Physical Vapor Deposition (PVD) is a widely used thin-film deposition technique that involves the physical transfer of material from a source to a substrate in a vacuum environment. The process begins with the vaporization of a solid or liquid source material, which is then transported through a low-pressure chamber and deposited onto a substrate, forming a thin film. PVD is commonly used in industries such as semiconductors, optics, and tool coatings due to its ability to produce high-quality, durable, and precise coatings. The method includes various techniques like vacuum thermal evaporation, electron beam evaporation, and arc evaporation, each suited for specific applications.
Key Points Explained:
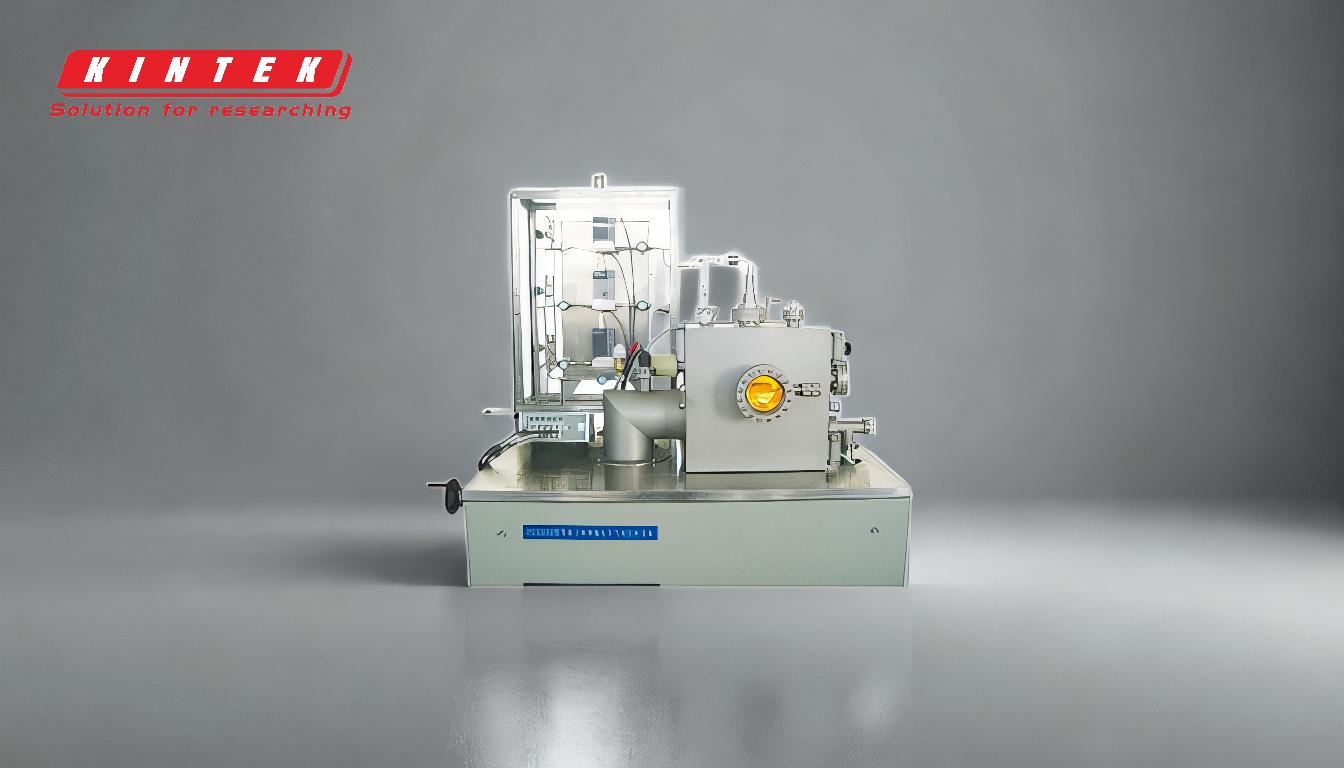
-
What is PVD?
- Physical Vapor Deposition (PVD) is a process where material is physically transferred from a source to a substrate in a vacuum environment. The source material, typically in solid or liquid form, is vaporized into individual atoms or small clusters, which then travel through the vacuum chamber and condense on the substrate to form a thin film. This method is widely used for creating coatings with high precision, durability, and uniformity.
-
How PVD Works:
- Vaporization: The source material (e.g., metal or compound) is vaporized using techniques such as thermal evaporation, electron beam evaporation, or arc evaporation. This step transforms the material into a plasma or gaseous state.
- Transport: The vaporized atoms or molecules travel through a low-pressure vacuum chamber, ensuring minimal contamination and precise deposition.
- Deposition: The vaporized material condenses on the substrate, forming a thin, uniform film. The substrate can be a tool, semiconductor, or any surface requiring a coating.
-
Common PVD Techniques:
- Vacuum Thermal Evaporation: This technique uses heat to vaporize the source material. It is one of the simplest and oldest PVD methods, suitable for materials with low melting points.
- Electron Beam Evaporation: A high-energy electron beam is used to vaporize the source material. This method is ideal for materials with high melting points and provides precise control over the deposition process.
- Arc Evaporation: An electric arc is used to vaporize the source material. This technique is commonly used for depositing hard coatings like titanium nitride (TiN) on cutting tools.
- Laser Beam Evaporation: A laser is used to vaporize the source material, offering high precision and control, especially for complex materials.
- Molecular Beam Epitaxy (MBE): This advanced technique is used for growing high-quality crystalline films, often in semiconductor applications.
- Ion Plating Evaporation: Combines PVD with ion bombardment to enhance film adhesion and density, making it suitable for demanding applications.
-
Applications of PVD:
- Tool Coatings: PVD is widely used to coat cutting tools, molds, and dies with hard, wear-resistant materials like titanium nitride (TiN) and chromium nitride (CrN).
- Semiconductors: PVD is used to deposit thin films of metals and dielectrics in semiconductor manufacturing, enabling the production of integrated circuits and microelectronic devices.
- Optics: PVD is employed to create anti-reflective, reflective, and protective coatings on optical components like lenses and mirrors.
- Decorative Coatings: PVD is used to apply durable, aesthetically pleasing coatings on jewelry, watches, and consumer electronics.
-
Advantages of PVD:
- High-Quality Coatings: PVD produces thin films with excellent adhesion, uniformity, and durability.
- Versatility: PVD can deposit a wide range of materials, including metals, ceramics, and composites.
- Environmentally Friendly: PVD processes typically use fewer hazardous chemicals compared to other coating methods, making them more environmentally sustainable.
- Precision: PVD allows for precise control over film thickness and composition, making it ideal for applications requiring high accuracy.
-
Comparison with Other Deposition Methods:
- PVD differs from Chemical Vapor Deposition (CVD) in that it relies on physical processes (vaporization and condensation) rather than chemical reactions. While CVD often requires higher temperatures and can deposit thicker films, PVD is preferred for applications requiring high precision and lower processing temperatures. For example, microwave plasma chemical vapor deposition is a CVD technique that uses plasma to enhance chemical reactions, making it suitable for depositing materials like diamond films.
In summary, PVD is a versatile and precise thin-film deposition method that plays a critical role in various industries. Its ability to produce high-quality coatings with excellent adhesion and durability makes it a preferred choice for applications ranging from tool coatings to semiconductor manufacturing.
Summary Table:
Aspect | Details |
---|---|
What is PVD? | A vacuum-based process for transferring material to a substrate as a thin film. |
How PVD Works | Vaporization → Transport → Deposition. |
Common Techniques | Vacuum Thermal Evaporation, Electron Beam Evaporation, Arc Evaporation. |
Applications | Tool coatings, semiconductors, optics, decorative coatings. |
Advantages | High-quality, durable, precise, and environmentally friendly coatings. |
Discover how PVD can enhance your applications—contact our experts today!