Vacuum quenching is a specialized heat treatment process used to enhance the mechanical properties of metals, particularly steel and alloys. It involves heating the workpiece to a specific temperature in a vacuum environment, holding it at that temperature for a predetermined time, and then rapidly cooling it using a cooling medium such as gas, oil, or water. This process transforms the microstructure of the metal, typically converting austenite to martensite, which increases hardness and strength. The vacuum environment prevents oxidation and contamination, ensuring a clean and precise treatment. The process is widely used in industries requiring high-performance materials, such as aerospace, automotive, and tool manufacturing.
Key Points Explained:
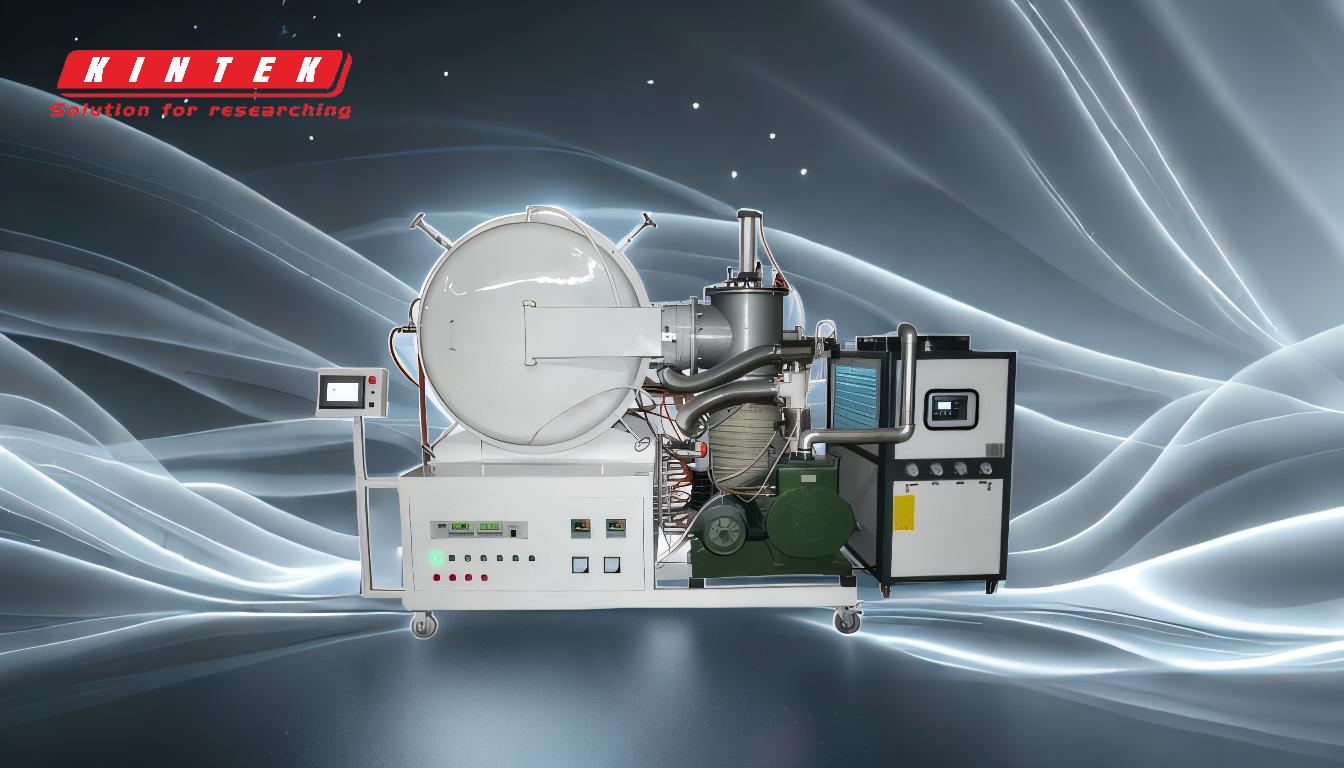
-
Loading the Furnace:
- The first step in vacuum quenching is loading the workpiece into the vacuum chamber. This involves placing the parts, tools, or components into the chamber in a way that ensures even heating and cooling. Proper loading is crucial to achieve uniform properties across the workpiece.
-
Creating a Vacuum:
- Once the workpiece is loaded, the chamber is sealed, and a vacuum is created by removing all oxygen and other gases using a vacuum pump. This step is essential to prevent oxidation and contamination of the workpiece. The vacuum level is maintained throughout the heating and quenching process to ensure a clean environment.
-
Heating the Workpiece:
- The workpiece is then heated to a specific temperature, known as the austenitizing temperature, using precise temperature controls. This temperature varies depending on the type of metal and the desired properties. The workpiece is held at this temperature for a set period to allow the microstructure to fully transform into austenite.
-
Quenching:
- After the heating phase, the workpiece is rapidly cooled using a cooling medium. The choice of cooling medium depends on the material and the desired properties. Common cooling mediums include:
- Gas Quenching: High-purity inert gases like nitrogen or argon are used to cool the workpiece. This method is clean and prevents any chemical reactions that could alter the metal's properties.
- Liquid Quenching: The workpiece is rapidly cooled in a quenching oil bath. This method is more aggressive and is used when a higher cooling rate is required.
- Water Quenching: In some cases, water is used as the cooling medium, especially for materials that require very rapid cooling.
- After the heating phase, the workpiece is rapidly cooled using a cooling medium. The choice of cooling medium depends on the material and the desired properties. Common cooling mediums include:
-
Cooling and Finishing:
- After quenching, the workpiece is further cooled to room temperature. In some cases, additional heat treatment processes like tempering may be applied to reduce brittleness and improve toughness. The final step involves inspecting the workpiece to ensure it meets the required specifications.
-
Types of Quenching Processes:
- Gas Quenching: This involves cooling the workpiece in a high-purity neutral gas after heating in a vacuum. It is commonly used for materials that require a clean and controlled cooling environment.
- Liquid Quenching: This involves rapid cooling in a quenching oil bath after heating. The workpiece is moved to a cooling chamber filled with high-purity nitrogen to prevent oxidation during the cooling process.
-
Equipment and Components:
- The vacuum system in a vacuum furnace includes components such as vacuum valves, mechanical pumps, diffusion pumps, and Roots pumps. These components work together to achieve and maintain the desired vacuum level, which is typically around 7 × 10^-3 Pa. The vacuum cleaning furnace plays a crucial role in ensuring the cleanliness and efficiency of the quenching process.
-
Applications and Benefits:
- Vacuum quenching is widely used in industries that require high-performance materials, such as aerospace, automotive, and tool manufacturing. The benefits include:
- Enhanced Mechanical Properties: Increased hardness, strength, and wear resistance.
- Clean and Precise Treatment: The vacuum environment prevents oxidation and contamination, ensuring a high-quality finish.
- Versatility: The process can be tailored to different materials and cooling requirements, making it suitable for a wide range of applications.
- Vacuum quenching is widely used in industries that require high-performance materials, such as aerospace, automotive, and tool manufacturing. The benefits include:
In summary, vacuum quenching is a highly controlled and precise heat treatment process that enhances the mechanical properties of metals. By using a vacuum environment and carefully selected cooling mediums, it ensures a clean and efficient treatment, making it ideal for high-performance applications.
Summary Table:
Step | Description |
---|---|
Loading the Furnace | Place the workpiece in the vacuum chamber for even heating and cooling. |
Creating a Vacuum | Remove oxygen and gases to prevent oxidation and contamination. |
Heating | Heat to austenitizing temperature for microstructure transformation. |
Quenching | Rapidly cool using gas, oil, or water to achieve desired properties. |
Cooling & Finishing | Cool to room temperature; inspect and apply additional treatments if needed. |
Applications | Aerospace, automotive, and tool manufacturing for high-performance materials. |
Discover how vacuum quenching can optimize your metal treatment—contact our experts today!