Thin film production involves depositing a thin layer of material onto a substrate, with processes tailored to the desired application and material properties. The two main categories of deposition methods are Physical Vapor Deposition (PVD) and Chemical Vapor Deposition (CVD), each encompassing various techniques. PVD methods, such as sputtering and thermal evaporation, involve vaporizing a solid material and depositing it onto a substrate. CVD methods, including plasma-enhanced CVD and atomic layer deposition, rely on chemical reactions to form thin films. Additionally, simpler techniques like spin coating and dip coating are used for polymer films. The choice of method depends on factors like material type, film thickness, substrate properties, and application requirements.
Key Points Explained:
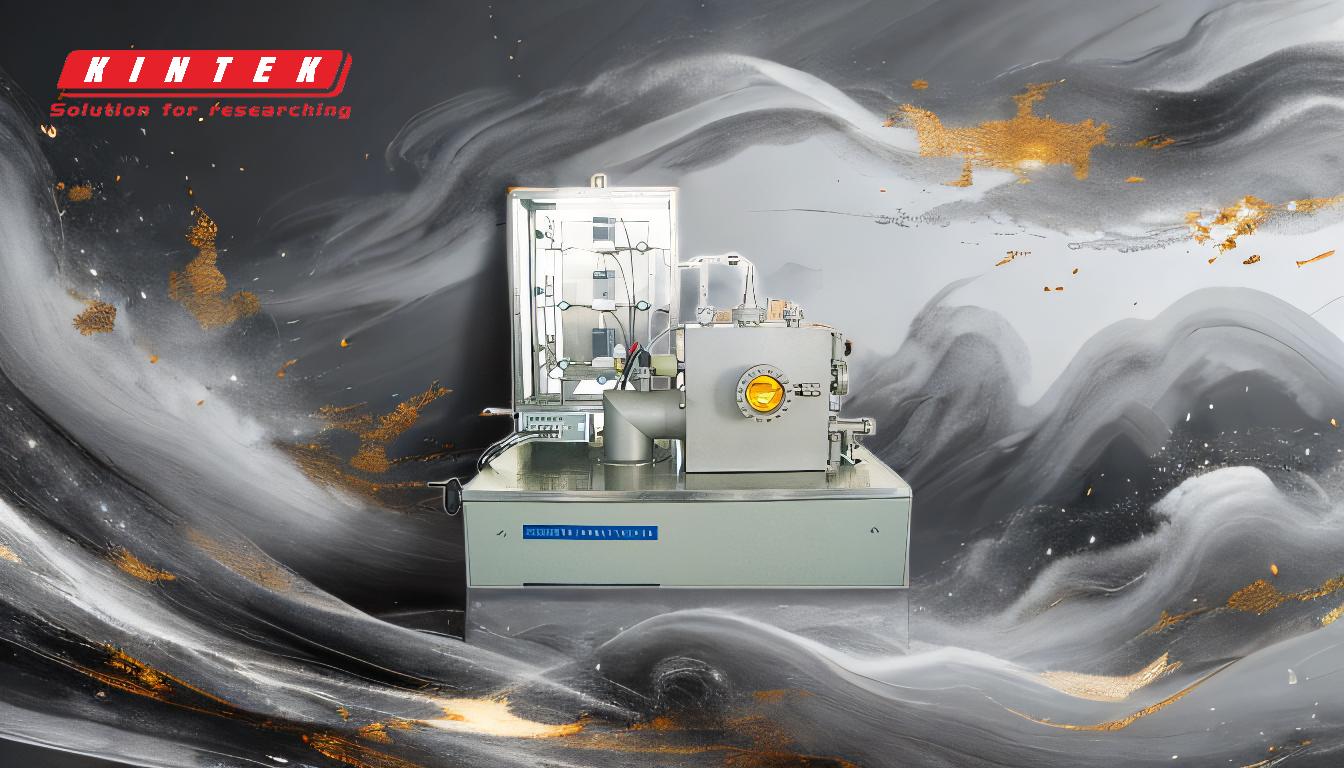
-
Overview of Thin Film Production
- Thin film production involves depositing a thin layer of material onto a substrate.
- The process is critical for applications in semiconductors, optics, solar cells, and OLEDs.
- The choice of deposition method depends on the material, substrate, and desired film properties.
-
Physical Vapor Deposition (PVD)
- PVD involves vaporizing a solid material in a vacuum and depositing it onto a substrate.
- Common PVD techniques include:
- Sputtering: A target material is bombarded with ions, causing atoms to eject and deposit onto the substrate.
- Thermal Evaporation: The material is heated until it vaporizes and condenses onto the substrate.
- Electron Beam Evaporation: An electron beam heats the material to high temperatures for vaporization.
- Pulsed Laser Deposition (PLD): A laser ablates the target material, creating a plume that deposits onto the substrate.
- PVD is suitable for metals, alloys, and ceramics, offering high purity and precise thickness control.
-
Chemical Vapor Deposition (CVD)
- CVD uses chemical reactions to deposit thin films from gaseous precursors.
- Key CVD techniques include:
- Plasma-Enhanced CVD (PECVD): Plasma is used to enhance chemical reactions at lower temperatures.
- Atomic Layer Deposition (ALD): Precursors are introduced sequentially to deposit films one atomic layer at a time.
- Low-Pressure CVD (LPCVD): Reactions occur at reduced pressure for better uniformity.
- CVD is ideal for producing high-purity, conformal coatings, especially for semiconductors and dielectrics.
-
Solution-Based Deposition Methods
- These methods are commonly used for polymer films and simpler applications.
- Techniques include:
- Spin Coating: A solution is applied to a substrate, which is then spun at high speed to spread the material evenly.
- Dip Coating: The substrate is immersed in a solution and withdrawn at a controlled speed to form a thin film.
- Sol-Gel: A colloidal solution (sol) is applied to the substrate and gelified to form a solid film.
- These methods are cost-effective and suitable for large-area coatings.
-
Factors Influencing Thin Film Properties
- Substrate Properties: Surface roughness, cleanliness, and material compatibility affect film adhesion and quality.
- Deposition Parameters: Temperature, pressure, and deposition rate influence film thickness, uniformity, and microstructure.
- Material Properties: The choice of material (e.g., metal, polymer, ceramic) determines the deposition method and film characteristics.
- Post-Deposition Treatments: Annealing or etching may be required to achieve desired film properties.
-
Applications of Thin Films
- Semiconductors: Thin films are used in transistors, diodes, and integrated circuits.
- Optics: Anti-reflective coatings and mirrors rely on precise thin film deposition.
- Energy: Thin films are critical for solar cells and fuel cells.
- Displays: OLEDs and flexible electronics utilize thin polymer films.
-
Emerging Trends in Thin Film Production
- Flexible Electronics: Development of thin films for bendable and stretchable devices.
- Nanostructured Films: Use of techniques like ALD to create films with nanoscale precision.
- Sustainable Methods: Research into eco-friendly deposition techniques and materials.
By understanding these key points, a purchaser can evaluate the most suitable thin film production method for their specific application, ensuring optimal performance and cost-effectiveness.
Summary Table:
Method | Key Techniques | Applications |
---|---|---|
Physical Vapor Deposition (PVD) | Sputtering, Thermal Evaporation, Electron Beam Evaporation, Pulsed Laser Deposition | Metals, alloys, ceramics; high purity, precise thickness control |
Chemical Vapor Deposition (CVD) | Plasma-Enhanced CVD, Atomic Layer Deposition, Low-Pressure CVD | Semiconductors, dielectrics; high-purity, conformal coatings |
Solution-Based Methods | Spin Coating, Dip Coating, Sol-Gel | Polymer films, large-area coatings; cost-effective |
Looking for the best thin film production method for your application? Contact our experts today!