The Sinter-HIP (Hot Isostatic Pressing) process is a specialized thermal consolidation technique used to produce materials with minimal or no porosity, achieving near-theoretical density. It combines vacuum sintering with the application of high pressure and heat simultaneously, typically using argon gas, to fully consolidate materials such as cemented carbide. This process enhances mechanical properties like strength, fracture toughness, and resistance to wear, corrosion, and deflection. Sinter-HIP is widely used in industries such as aerospace, defense, oil & gas, electronics, and marine for manufacturing high-performance structural and nonstructural components. It is particularly cost-effective for large-scale production and can handle a variety of materials, including ceramics and tool steels.
Key Points Explained:
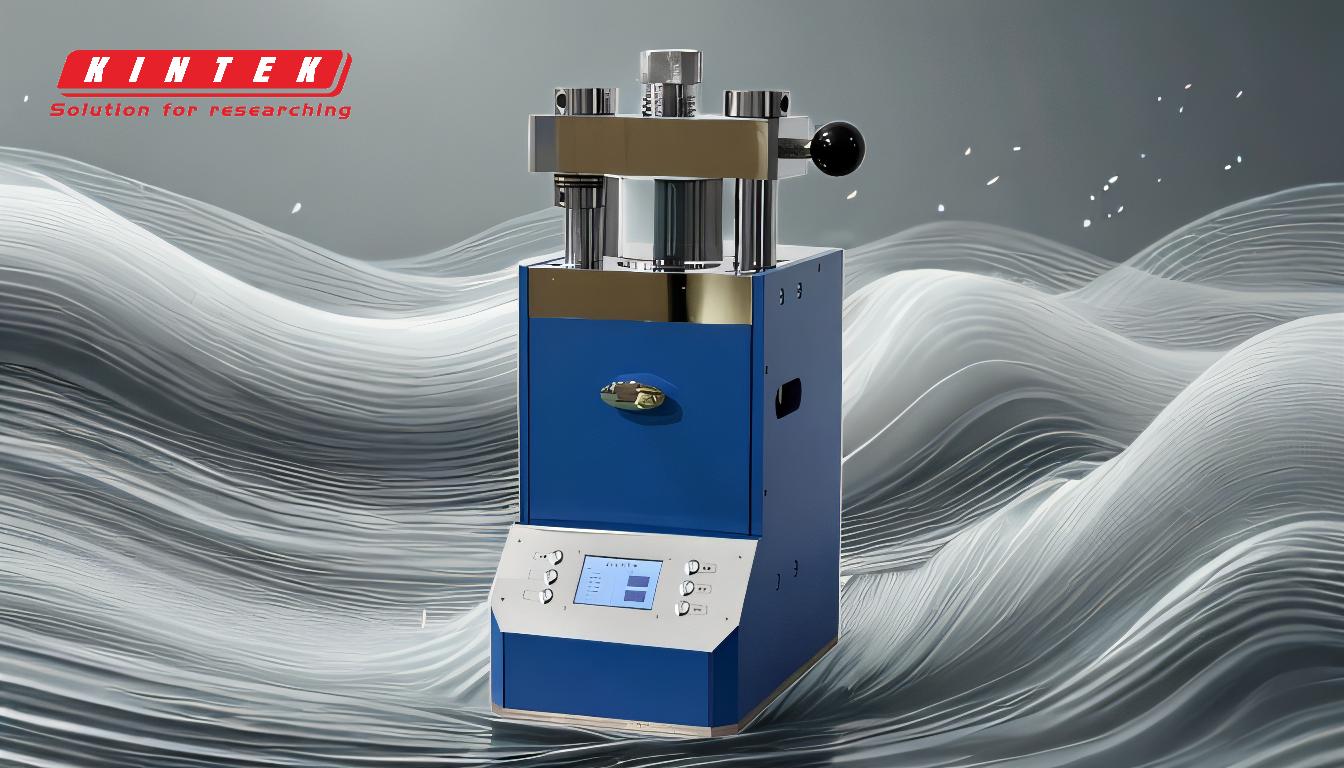
-
Definition and Purpose of Sinter-HIP:
- Sinter-HIP is a thermal consolidation process that combines vacuum sintering with hot isostatic pressing (HIP).
- Its primary purpose is to eliminate porosity in sintered materials, achieving near-full theoretical density.
- This results in components with superior mechanical properties, such as high strength, toughness, and resistance to wear and corrosion.
-
Process Mechanism:
- The process begins with vacuum sintering, where the material is heated in a vacuum to remove gases and bind particles.
- At the end of the sintering phase, the vacuum is replaced with pressurized argon gas, typically at many atmospheres.
- The simultaneous application of heat and pressure consolidates the material, creating a dense, homogeneous structure with minimal porosity.
-
Key Advantages:
- Improved Mechanical Properties: Sinter-HIP enhances transverse rupture strength (400,000-560,000 psi), compressive strength (>600,000 psi), torsional strength, and fracture toughness.
- Elimination of Porosity: The process ensures near-zero porosity, leading to components with high reliability and performance.
- Versatility: It can be applied to a wide range of materials, including cemented carbide, ceramics, and tool steels.
- Cost-Effectiveness: Suitable for large-scale production, making it economically viable for industries requiring high-performance components.
-
Applications Across Industries:
- Aerospace and Defense: Used for manufacturing structural components that require high strength and reliability.
- Oil & Gas: Ideal for producing wear-resistant and corrosion-resistant parts used in harsh environments.
- Electronics: Applied in the production of components requiring high precision and durability.
- Marine: Used for parts exposed to corrosive marine conditions.
-
Material Compatibility:
- Sinter-HIP is effective for materials like cemented carbide, ceramics, and powder metallurgy (PM) tool steels.
- The process can handle both structural and nonstructural components, making it versatile for various industrial applications.
-
Economic and Production Benefits:
- The ability to produce fully dense components in large quantities makes Sinter-HIP a cost-effective solution.
- It reduces the need for secondary processing, saving time and resources in manufacturing.
By combining vacuum sintering with hot isostatic pressing, Sinter-HIP offers a robust solution for producing high-density, high-performance materials across multiple industries. Its ability to eliminate porosity and enhance mechanical properties makes it a preferred choice for applications requiring reliability and durability.
Summary Table:
Aspect | Details |
---|---|
Process | Combines vacuum sintering with hot isostatic pressing (HIP) using argon gas. |
Key Benefits | - Near-zero porosity - Enhanced mechanical properties - Cost-effective for large-scale production. |
Applications | Aerospace, defense, oil & gas, electronics, marine. |
Material Compatibility | Cemented carbide, ceramics, tool steels. |
Economic Advantages | Reduces secondary processing, saving time and resources. |
Learn how the Sinter-HIP process can revolutionize your material production—contact our experts today!