Sintering bonding is a critical process in materials science and manufacturing, particularly in powder metallurgy and ceramic production. It involves transforming powdered materials into dense, solid bodies by applying heat and pressure below the material's melting point. This process creates strong, durable, and low-porosity materials through atomic diffusion and particle fusion. The sintering process can be broken down into several key stages, including powder preparation, compression, heating, particle merging, and solidification. Each step plays a vital role in achieving the desired material properties, such as strength, durability, and structural integrity.
Key Points Explained:
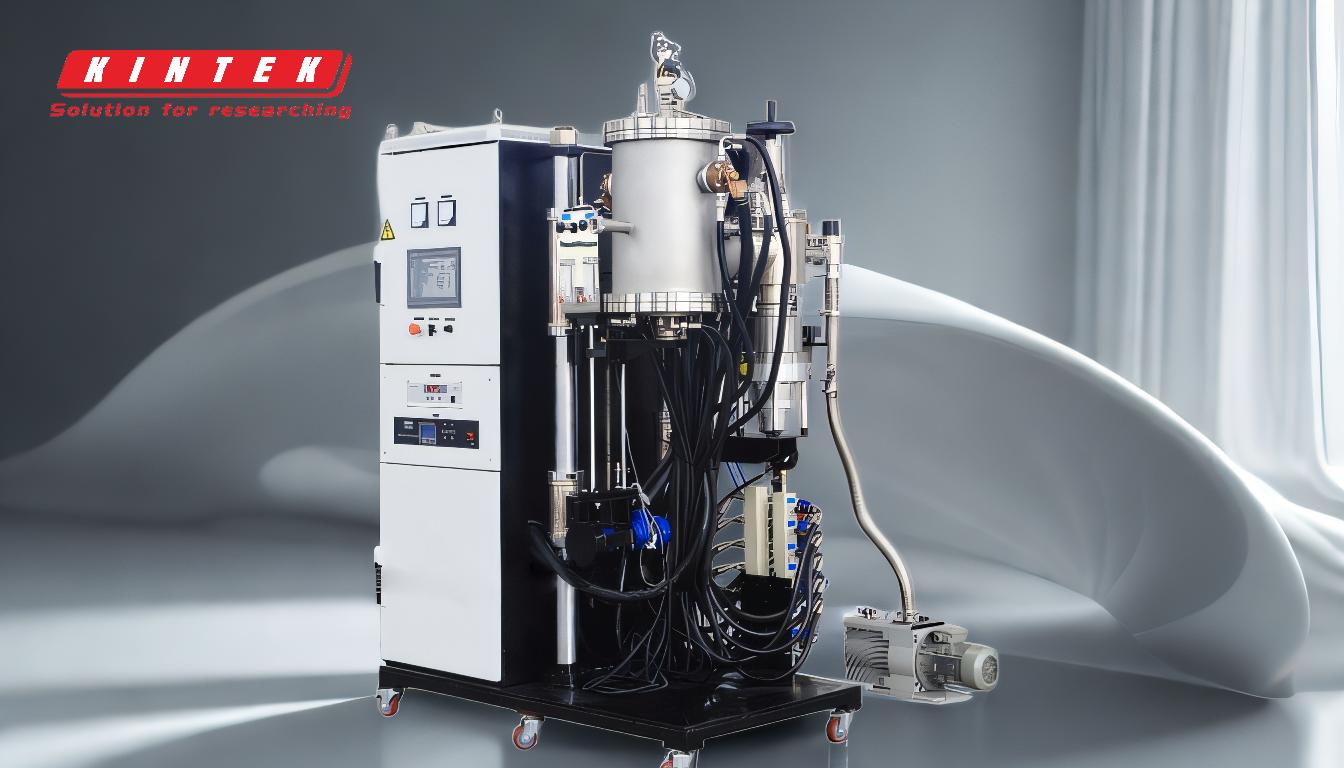
-
Powder Preparation
- The process begins with the preparation of the powder compact, which involves creating a uniform mixture of powdered materials and coupling agents.
- Methods for powder preparation include cold welding, 3D-printed lasers, or pressing tools, often performed in a controlled atmosphere to prevent contamination.
- The goal is to ensure the powder particles are evenly distributed and properly shaped for the next steps.
-
Compression
- The prepared powder is then compressed into the desired shape using high-pressure tools or molds.
- This step ensures the powder particles are tightly packed, reducing porosity and creating a cohesive structure.
- Temporary binders may be used during compression to hold the powder in place before sintering.
-
Heating and Consolidation
- The compressed powder is heated to a temperature just below the material's melting point.
- This activates atomic diffusion, where atoms move across particle boundaries, leading to particle merging and densification.
- In some cases, liquid phase sintering (LPS) is used to accelerate the process by introducing a liquid phase that enhances particle bonding.
-
Particle Merging and Densification
- During heating, the powder particles begin to merge, reducing voids and increasing density.
- This step is critical for achieving the desired mechanical properties, such as strength and durability.
- The process may involve the formation of martensitic crystalline microstructures, which contribute to the material's hardness and wear resistance.
-
Solidification
- After the particles have merged, the material is cooled, allowing it to solidify into a unified mass.
- The cooling rate can influence the final material properties, such as grain size and microstructure.
- The result is a dense, low-porosity material with improved mechanical and thermal properties.
-
Applications and Benefits
- Sintering bonding is widely used in industries such as powder metallurgy, ceramics, and advanced manufacturing.
- It is particularly useful for materials with high melting points, such as tungsten and molybdenum, which are difficult to process using traditional melting methods.
- The process produces materials with excellent strength, durability, and resistance to wear and corrosion.
By following these steps, sintering bonding transforms powdered materials into high-performance components, making it an essential process in modern manufacturing.
Summary Table:
Stage | Description |
---|---|
Powder Preparation | Uniform mixture of powdered materials and coupling agents, often in a controlled atmosphere. |
Compression | High-pressure tools or molds compress the powder into the desired shape, reducing porosity. |
Heating | Heat applied below melting point activates atomic diffusion, leading to particle merging. |
Particle Merging | Particles merge, reducing voids and increasing density for improved mechanical properties. |
Solidification | Cooling solidifies the material, influencing grain size and microstructure for final properties. |
Applications | Used in powder metallurgy, ceramics, and advanced manufacturing for high-performance materials. |
Discover how sintering bonding can enhance your manufacturing process—contact our experts today!