Physical Vapor Deposition (PVD) is a sophisticated vacuum-based coating process used to create thin, durable, and functional films on substrates. The process involves vaporizing a solid material in a vacuum, transporting the vaporized atoms or molecules to the substrate, and depositing them to form a thin, bonded layer. PVD is widely used to enhance the appearance, durability, and functionality of parts in industries such as automotive, aerospace, medical devices, and consumer electronics. The process typically involves steps such as vaporization, migration, and deposition, often enhanced by reactive gases to modify the coating's properties.
Key Points Explained:
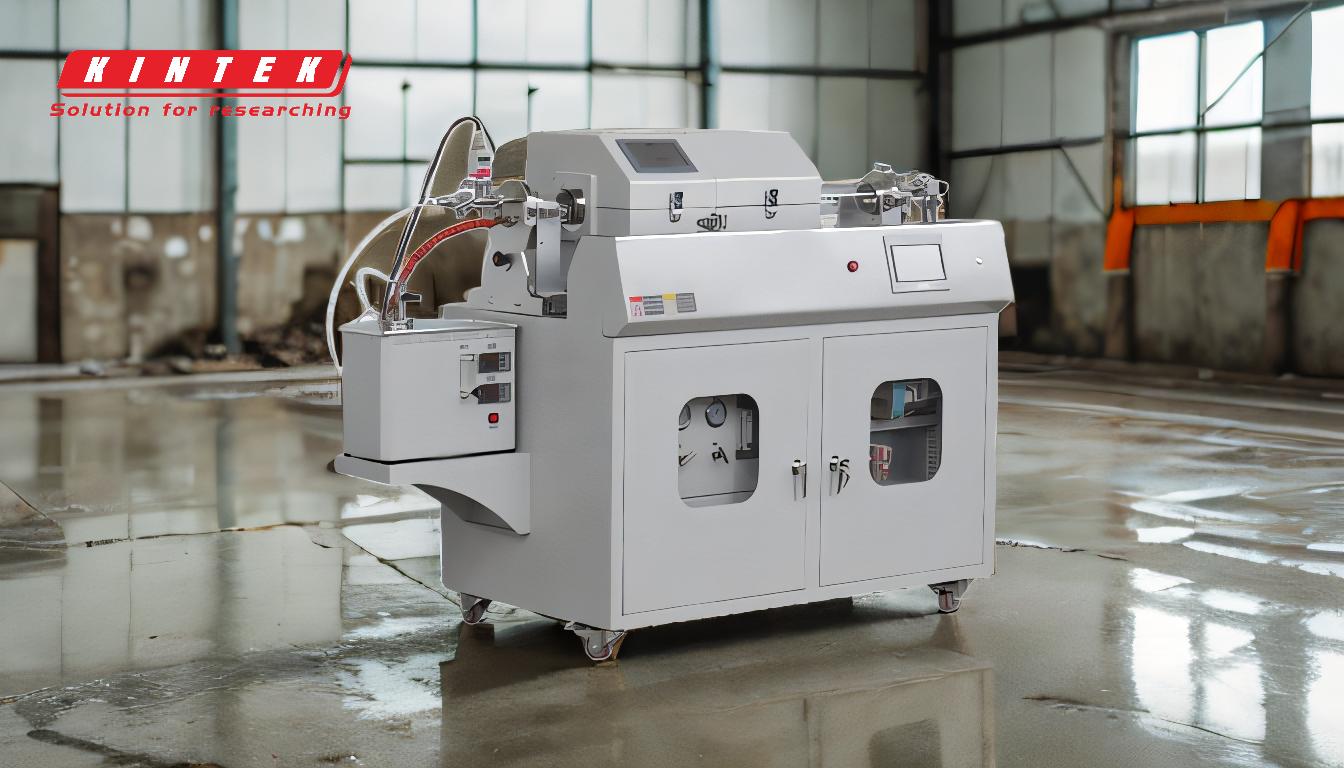
-
Overview of PVD Finishing
- PVD is a vacuum-based thin-film deposition process.
- It involves converting a solid material into vapor and then depositing it onto a substrate to form a thin, uniform layer.
- The process is performed under high-vacuum conditions to ensure cleanliness and precision.
-
Key Steps in the PVD Process
The PVD process can be broken down into several critical steps:-
Vaporization of the Coating Material:
- The solid material (target) is vaporized using techniques such as:
- Evaporation: Heating the material until it vaporizes.
- Sputtering: Bombarding the target with high-energy ions to dislodge atoms.
- Cathodic Arc: Using an electric arc to vaporize the material.
- This step occurs in a vacuum chamber to prevent contamination.
- The solid material (target) is vaporized using techniques such as:
-
Migration of Vaporized Atoms or Molecules:
- The vaporized material travels through the vacuum chamber toward the substrate.
- Reactive gases (e.g., nitrogen, oxygen) can be introduced to modify the coating's composition, such as forming metal nitrides or oxides.
-
Deposition onto the Substrate:
- The vaporized atoms or molecules condense onto the substrate, forming a thin, uniform layer.
- The substrate is typically held at a lower temperature to ensure proper adhesion and film formation.
-
Vaporization of the Coating Material:
-
Techniques Used in PVD
PVD employs various methods to vaporize the target material, each with unique advantages:-
Evaporation:
- Uses a heated crucible or electron beam to vaporize the material.
- Suitable for materials with low melting points.
-
Sputtering:
- Involves bombarding the target with ions to eject atoms.
- Ideal for materials with high melting points and complex compositions.
-
Cathodic Arc:
- Generates a high-energy arc to vaporize the target.
- Produces highly ionized vapor, resulting in dense and adherent coatings.
-
Evaporation:
-
Role of Reactive Gases
- Reactive gases like nitrogen, oxygen, or acetylene are often introduced during the PVD process.
- These gases react with the vaporized material to form compounds such as:
- Metal Nitrides (e.g., titanium nitride for gold-colored coatings).
- Metal Oxides (e.g., aluminum oxide for wear resistance).
- The addition of reactive gases enhances the coating's properties, such as hardness, corrosion resistance, and aesthetic appeal.
-
Advantages of PVD Finishing
- Durability: PVD coatings are highly resistant to wear, corrosion, and scratching.
- Uniformity: The vacuum environment ensures a consistent and uniform coating.
- Versatility: Suitable for a wide range of materials, including metals, ceramics, and polymers.
- Environmental Friendliness: PVD is a clean process with minimal waste and no harmful byproducts.
-
Applications of PVD Coatings
- Automotive: Used for decorative and functional coatings on components like wheels, trim, and engine parts.
- Aerospace: Enhances the performance and longevity of turbine blades and other critical components.
- Medical Devices: Provides biocompatible and wear-resistant coatings for surgical instruments and implants.
- Consumer Electronics: Improves the durability and appearance of smartphone casings, watch components, and more.
-
Considerations for Equipment and Consumable Purchasers
- Vacuum Chamber Quality: Ensure the chamber is designed for high-vacuum conditions to maintain coating consistency.
- Target Material Selection: Choose high-purity targets to achieve the desired coating properties.
- Reactive Gas Compatibility: Verify that the system can handle the required gases for compound formation.
- Substrate Preparation: Proper cleaning and pretreatment of substrates are crucial for optimal adhesion.
- Process Control: Advanced systems with precise temperature, pressure, and power controls are essential for high-quality coatings.
In summary, PVD finishing is a highly controlled and versatile process that transforms solid materials into durable, functional, and aesthetically pleasing coatings. By understanding the steps, techniques, and considerations involved, equipment and consumable purchasers can make informed decisions to achieve the desired results for their specific applications.
Summary Table:
Aspect | Details |
---|---|
Process Overview | Converts solid material into vapor, deposits it on a substrate in a vacuum. |
Key Steps | Vaporization, migration, deposition, often enhanced with reactive gases. |
Techniques | Evaporation, sputtering, cathodic arc. |
Advantages | Durability, uniformity, versatility, environmental friendliness. |
Applications | Automotive, aerospace, medical devices, consumer electronics. |
Purchasing Considerations | Vacuum chamber quality, target material, reactive gas compatibility, substrate prep, process control. |
Discover how PVD coatings can enhance your products—contact our experts today for tailored solutions!