Purchaser Tips | Choose the right alloy, ensure equipment capabilities, and implement QC. |
Discover how hot pressing steel can enhance your manufacturing process—contact our experts today!