Induction melting is a highly efficient and precise method for melting metals, particularly those that are reactive or require a controlled atmosphere. The process involves using electromagnetic induction to generate heat within the metal, which is contained in a crucible surrounded by an induction coil. This method is especially useful for metals and alloys that cannot be melted in air due to their affinity for oxygen and nitrogen. The vacuum induction melting process, in particular, takes place in a vacuum chamber to remove gas impurities and refine the metal. The process includes several key steps: preparing the crucible and charge, melting and refining the metal, and pouring the molten metal. Induction melting offers rapid and uniform heating, precise temperature control, and is suitable for a wide range of metals, making it a versatile and essential technology in metallurgy.
Key Points Explained:
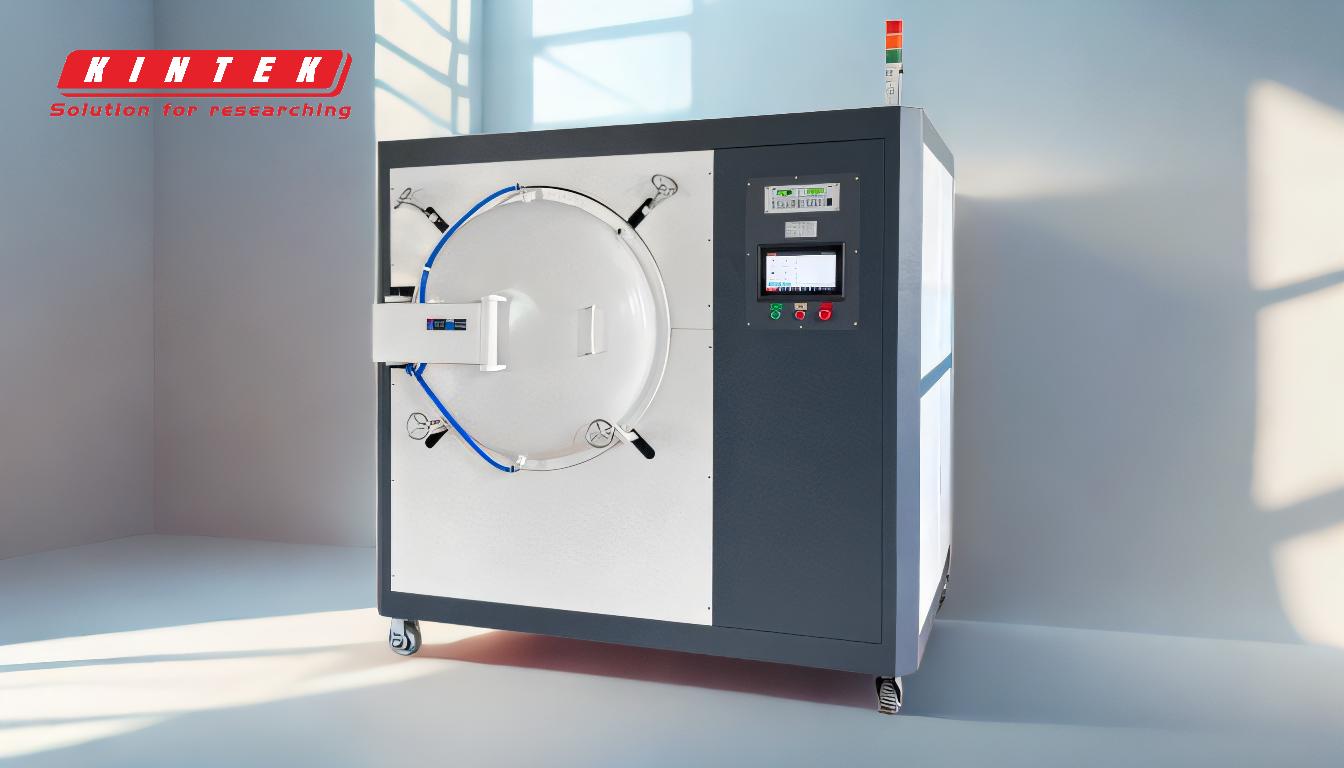
-
Electromagnetic Induction Heating:
- Induction melting relies on electromagnetic induction to generate heat within the metal. When an alternating current flows through the induction coil surrounding the crucible, it creates a magnetic field. This magnetic field induces eddy currents within the metal, which generate heat due to electrical resistance. The heat accumulates until the metal reaches its melting point.
- This method ensures rapid and uniform heating, which is crucial for efficient melting and precise temperature control. It is particularly beneficial for metals that require a controlled environment to prevent oxidation or contamination.
-
Vacuum Environment:
- In vacuum induction melting, the process takes place inside a vacuum chamber. This environment is essential for melting metals and alloys that are highly reactive with oxygen and nitrogen, such as titanium and nickel-based superalloys.
- The vacuum removes gas impurities from the metal, resulting in a purer final product. Additionally, the vacuum environment allows for better control over the alloy chemistry, as it prevents unwanted reactions with atmospheric gases.
-
Crucible Preparation and Charge Loading:
- The crucible, which holds the metal, is typically lined with refractory materials to withstand high temperatures and chemical reactions. Proper preparation of the crucible is crucial to ensure its longevity and the quality of the melt.
- The solid metal raw materials, known as the charge, are carefully selected and loaded into the crucible. The charge may include scrap metal, ingots, or other forms of the metal to be melted.
-
Melting and Refining:
- Once the charge is loaded, the induction furnace is activated, and the metal begins to melt. The electromagnetic stirring effect caused by the induction process helps to homogenize the metal, ensuring a uniform composition.
- During the melting process, refining may occur, where impurities are removed, and the metal's composition is adjusted to meet specific requirements. This step is critical for producing high-quality alloys with precise chemical compositions.
-
Pouring and Casting:
- After the metal has been melted and refined, it is ready for pouring. The molten metal is poured into molds to create ingots, billets, or other desired shapes.
- The pouring process must be carefully controlled to ensure the metal fills the molds evenly and solidifies without defects. This step is crucial for producing high-quality castings with the desired mechanical properties.
-
Advantages of Induction Melting:
- Efficiency and Precision: Induction melting offers rapid heating and precise temperature control, making it an efficient method for melting metals. The electromagnetic stirring effect ensures a uniform melt, which is essential for producing high-quality alloys.
- Versatility: Induction furnaces can handle a wide range of metals, including copper, aluminum, iron, and steel. This versatility makes induction melting suitable for various industries, from aerospace to automotive.
- Clean and Controllable: Induction furnaces are clean and highly controllable, with minimal emissions and waste. They are available in various sizes, making them suitable for both small and large-scale operations.
-
Maintenance and Repair:
- Over time, the crucible and induction coil may require maintenance or repair due to wear and tear. The repair process depends on the extent of damage:
- Full Repair: If the crucible wall is uniformly eroded to about 70 mm, the damaged areas are scraped off, and a new refractory lining is applied using quartz sand. The furnace is then heated to cure the new lining.
- Partial Repair: For smaller cracks or erosion, the damaged areas are scraped off, and the charge is fixed with a steel plate. Quartz sand is then used to fill the gaps, and the area is compacted before the furnace is heated.
- Over time, the crucible and induction coil may require maintenance or repair due to wear and tear. The repair process depends on the extent of damage:
In summary, induction melting is a sophisticated and efficient process for melting metals, particularly those that require a controlled atmosphere. The vacuum induction melting process, in particular, offers significant advantages in terms of purity and control over alloy chemistry. The process involves several key steps, from preparing the crucible and charge to melting, refining, and pouring the molten metal. Induction melting is versatile, clean, and highly controllable, making it an essential technology in modern metallurgy.
Summary Table:
Key Steps | Details |
---|---|
Electromagnetic Induction | Generates heat via eddy currents for rapid, uniform heating. |
Vacuum Environment | Removes gas impurities, ideal for reactive metals like titanium. |
Crucible Preparation | Lined with refractory materials to withstand high temperatures. |
Melting & Refining | Ensures uniform composition and removes impurities. |
Pouring & Casting | Molten metal is poured into molds for high-quality castings. |
Advantages | Efficient, precise, versatile, and clean with minimal emissions. |
Maintenance & Repair | Includes full or partial repairs for crucible and induction coil. |
Learn how induction melting can revolutionize your metal processing—contact our experts today!