Vacuum arc degassing (VAD) is a specialized process used in metallurgy to refine molten steel by removing dissolved gases and impurities. This process involves creating a vacuum environment to lower the pressure, which reduces the solubility of gases like hydrogen and oxygen in the molten metal. The gases are then expelled from the molten steel, resulting in a cleaner and higher-quality material. The process typically includes steps such as preparing the furnace, heating the metal, creating a vacuum, degassing, and cooling the metal before removing it from the furnace.
Key Points Explained:
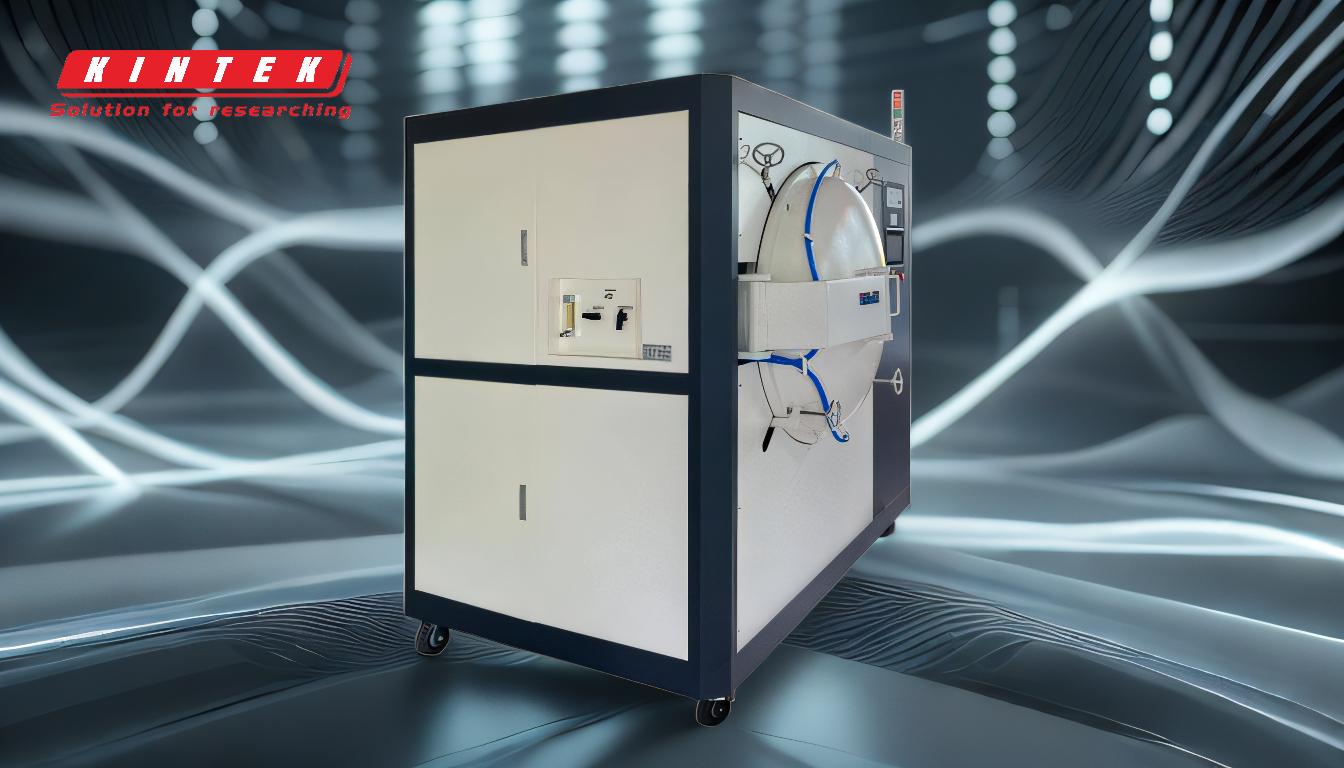
-
Preparation of the Furnace:
- Before the vacuum arc degassing process begins, the furnace must be prepared. This involves cleaning the furnace chamber to remove any residual soot, grit, or splash metal from previous operations. The copper mould, which is used to shape the molten metal, is also cleaned and placed back into the mould passage. The sealing cover is tightened to ensure an airtight environment, and the furnace cavity is blown dry to remove any moisture.
-
Heating the Metal:
- The metal to be treated is heated to a high temperature in the furnace. This step is crucial because it ensures that the metal is in a molten state, which is necessary for the degassing process to be effective. The temperature must be carefully controlled to maintain the metal in a liquid state without causing any unwanted reactions or evaporation of the metal itself.
-
Creating a Vacuum:
- A vacuum is created within the furnace chamber by removing air and other gases. This is typically achieved using vacuum pumps. The vacuum environment is essential because it lowers the pressure inside the chamber, which in turn reduces the solubility of gases like hydrogen and oxygen in the molten metal. This step is critical for the effective removal of these gases.
-
Degassing Process:
- Once the vacuum is established, the degassing process begins. The reduced pressure causes the dissolved gases in the molten metal to become less soluble and separate from the metal. These gases are then forced out of the chamber through the vacuum system. The process continues until the desired level of gas removal is achieved, which is typically monitored using sensors and other analytical tools.
-
Cooling and Removal:
- After the degassing process is complete, the metal is allowed to cool down gradually. This step is important to prevent any thermal stress or cracking in the metal. Once the metal has cooled to a safe temperature, the furnace is opened, and the refined metal is removed. The furnace chamber is then cleaned again in preparation for the next batch of metal.
-
Advantages of Vacuum Arc Degassing:
- The vacuum arc degassing process offers several advantages, including the removal of harmful gases like hydrogen and oxygen, which can cause defects in the final product. It also helps in reducing the levels of impurities and inclusions in the metal, resulting in a higher-quality material. Additionally, the process can be precisely controlled, allowing for consistent results and improved mechanical properties of the metal.
-
Applications of Vacuum Arc Degassing:
- Vacuum arc degassing is widely used in the production of high-quality steel, particularly for applications where the mechanical properties and purity of the metal are critical. This includes the production of aerospace components, automotive parts, and high-performance alloys. The process is also used in the manufacture of specialty steels, such as those used in the construction of nuclear reactors and other high-stress environments.
In summary, vacuum arc degassing is a sophisticated process that plays a crucial role in the production of high-quality steel. By removing dissolved gases and impurities, it enhances the mechanical properties and overall quality of the metal, making it suitable for demanding applications in various industries.
Summary Table:
Step | Description |
---|---|
Preparation | Clean furnace, prepare copper mould, and ensure airtight sealing. |
Heating | Heat metal to molten state for effective degassing. |
Creating a Vacuum | Use vacuum pumps to reduce pressure and gas solubility in molten metal. |
Degassing | Expel dissolved gases under reduced pressure for cleaner steel. |
Cooling & Removal | Cool metal gradually and remove refined steel from the furnace. |
Advantages | Removes harmful gases, reduces impurities, and improves mechanical properties. |
Applications | Aerospace, automotive, high-performance alloys, and specialty steels. |
Discover how vacuum arc degassing can elevate your steel quality—contact us today!