An induction furnace is a highly efficient and versatile piece of equipment used primarily for melting metals such as iron, steel, copper, aluminum, and precious metals. Its purpose extends to various industries, including metal recycling, forging, foundry, and heat treatment. The furnace operates on the principle of electromagnetic induction, which generates heat directly within the metal, resulting in a clean, energy-efficient, and well-controlled melting process. Key advantages include fast heating, high production efficiency, minimal oxidation, and precise temperature control. Induction furnaces are essential in modern industrial processes due to their ability to reduce material waste, lower energy consumption, and improve working conditions.
Key Points Explained:
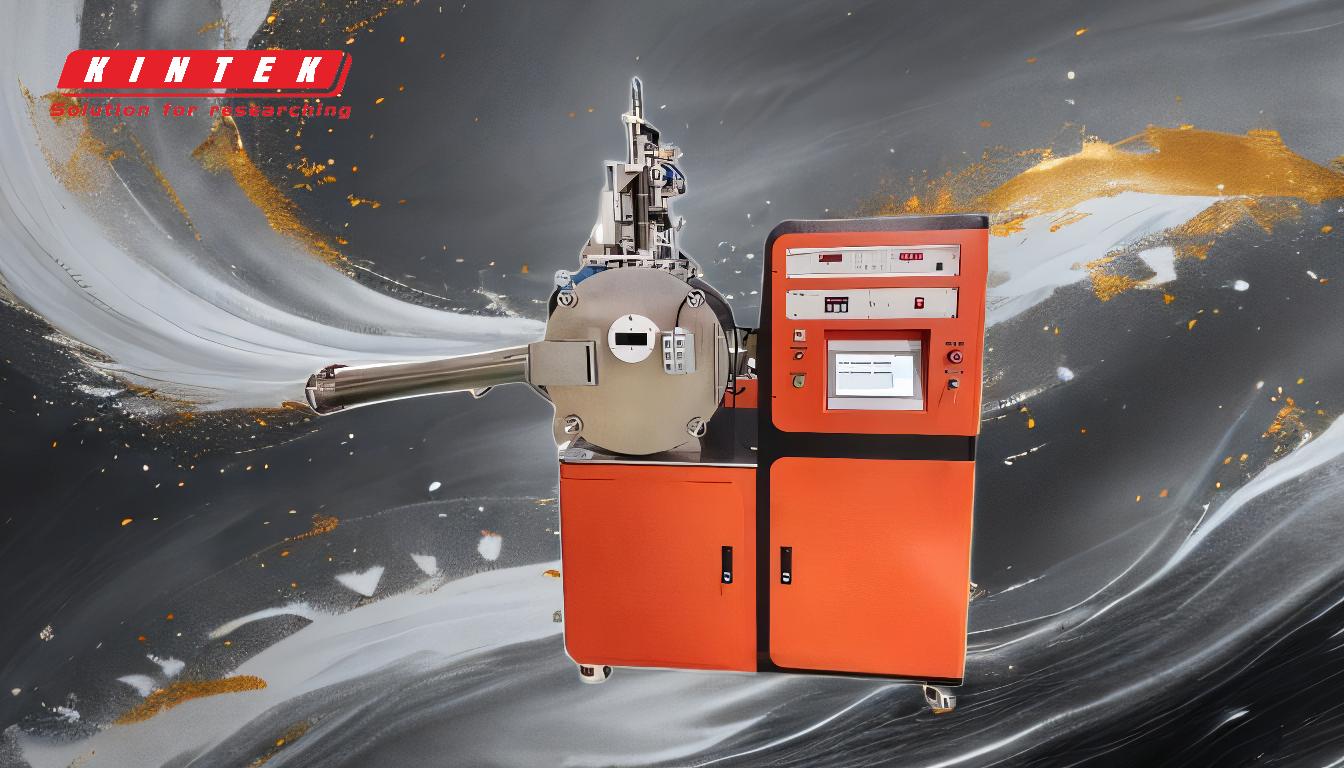
-
Primary Purpose of an Induction Furnace:
- The main purpose of an induction furnace is to melt metals efficiently and precisely. It is widely used in industries such as metal recycling, forging, foundry, and heat treatment. The furnace is capable of melting a wide range of metals, including iron, steel, copper, aluminum, and precious metals, making it a versatile tool in industrial applications.
-
Working Principle:
- Induction furnaces operate on the principle of electromagnetic induction. An alternating current passes through a coil, creating a magnetic field that induces eddy currents within the metal. These currents generate heat, melting the metal without direct contact between the heat source and the material. This method ensures a clean and controlled melting process.
-
Advantages of Induction Furnaces:
- Energy Efficiency: Induction furnaces are highly energy-efficient compared to traditional melting methods, such as coal or gas-fired furnaces. The direct heating of the metal reduces energy loss.
- Fast Heating: The furnace heats metals rapidly, significantly reducing melting time and increasing production efficiency.
- Minimal Oxidation: The process generates less oxidation and decarburization, preserving the quality of the metal and reducing material waste.
- Precise Temperature Control: Induction furnaces offer superior temperature control, ensuring consistent and accurate melting conditions.
- Environmental Benefits: The furnace produces no pollutants, creating a cleaner working environment and improving worker safety.
-
Applications in Various Industries:
- Metal Recycling: Induction furnaces are commonly used in metal recycling systems to remelt and purify scrap metals, making them suitable for reuse.
- Forging Industry: In forging, the furnace heats metal blanks before shaping, ensuring uniform heating and reducing forging die costs.
- Foundry Industry: It is used for remelting and purifying waste metals, often referred to as a medium frequency melting furnace.
- Heat Treatment: Induction furnaces are employed for processes like quenching and tempering, particularly for steel bars, to enhance their mechanical properties.
-
Types of Induction Furnaces:
- Induction furnaces come in various types, including medium frequency heating furnaces, diathermy furnaces, and series resonant medium frequency furnaces. These variations cater to specific industrial needs, such as heating, melting, or heat treatment.
-
IGBT Induction Furnace:
- Modern induction furnaces often use Insulated Gate Bipolar Transistor (IGBT) technology, which enhances efficiency and control. The igbt induction furnace is known for its compact design, high power density, and ability to handle a wide range of frequencies, making it ideal for industrial applications.
-
Operational Benefits:
- Induction furnaces are lightweight, compact, and easy to operate. They require minimal maintenance and provide a superior working environment due to their clean and pollution-free operation.
In summary, the induction furnace is a critical tool in modern industrial processes, offering unmatched efficiency, precision, and environmental benefits. Its applications span multiple industries, making it indispensable for metal melting, recycling, and heat treatment processes.
Summary Table:
Key Aspect | Details |
---|---|
Primary Purpose | Efficient and precise melting of metals like iron, steel, copper, and more. |
Working Principle | Electromagnetic induction heats metal directly, ensuring a clean process. |
Advantages | Energy efficiency, fast heating, minimal oxidation, precise temperature control. |
Applications | Metal recycling, forging, foundry, heat treatment. |
Types | Medium frequency, diathermy, and IGBT induction furnaces. |
Operational Benefits | Lightweight, compact, easy to operate, and pollution-free. |
Ready to enhance your industrial processes with an induction furnace? Contact us today to learn more!